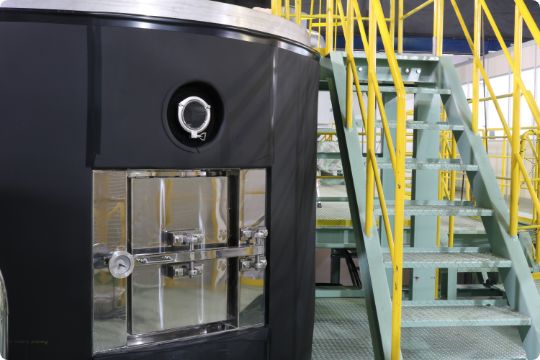
フリーズグラニュレーターにより、
液体から粉体へ受託加工します。
フリーズグラニュレーターを使用した受託粉体加工・試作テストをお引き受けしています。
フリーズグラニュレーション(Freeze Granulation:FG)とは、「凍結造粒」と呼ばれ、原液を噴霧し急速冷却させて凍結体を得る凍結工程と、フリーズドライヤーにて凍結乾燥し乾燥粉体を得る乾燥工程の2工程の組み合わせによる新しい粉体製造方法です。名称は、噴霧凍結乾燥(Spray Freese Drying:SFD)、噴霧凍結造粒乾燥(Spray Freeze Granulation Drying:SFGD)等、様々ですが、当社ではフリーズグラニュレーション(FG:凍結造粒)、または噴霧凍結造粒乾燥(SFGD)としています。特許取得の独自技術により製作された装置により、元来困難であった高濃度・高粘度スラリーの大量処理が可能となりました。得られる粉体の特性はユニークで、中実、均質、低密度な球形顆粒を低温乾燥で製造可能です。
当社では、工業製品を中心に極少量(50mL)から、数十L程度までの原液を処理、粉体加工してユーザー様に提供しています。食品、医薬系でも、開発の支援として、受託研究での粉体試作テストをお引き受けしています。
保有設備
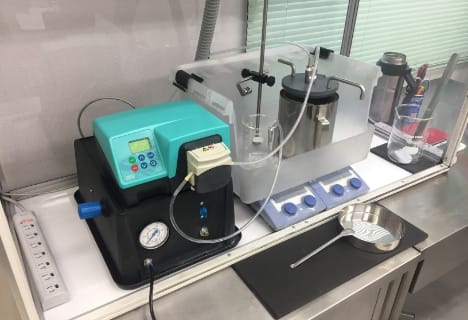
フリーズグラニュレーター LS-6
(Sweden PowderPro社製品)
凍結チャンバー径:φ120mm
噴霧方式:二流体ノズル
最大原液処理速度:6kg/h
冷却温度:-196℃
冷却方式:液化窒素による湿式冷却
設置場所:PTC1
ビーカー内の液化窒素中に噴霧した原液を投入・含侵させて瞬間凍結させます。
装置が小さくコンパクトで、数十~数百mL程度の少量サンプルを多検体で処理する用途に適しています。
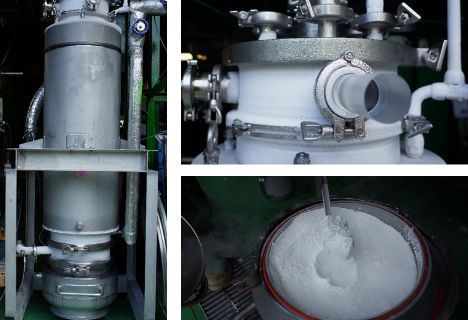
フリーズグラニュレーター CS30
凍結チャンバー径:φ300mm
噴霧方式:二流体ノズル
最大原液処理速度:15kg/h
冷却温度:-10~-120℃
冷却方式:液化窒素の蒸発ガスによる乾式冷却
設置場所:PTC1
ジャケット構造の凍結チャンバー外層に液化窒素を投入することでチャンバー全体を冷却し、熱交換されて気化した窒素ガスをチャンバー内層に投入します。噴霧された原液は、窒素ガスと接触して瞬間凍結します。
冷却固化した凍結体は捕集タンクに溜まり、回収が容易なため、大量生産が可能です。
液化窒素の投入速度調整により、凍結温度の制御が可能です。
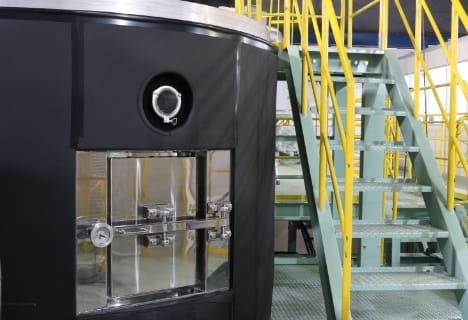
フリーズグラニュレーター CS220
※2023年4月以降受託加工引き受け開始予定
凍結チャンバー径:φ2200mm
噴霧方式:ロータリーアトマイザー、二流体ノズル
最大原液処理速度:20kg/h
冷却温度:-10~-45℃
冷却方式:チラーユニット+熱交換器+ブロワで発生させた冷却大気ガスまたは窒素、アルゴン等の冷却不活性ガス
設置場所:PTC2
下記を目的とした世界に例のない生産用フリーズグラニュレーターを開発しました。
- 液化窒素フリーによるランニングコスト削減
- 液化窒素フリー、電気制御による精密温度設定
- ロータリーアトマイザーでの噴霧による粒子径制御且つシャープな粒度分布
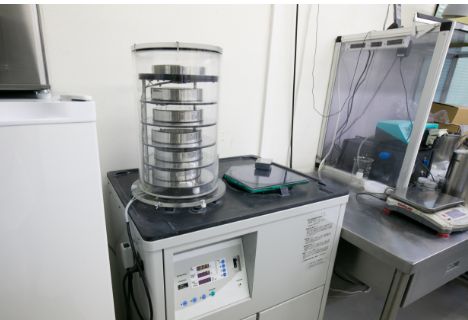
ラボ用フリーズドライヤー FDU-2110
(東京理化器械社製品)
棚容量:700mL × 6段
コールドトラップ容量:3kg
コールドトラップ温度:-80℃
設置場所:PTC1
6段式の特殊多段仕様のため、条件を振った凍結体の乾燥が可能で、少量多品種検体に適しています。
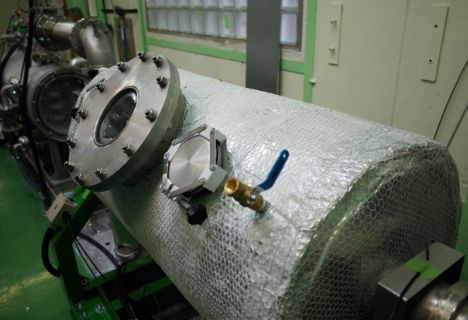
パイロット用フリーズドライヤー TFD-10
乾燥チャンバー容量:85L
コールドトラップ容量:10kg
コールドトラップ温度:-40℃
設置場所:PTC1
チャンバーが揺動することにより、凍結体が効率的且つ均一に乾燥します。
CS30を上部に連結することにより、凍結処理~凍結乾燥までの連続処理が可能です。
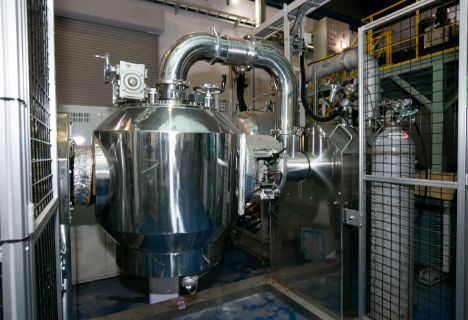
パイロット用フリーズドライヤーRHEOFREED® 160L
(神鋼環境ソリューション社製品)
乾燥チャンバー容量:160L
コールドトラップ容量:30kg
コールドトラップ温度:-45℃
設置場所:PTC2
乾燥チャンバーが回転することにより、凍結体が効率的且つ均一に乾燥します。
棚型乾燥機と比較し、乾燥時間50%以上減、シンプル構造のため、凍結体仕込、乾燥品取出、洗浄時間を大幅短縮することが可能です。
スケールアップによる大型機の製造が可能です。
このような課題はありませんか?
- スプレードライでは熱影響を受けてしまう
- スプレードライでは粒子が中空状になってしまう。
- スプレードライでは粒子が高密度となってしまう。
- フリーズドライでは予備冷凍時に偏析が発生してしまう。
フリーズグラニュレーションのサービス内容全般
- 小型フリーズグラニュレーターによる
少量試作テスト、受託加工 - パイロット、生産用スプレードライヤーに
よる試作テスト、受託加工
ユーザー様に
ご用意頂くもの
- 原液(サンプル)※当社で原液を調製することも可能です。詳細は液体調製へ
- 溶媒(有機溶剤系のみ)原液の処理後に、状況によって少量の溶媒のみを循環送液し、チューブ系内を洗浄します。
- 当社との打ち合わせで必要となった際のご支給品
当社でご用意
させて頂くもの
- フリーズグラニュレーター
- 液化窒素(CS220以外の装置冷却に使用)
- フリーズドライヤー
- イオン交換水
- 送液ポンプ、撹拌機、原液タンク、秤等、業務に必要な小物類
- 回収粉体の梱包用段ボール、ビニール袋、郵送料
- お立会いの際の昼食
- フリーズグラニュレーター使用後の洗浄作業
フリーズグラニュレーションのサンプル
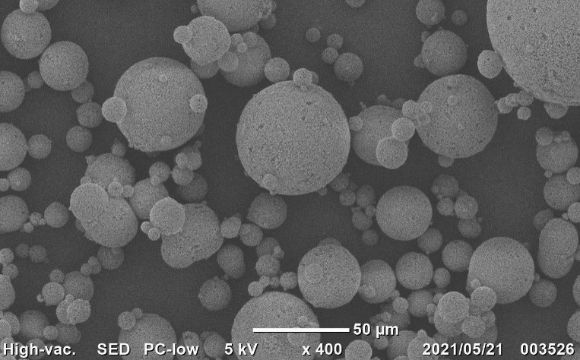
シリカ
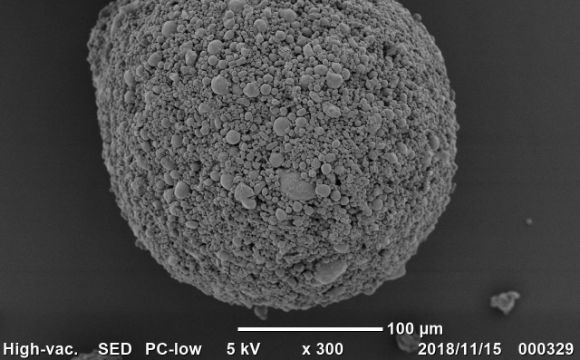
SUS316
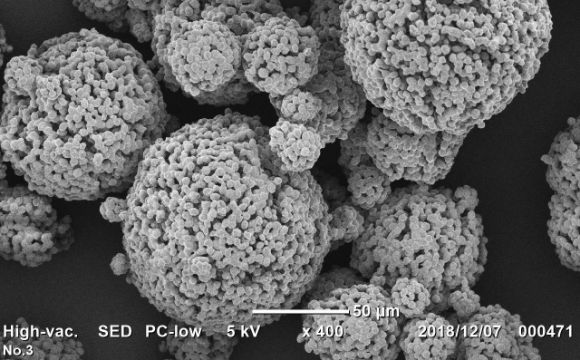
イースト菌
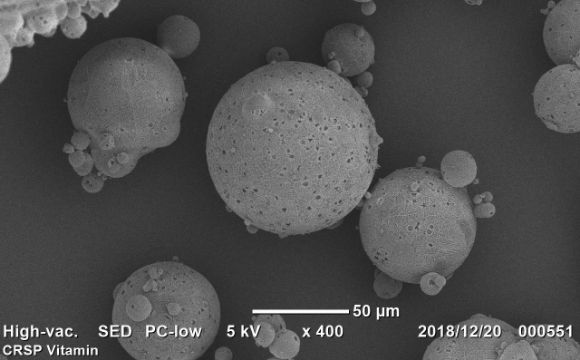
アスコルビン酸+デキストリン
フリーズグラニュレーションの対応品目
適切な保護具の着用により人体に害のない環境を構築できるもの、接粉部SUS304の装置に損害を与えない物性であれば、フリーズグラニュレーション受託加工のトライが可能です。
まずは少量の評価テストから実施し、性能が確認できた際にスケールアップ生産に進むのが通常の流れとなります。
対応例
- セラミックス
- 金属
- 樹脂
- 食品
- 顔料
- 医薬品
- 化成品
- バイオ
フリーズグラニュレーションのノウハウ
スプレードライとの比較
フリーズグラニュレーションは、スプレードライと比較すると下記の特徴があります。
低密度な中実球となる。
スプレードライは、液滴の瞬間乾燥時に溶媒が液滴表面から蒸発すると同時に内部の溶媒が表面に移動することで、液滴全体が収縮しながら液滴内の固形物が外側に移動しながら乾燥粒子となる傾向があります。そのため乾燥粒子の外側の密度が高く内側が密度の低い、中空形状となることがあります。
フリーズグラニュレーションは、液滴を瞬間的に瞬間凍結させることで、溶媒を含め液滴内部構造を固定させます。後工程の凍結乾燥は、長時間を要するため、溶媒の昇華による移動・収縮がないので低密度かつ内部・外部の密度差のない中実球となります。低密度な中実球は、医薬、機能性食品の溶解性の向上や、セラミックス、金属の粉末冶金の特性向上に寄与します。
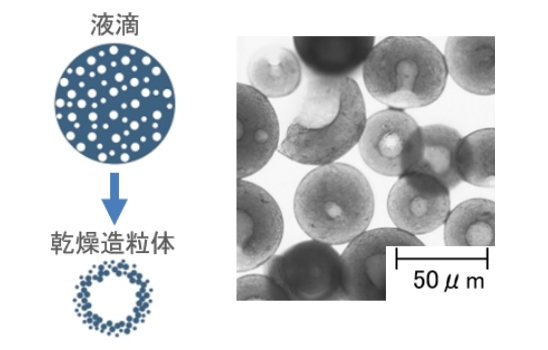
スプレードライ
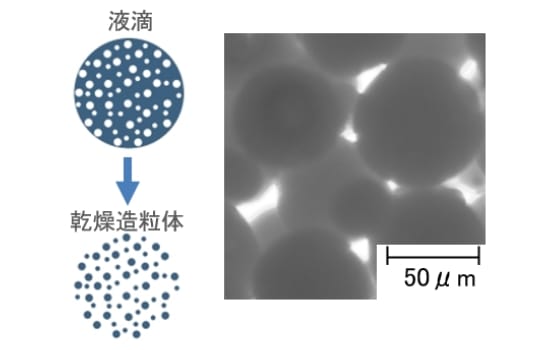
フリーズグラニュレーション
上記のアルミナ顆粒の浸液透光画像では、スプレードライは中空、フリーズグラニュレーションは中実であることが示されています。
低温乾燥による粉体化
スプレードライは、瞬間乾燥でかつ気流により高熱に曝されないタンク等捕集部に数十秒程度で移動するため、熱に弱い物性でも粉体化が可能です。しかし、熱風を乾燥媒体としているため常温以上の熱に曝されることは避けられず、高熱に極めて弱い物性の乾燥は困難です。
フリーズグラニュレーションは、常温以上の熱を全く与えることなく乾燥粉体を得ることができるため、医薬等に適しています。
高いランニングコスト
スプレードライは微細液滴に熱風を接触させて粉体化することに対し、フリーズグラニュレーションは、凍結させてからフリーズドライするため、エネルギーコストが高く、高ランニングコストとなります。当社では液化窒素フリーの装置の開発等、ランニングコストの低下の検討を絶えず実施してきていますが、現状は広範囲な業界・品目の粉体製造に不適で、高付加価値製品の適用に限られています。
大量生産が困難
フリーズグラニュレーションは、近年まで多くても数百g程度の粉体を得る技術でしたが、当社特許技術により、バッチ当たり最大数十kgの粉体を製造することが可能です。世界最大規模の生産設備と自負しており、技術的には数百kgまでのスケールアップが可能です。しかし時間あたりトン単位の粉体を製造できるスプレードライと比較すると大量生産が難しいと言えます。
フリーズドライ+粉砕との比較
フリーズグラニュレーションは、凍結工程と乾燥工程の2工程の組み合わせによる粉体製造法です。類似の粉体製造方法として、「フリーズドライ+粉砕」があります。原液をフリーザーで予備凍結させてからフリーズドライヤーで凍結乾燥させ、粉砕機による処理により粉末化させます。粉砕は凍結乾燥前の予備凍結体で実施することもあります。本手法の代表例として、インスタントコーヒーの製造が挙げられます。
フリーズドライ+粉砕と、フリーズグラニュレーションとの大きな違いは凍結速度にあります。
予備凍結のフリーザーは、一般的には数十分~数時間で原液を凍結固化させるため、溶液であれば凍結中に濃縮による偏析、スラリーであれば更に沈降による偏析も懸念されます。対してフリーズグラニュレーションは、比表面積が増大化した微細液滴をミリセカンドで瞬間凍結させるため、原液が偏析することなく凍結により構造が保持されます。後工程の凍結乾燥にて固形物の移動・収縮がなく溶媒を昇華させるので、原液状態に近しい均質な構造を保持した乾燥粉体となります。
事例1 セラミックス
スプレードライ、フリーズグラニュレーションで調製したアルミナ顆粒を、乾式プレスして成形体・焼成体を作製して密度を評価しました。
SEM画像
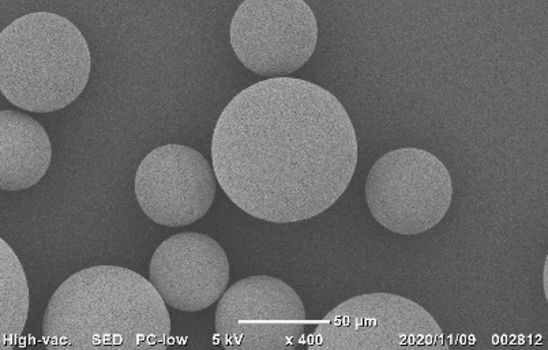
スプレードライ顆粒
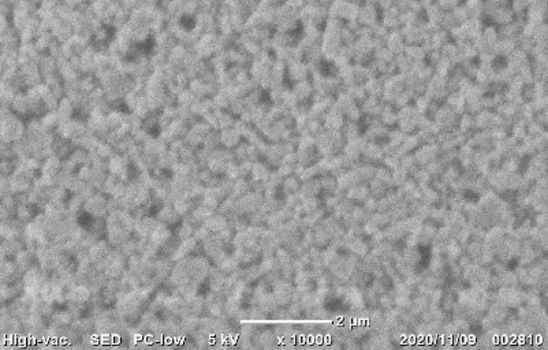
スプレードライ顆粒拡大
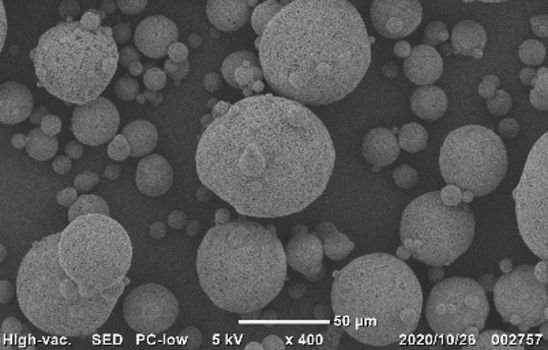
フリーズグラニュレーション顆粒
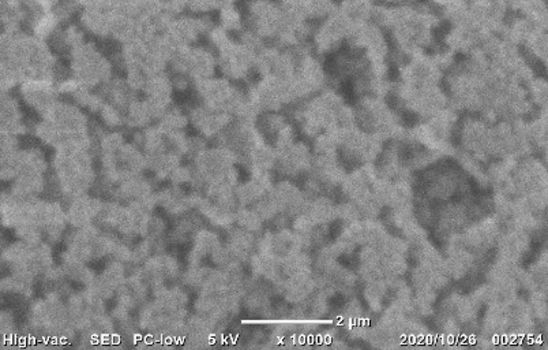
フリーズグラニュレーション顆粒拡大
スプレードライ顆粒は粒度分布がシャープ、フリーズグラニュレーション顆粒はブロードです。これは本試験時のスプレードライはロータリーアトマイザー、フリーズグラニュレーションは二流体ノズル方式であったための違いと考えられます。顆粒の形状はスプレードライがより真球状となっています。拡大写真では、スプレードライ顆粒は一次粒子が密接に凝集していますが、フリーズグラニュレーション顆粒は一次粒子間に空孔が多く、低密度であることが分かります。
成形体・焼成体密度
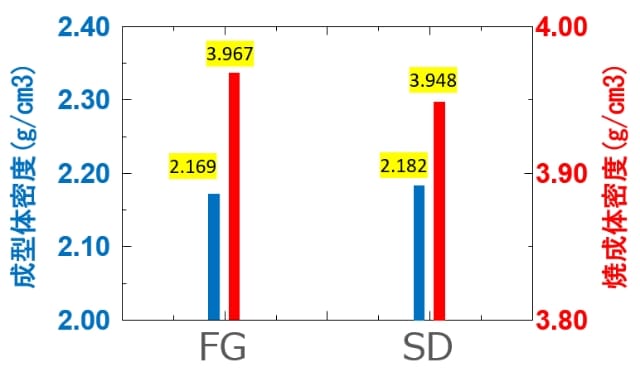
成形体はスプレードライ顆粒の密度が高くなりましたが、焼成後、フリーズグラニュレーション顆粒が高密度となり、性能が逆転しました。
フリーズグラニュレーションは、内部構造が均質な低密度顆粒(顆粒自体の充填量が少ない)が得られるため、成形体密度は向上しにくいと考えられます。しかし成形体自体も均質なため、焼成時に欠陥が生じにくく密度が向上したと考えられます。
事例2 バイオ
ヨーグルトをモデル検体として、スプレードライ顆粒、フリーズグラニュレーション顆粒を調製し、比較しました。
顆粒外観
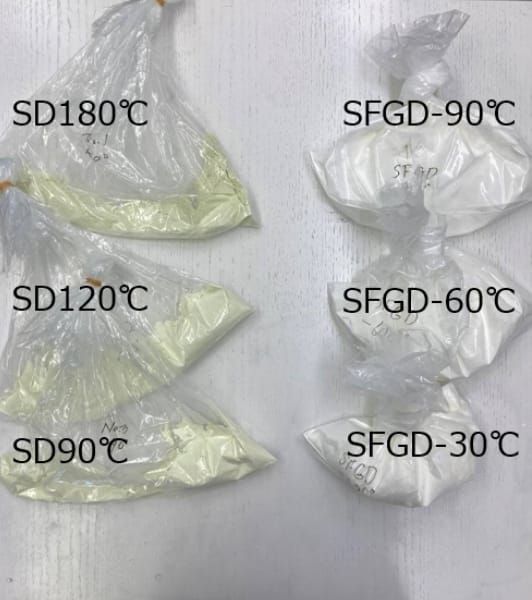
スプレードライ顆粒は全体的に黄色くなり、フリーズグラニュレーション顆粒は白色となりました。スプレードライ顆粒は高温条件ほど黄色味を帯びているので、熱の影響と考えられます。
SEM画像
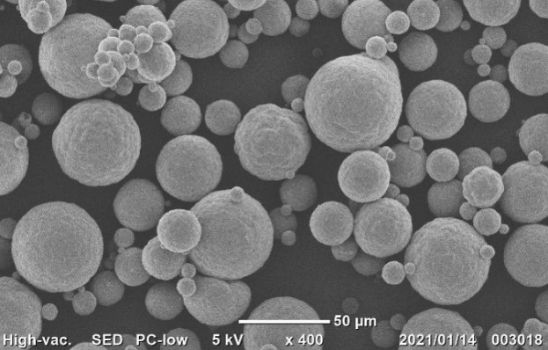
スプレードライ顆粒
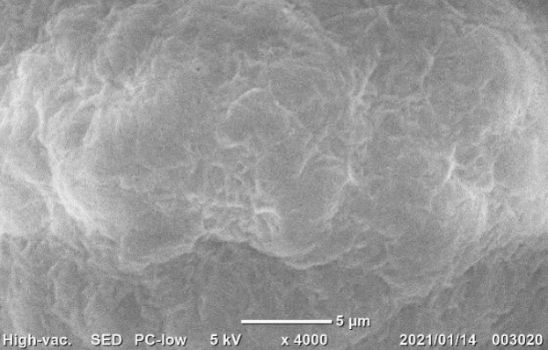
スプレードライ顆粒拡大
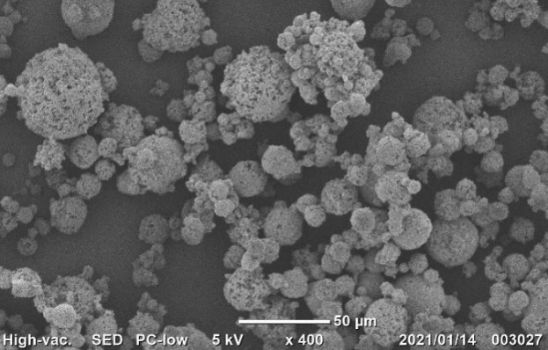
フリーズグラニュレーション顆粒
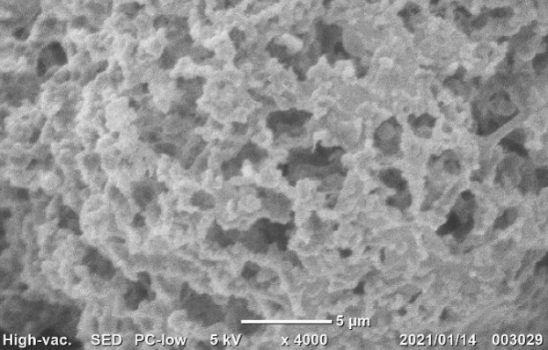
フリーズグラニュレーション顆粒拡大
スプレードライ顆粒は表面に隙間が無く、密に詰まっている様子が確認できますが、フリーズグラニュレーション顆粒は空孔を多く有しており、多孔質な顆粒構造となっています。溶解性も大きく変わることが想定できます。
生菌数
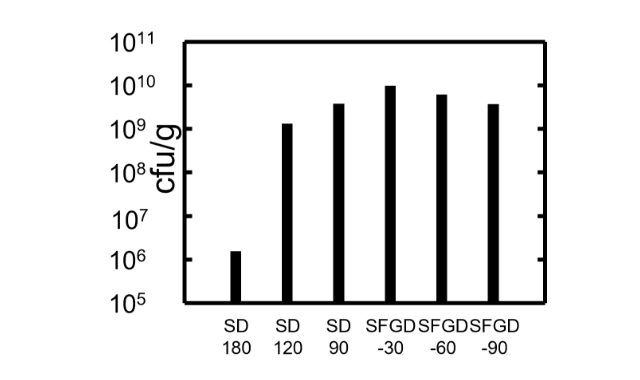
MRS寒天平板嫌気培養法にて評価しました。フリーズグラニュレーション顆粒の-30℃条件が最も生菌数が高くなりました。乳酸菌においては、高温条件は好ましくないことは勿論、低すぎる温度に曝されることも、生菌数を減らしてしまうことが示されました。
事例3 医薬
錠剤の賦形剤等で広く使用されている乳糖をモデルとして、スプレードライ顆粒、フリーズグラニュレーション顆粒を調製し、評価しました。
粒度分布
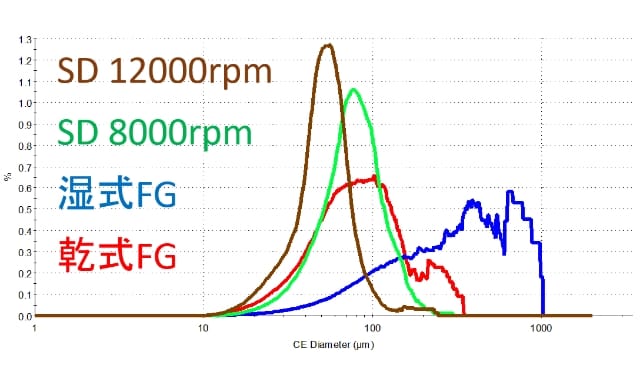
スプレードライ顆粒は粒度分布がシャープで小さく、フリーズグラニュレーション顆粒は粒度分布がブロードで特に湿式冷却方式で調製した顆粒が大きいことが示されました。スプレードライがシャープな粒度分布であるのは、ロータリーアトマイザー方式で噴霧しており、フリーズグラニュレーションは二流体ノズルで噴霧していることが主要因です。またフリーズグラニュレーションは乾燥時に収縮が無いので、スプレードライと比較して粒子が大きくなる傾向です。フリーズグラニュレーションの乾式冷却と比較して湿式冷却の顆粒が大きい理由は、凍結固化速度の違いです。双方とも二流体ノズル方式で噴霧していますが、湿式冷却方式は吐出口近傍直下に液化窒素の液面が存在しているため、噴霧直後の大きい液滴が液化窒素に含侵して凍結固化されます。乾式冷却方式は冷却ガスの気流中に噴霧されるため、液化窒素と比較すると凍結固化速度が遅く、噴霧直後の大きい液滴が分裂して微細液滴となってから固化していると推察されます。
SEM画像
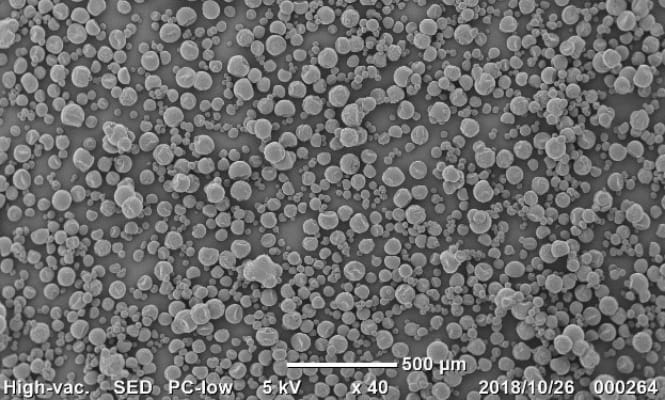
スプレードライ顆粒
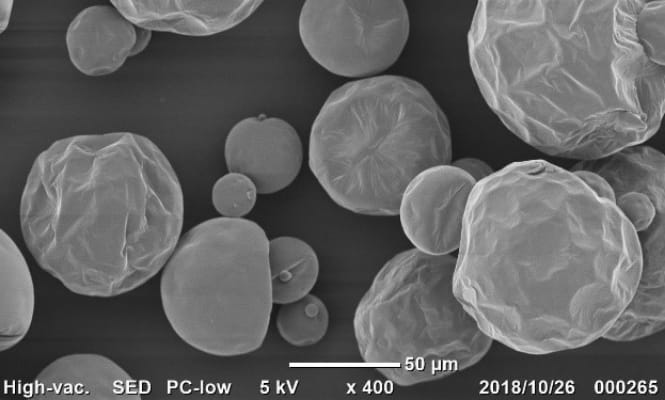
スプレードライ顆粒拡大
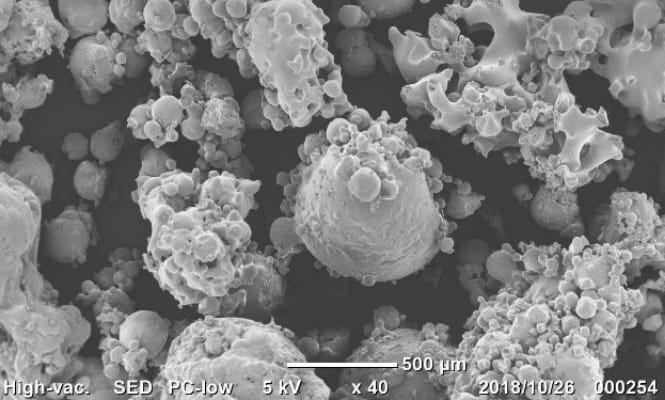
フリーズグラニュレーション顆粒
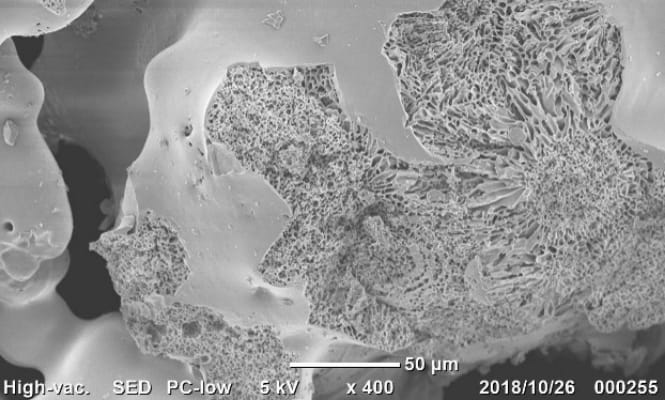
フリーズグラニュレーション顆粒拡大
粒度分布の結果通り、SEMでもスプレードライ顆粒は粒度分布がシャープで小さく、フリーズグラニュレーション顆粒はブロードで大きいことが確認できます。形状はスプレードライ顆粒は球形で表面が膜のような構造をしていることに対し、フリーズグラニュレーション顆粒は歪な形状で表面の一部は膜状となっているが、大部分は多孔質な構造となっていることが確認できます。
結晶構造
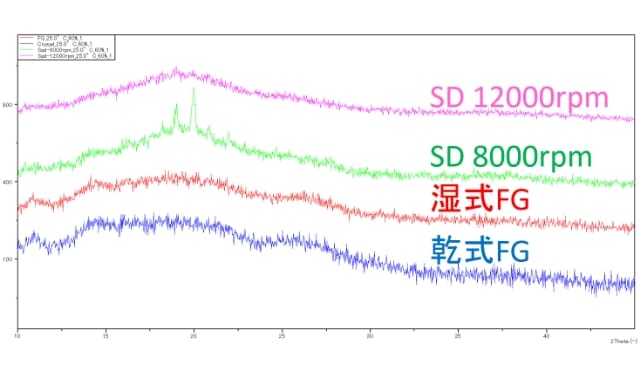
X線回折装置(XRD)にて、結晶構造を測定した結果、SD8000rpmが一部結晶構造を保持しており、その他検体は、非晶質(アモルファス)であることが確認できました。SD8000rpmはロータリーアトマイザーの回転数が低く粒度分布結果からも大きい粒子となっていたので乾燥に時間を要したことが一部結晶構造を有したと考えられます。フリーズグラニュレーション顆粒においては、SD8000rpmよりはるかに大きい粒子となっていましたが、完全に非晶質な状態であることが確認できたので、フリーズグラニュレーションの優位性が示されたかと思います。
事例4 セルロースナノファイバー(CNF)の粉体化
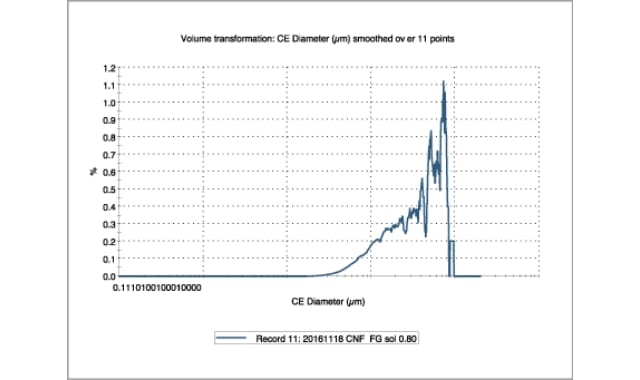
セルロースナノファイバー(CNF)は、パルプをナノサイズまで微解砕した新素材で、植物由来のため環境に優しく、且つ鉄の5倍の強度、鉄の1/5の重量、低熱膨張等、様々な特性を持つので、これから多種多様な用途への展開が期待されています。
通常、CNFは低濃度の水で分散した液で提供されており、乾燥することで輸送コストの低減、経年劣化防止が考えられますが、乾燥させるとナノ繊維が強固に凝集してしまい、比表面積が著しく低下、溶媒への再分散が困難で、その特性が低下してしまうことがあります。しかし、フリーズグラニュレーションで乾燥粉体化すると、瞬間凍結により形状を保持し、時間を要する昇華現象の凍結乾燥により固形物の移動が無いので、写真のようにナノ繊維を保持した造粒粉体を得ることができます。写真の造粒粉体はCNF分散液2wt%のため、通常の乾燥では大きく収縮・凝集する所を、D50:400μmの大粒子で捕集できています。
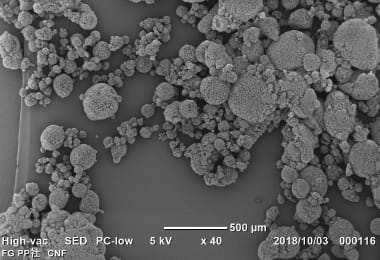
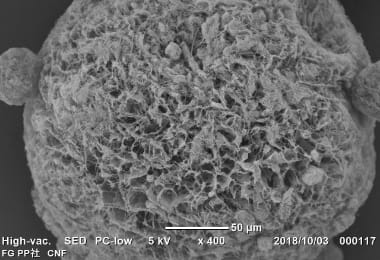
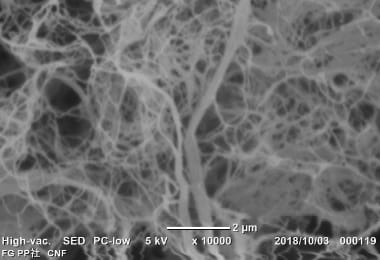
フリーズグラニュレーションご依頼の流れ
お問い合わせ
メール、お電話にてご連絡・お問い合わせ下さい。(ユーザー様)
ヒヤリング
当社専門スタッフが、ご要望をヒヤリングします。またユーザー様にテスト・受託加工確認書をご記載頂きます。(当社・ユーザー様)
ご提案・御見積書を提出
ユーザー様のご要望に適したフリーズグラニュレーター、フリーズドライヤーでの受託加工をご提案・御見積書を提出します。(当社)
注文書を発行
御見積金額、テスト内容に問題が無ければ、加工実施日程をお打ち合わせの上、注文書を発行頂きます。(当社・ユーザー様)
サンプルやご支給品を当社に送付
実施日前日までにサンプルやご支給品を当社に送付下さい。当日にハンドキャリーでも可(ユーザー様)
実施日当日・加工開始
フリーズグラニュレーションのよくあるご質問
フリーズグラニュレーションで得られる最小の粒子径、最大の粒子径を教えて下さい。
原液の物性によって大きくことなるので、一概に申し上げることはできません。一般的に原液固形分濃度が低く、低粘度であれば粒子は小さくなり、逆に原液固形分濃度が高く、高粘度であると粒子が大きくなります。スプレードライと比較すると、液滴→乾燥粒子の過程で収縮がないので、大きくなります。当社保有設備での実績では、最小でD50:10μm、最大で700μm程度です。乾式冷却で数十~200μm、湿式冷却で100~400μm程度となることが多いです。
有機溶剤系の処理は可能でしょうか。
使用可能な種類は限られますが可能です。一般的な有機溶剤は凝固点が低いので、凍結させることが困難且つ、凍結は可能であっても次工程の凍結乾燥中に溶解してしまい、粉体になりません。弊社実績ではシクロヘキサン、tert-アミルアルコールでの粉体化実績があります(※現在、tert-アミルアルコールの引き受けを停止しています)。実績のない有機溶剤でも安全性が確保できれば実施可能なため、詳細はお問い合わせ下さい。
テストに必要な最小量、受託加工の最大量を教えて下さい。
最小量は50mL、最大量は凍結後の嵩によって異なりますが、数十L程度になります。
依頼してから、加工の実施までどの程度の期間となりますか。
ご要望に適した装置のスケジュールに依存するため、明確に申し上げることはできませんが、装置が空いている状況であれば数日、空きがない状況では1~2ヶ月後となるイメージです。
秘密保持契約等の締結は可能ですか。
可能です。締結前であっても、ユーザー様情報を他社様にお話することはありません。
品質保証に対応はしていますか。
対応していません。ご支給頂く原液サンプルの物性変化や季節、天候等、様々な要因で粉体物性は変化します。粉体測定、液体測定サービスにて、粉体・液物性の評価は実施しています。
フリーズグラニュレーション受託加工に立ち会うことは可能でしょうか。
可能です。初回のトライの際は、是非お立会い頂きたいと思います。ユーザー様が求めている最適な粉体について、議論しながら加工を実施できれば、より良い粉体が製造できると考えています。凍結造粒処理し、フリーズドライヤーに投入するまでをお立会い頂くことが多いです。フリーズドライヤーには長時間が必要なため、改めてお立会い頂き、フリーズドライヤーから乾燥粉体の取り出し作業をお立会い頂くか、弊社のみで取り出して、乾燥粉体を郵送させて頂くことになります。