目次
スプレードライ(噴霧乾燥)
スプレードライとは、液体材料を高温気流中に噴霧し、急速に乾燥させることによって乾燥粉体を製造する連続式プロセスです。ロータリーアトマイザーやスプレーノズル等の噴霧システムによって、高温気流が連続で流れる乾燥プロセス内に、溶液やゲル、懸濁液、スラリー、エマルション等の液体材料を噴霧します。噴霧によって微粒化した液滴は、比表面積が増大し、秒単位で水分が蒸発して乾燥します。プロセスに供給される高温気流の熱は、液滴表面の水分蒸発に伴う蒸発潜熱として即座に消費されるため、例えば食品などの熱に敏感な材料にも使用することが可能です。また、液体材料から直接かつ連続で粉体を得られるため、濃縮、濾過、粉砕、混合、分級、乾燥、造粒という多段工程を一つにまとめることが可能です。
乾燥した造粒粉体は、球形で流動性に優れ、シャープで安定した粒度分布になります。プロセスに使用する乾燥空気は、主に大気を使用します。液体材料に可燃性の有機溶媒が含まれる場合や、酸化あるいはCO2との反応を避けたい、また粉じん爆発や発火の可能性が高い場合は、窒素等の不活性ガスを循環させて使用します。
スプレードライ法の特徴
- 液体から直接粉体が得られるため、製造工程を簡略化できる
- 液滴を秒単位で乾燥するため、熱に弱い材料も処理することが可能
- 造粒体は球形で流動性に優れ、シャープな粒度分布が得られる
- 噴霧システムの選定により、精密な粒子制御を行うことが可能
- 連続式プロセスであるため、スケールアップが容易で大量生産に適する
スプレードライ法の歴史
スプレードライ法は、1800年代後半に発明されました。1865年に、Charles LaMontが強力な空気の噴出によって卵を薄い液滴にし、加熱した空気の流れに落下させて乾燥させる方法の特許を取得しました。1872年には、化学者で医師のSamuel R. Percyが粉乳を製造するためのスプレードライヤープロセスの特許を取得しました。その後、1920年代から第二次世界大戦にかけて、主に粉乳の生産で実用化が進み、また徐々に他のアプリケーションへ利用が広がっていきました。日本では、戦前に醤油などの調味料および粉乳の製造法として活用が始まったといわれています。1950年代以降は、乾燥理論および製造プロセス面における研究が盛んに行われ、日本を含む先進工業国を中心に、金属、セラミックス、合成樹脂、化学品等の工業用素材向けにも活用が広がりました。ファインセラミックスや金属、またそれらを用いた高機能複合素材は、幅広い産業用途で利用されています。これらの工業素材分野では、食品や医薬品とは異なる要素において噴霧乾燥技術の向上が求められました。その結果、スプレードライ法は、粒子の形状や粒度、結晶構造、密度等を精密に制御することが可能なプロセスとして、技術面においてさらなる進歩を遂げました。現在では、食品や医薬品といった伝統産業に加えて、エレクトロニクスや半導体、光学材料、磁性材料、触媒等の様々な技術を支える土台であり、素材産業にとって不可欠な粉体製造法となっています。
アプリケーション例
食品
ミルク、クリーマー、ホエイ、乳酸菌、ビフィズス菌、ラクトフェリン、コーヒー、茶、緑茶カテキン、アルギン酸、コラーゲン、ケラチン、キトサン、グルコサミン、コンドロイチン、アガリクス、プロポリス、酵母、アスコルビン酸、ビタミン、クエン酸、フラボノイド、イソフラボノイド、フマル酸、リンゴ酸、コハク酸、酒石酸(タルタル酸)、フィチン酸、ステビア、イヌリン、トンカットアリ、モリンガ、マカ、アルニカ、ウコン、オウレン、ゲンチアナ、トウキ、サラシア、EPA・DHA等の食品マイクロカプセル、油脂エマルションマイクロカプセル、親水性粉末油脂、ココナッツオイル、澱粉、デキストリン、トレハロース、D-マンニトール、果糖、ブドウ糖、オリゴ糖、食品香料、香辛料、調味料(水産品、畜産品、農産品等)、粉末酒、天然色素、合成着色料、増粘剤、バイオガム、ローカストビーンガム、キサンタンガム、酸化防止剤、保存料、品質改良剤、植物抽出品、ミネラル、藻類、青汁、果汁、卵白、水産加工品、植物蛋白、動物蛋白、酵素、動物飼料、餌料
医薬品
医薬品、バイオ医薬品、原薬(APIs)、難溶性医薬品マイクロカプセル、コロイドキャリア(リポソーム、高分子マイクロスフィア、高分子ナノ粒子、マイクロエマルション)、抗生物質、固体分散体製剤、非晶質製剤、賦形剤、ポリエチレングリコール(PEG)、ポリ乳酸(PLA)、ポリカプロラクトン(PCL)、乳酸-グリコール酸共重合体(PLGA)、ペクチン、水溶性ポリマー、カルボキシビニルポリマー、第4級アンモニウム化合物、酵素、酵母、漢方薬、褐藻エキス、サプリメント
化学品
シリカ、珪酸ソーダ、炭酸カルシウム、触媒、ポリマー、ポリビニルアルコール(PVA)、ポリエチレンイミン(PEI)、ポリビニルピロリドン(PVP)、顔料、染料、石鹸、洗剤、界面活性剤、ゼオライト、化粧品、リグニン、硫安、燐案、尿素、肥料、除草剤、農薬、殺虫剤、重炭安、塗料、メラミン樹脂、アクリル樹脂、フェノール樹脂、エポキシ樹脂、尿素樹脂、アミノプラスチック、樹脂エマルジョン、機能性プラスチック、バイオプラスチック、生分解性プラスチック、エラストマー、ラテックス、塩化ビニル、酢酸ビニル、電池材料、酸化チタン、リン酸化合物、リン酸カルシウム、天然アパタイト、メチルセルロース(MC)、ヒドロキシプロピルメチルセルロース(HPMC)
セラミックス・合金・粉末冶金
アルミナ(Al2O3)、ジルコニア(ZrO2)、シリカ(SiO2)、窒化ケイ素(Si3N4)、サイアロン(SiAlON)、炭化ケイ素(SiC)、窒化アルミ(AlN)、窒化ホウ素(BN)、酸化チタン(TiO2)、酸化マグネシウム(MgO)、チタン酸バリウム(BaTiO3)、ステアタイト(MgO・SiO2)、ムライト(3Al2O3・2SiO2)、フェライト(Fe2O3)、ジルコン(ZrSiO4)、イットリア(Y2O3)、セリア(CeO2)、サーメット(TiC, TiN)、タングステンカーバイド(WC)、ニッケル合金、アルミニウム合金、マグネシウム合金、チタン合金、コバルト合金、レアメタル、レアアース、バイオセラミックス
工業材料・部品
電子材料、積層セラミックコンデンサ(MLCC)、半導体、絶縁体、磁性体、誘電体、ガラス材、センサー、触媒、耐火材、パルプ材、歯科材料、ハイドロキシアパタイト、セルロース、セルロースナノファイバー(CNF)、合成ゴム、合成繊維、カーボン、グラフェン、カーボンナノチューブ(CNT)、超電導材料、トナー原料、研磨剤、超硬工具、光ファイバー、電池材料、リチウムイオン二次電池正極材、ナトリウムイオン電池材料、全固体電池材料
ラクトース
酵母
クエン酸
ゼオライト
アルミナ
シリカ
ジルコニア
WC(- Fe-Ni)合金
コバルト
モリブデン
酸化イットリウム
酸化インジウム
プロセス概要
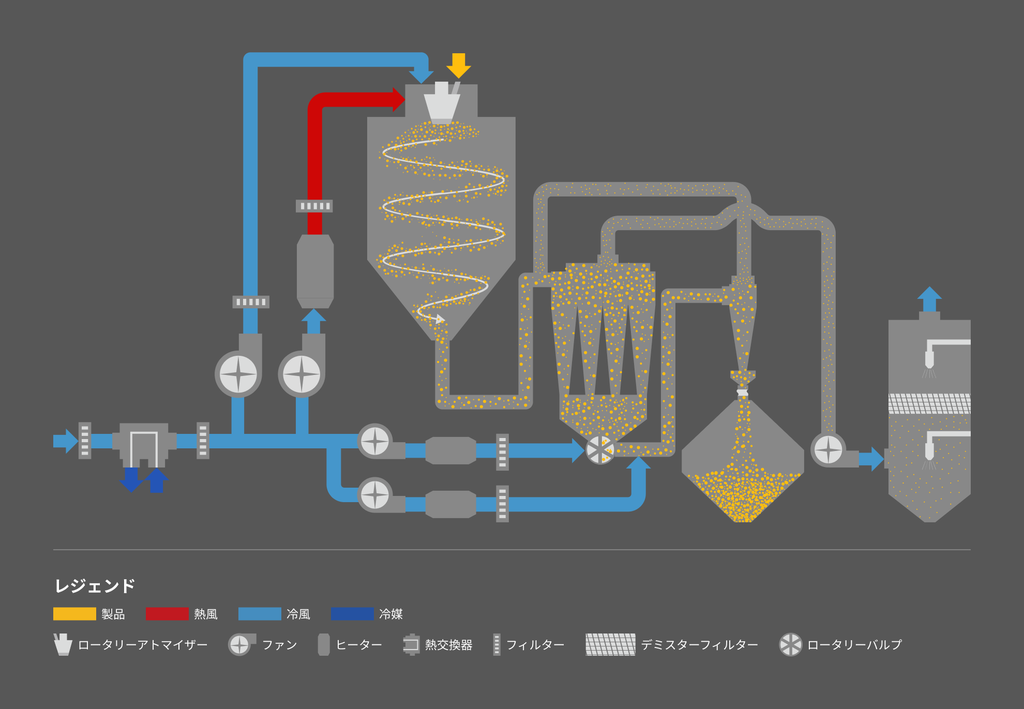
噴霧乾燥プロセスは、液体の微粒化、液滴の水分蒸発、乾燥粉体の分離回収という3つの工程からなります。
液体の微粒化
溶液やゲル、懸濁液、スラリー、エマルション等の液体材料を、ロータリーアトマイザーやスプレーノズル等の噴霧システムによって、高温気流が連続で流れる乾燥プロセス内に噴霧します。液体は、噴霧システムによって微粒化し、微細な液滴となります。液滴は、微細化することによって急激に比表面積が増大するため、数秒から数十秒程度の短時間で水分が蒸発して乾燥します。乾燥粉体の粒度や形状は、噴霧時の液滴に強く影響を受けるため、液体の微粒化はスプレードライ法における最も重要な要素技術になります。そのため、目的とする造粒体品質を得ることが可能な噴霧システムおよび微粒化条件を決定することが、スプレードライヤーの導入検討における最初のステップとなります(液体噴霧方式の選定はこちら)。
噴霧システムに供給された液体は、エネルギーが内外から付加されることによって不安定化し、流動と変形が生じて分裂します。液体は、流速の増加に伴う液中の乱れによって不安定性が増します。さらに、外気等の外部作用も加わることにより分裂を引き起こし、液糸や液滴が形成されます。外部作用は、主としてせん断力や、液体と外気の境界面に働く力(表面張力および気流による負圧)があります。液流の大部分が微粒化した状態を噴霧流といいます。液滴は、飛散時に再分裂を繰り返すことで微細化し、噴霧流を形成します。理論上は、外気の不規則な乱れによる力と液滴の表面張力が平衡して安定化するまで再分裂を繰り返します。
液体の微粒化は、液体と気体の物性および外部から付加するエネルギーが主要な因子となります。
液体と気体の物性
密度( ρ )、粘性( μ )、表面張力( σ )、比熱( c )、熱伝導率( λ )、温度拡散率( α )等
外部から付加するエネルギー
液流速( ν )、噴射圧力( p )、噴射速度( ν )、回転数( N )、温度( T )等
外部から付加するエネルギーは、液体を不安定にする働きである一方、液体は変形に抵抗して元の安定状態に戻ろうと働きます。噴霧流における液体の安定性は、液体の慣性力、粘性力および表面張力の無次元数から導かれます。代表的な無次元数としては、レイノルズ数( Re )、ウェーバー数( We )、ジェット数( Je )、レイノルズ数とウェーバー数から導かれるスタビリティ数( St )、オーネゾルゲ数( Oh )等があります。
噴霧特性は、噴霧システムだけではなく、液体材料の物性やスプレードライヤーのプロセス条件からも影響を受けます。液体の物性面では、密度や粘性、pH、分散状態、また懸濁液の場合は一次粒子の物性が影響します。プロセス条件面では、スプレードライヤープロセスの形状や温度、風量、内圧等が影響します。そのため、液体材料および製造プロセスの特性を考慮し、目的とする造粒体品質が得られる噴霧システムおよび微粒化条件を決定することが重要です。
液滴の水分蒸発
噴霧により微粒化した液滴の水分は、スプレードライヤープロセス内に連続して供給されている熱風と接触することにより、気流中に浮遊した状態で蒸発します。液滴の乾燥速度は、一般に数秒から数十秒程度となります。熱風との接触による液滴群の伝熱係数は、噴霧直後の加速時には、終端速度に達した後の自由落下区間と比べて非常に大きくなります。自由落下区間における伝熱係数は、単位空間あたりの液滴群の濃度が薄まることによって、ヌセルト数( Nu )、プラントル数( Pr )およびレイノルズ数( Re )から導かれるランツ・マーシャルの式等により推算することが可能です。しかし、落下時における液滴群の凝集や干渉、液体材料の物性およびプロセス運転条件により、実際の挙動にはばらつきが生じます。
乾燥速度と乾燥特性は、湿り材料である液体の物性および乾燥条件によっても異なります。湿り材料が非吸着性の多孔体の場合は、液滴は高温気流が連続で接触することによって受熱し、材料予熱期間と呼ばれる液滴の温度上昇を経て、表面蒸発期間に移行します。表面蒸発期間では、液滴表面の水分蒸発によって蒸発潜熱が奪われます。その結果、液滴温度は動的平衡温度である湿球温度( Tw )に漸近します。この期間では、液滴への入熱量はすべて液滴表面における自由水の蒸発に使われるため、液滴の表面温度と乾燥速度はほぼ一定になります。表面蒸発期間における乾燥速度は、液滴表面と熱風気流の水蒸気分圧の圧力差( ΔP )に、気体側の物質移動係数を乗じた値となります。非吸着性の多孔体の場合は、液滴表面の水蒸気分圧は飽和水蒸気圧に等しく、表面における自由水が減少しても、気体側の物質移動係数は大きく低下しません。そのため、材料表面の温度が上昇しない場合は、乾燥速度はほぼ一定となるため、定率乾燥期間に相当します。その後、液滴径は水分蒸発の進行に伴い縮小し、液滴内部から表面への自由水の移動が蒸発速度に劣後することによって、減率乾燥期間に移行します。減率乾燥期間では、固形分である材料温度が表面から徐々に上昇し始めます。受熱量の一部が材料の温度上昇に費やされるため、水分蒸発に使われる熱量がその相当分減少し、乾燥速度が低下します。定率乾燥期間と減率乾燥期間の遷移点における含水率を限界含水率( Wc )といいます。
個別の液体材料における実際の乾燥過程は、湿り材料の内部で起こる熱と物質の移動抵抗によって異なります。限界含水率に到達する前は自由水が豊富に存在するため、湿り材料の物質移動抵抗は小さくなります。その後、乾燥が進行して含水率が低下するとともに、湿り材料の物質移動抵抗は増加します。
不均質系材料である懸濁液やスラリーの場合は、一般に含水率が30〜50%程度までは定率乾燥期間となり、乾燥速度が境膜律速下において一定値となる傾向があります。溶液やゲル等の均質系材料の場合は、定率乾燥期間が短い、あるいは無い場合もあります。例えば、高分子溶液の場合は、水分が液滴内で拡散移動することにより、定率乾燥期間が認められないことがあります。この場合は、定率乾燥期間が存在しないため、乾燥速度は遅くなります。一方、塩類溶液の場合は、液滴の表面に結晶が析出して外殻を形成するため、外殻形成時点から減率乾燥期間に移行する傾向もみられます。外殻が形成される材料は、熱風温度が沸点以上の場合に、液滴内部の蒸気圧が外気圧よりも高くなることによって外殻が破裂することがあります。外殻が破裂する例としては、結合剤を添加したスラリーや、賦形剤あるいはコーティング剤を添加してマイクロカプセル化を行う噴霧乾燥工程があります。ゼラチンのような水との親和力が高いゲルや結合水の場合は、乾燥初期に液滴表面に皮膜を形成し、その時点より減率乾燥期間に移行することがあります。皮膜を形成する結合水のような高分子材料は、液滴が膨張することによって液滴径が大きくなることもあります。
水分蒸発は、表面蒸発期間を経て、内部で蒸発して蒸気の状態で表面に移動する、内部蒸発期間へ移行する場合もあります。内部蒸発期間は、減率乾燥期間で発生します。内部蒸発における実際の熱と物質の挙動については、未だ解明されていない所が多くあります。蒸発面が後退する理論では、蒸発が内部の深さ方向のある点において起こると仮定します。液滴を乾燥領域と湿潤領域に分けて、その界面において蒸発が起こると仮定し、界面は乾燥の進行とともに内部へ後退します。また、蒸発が起こる場所が界面ではなく領域で捉える内部蒸発圏理論もあります。噴霧乾燥における実際の挙動としては、乾燥の進行時に、外殻または皮膜が形成された状態で内部蒸発期間へ移行した場合は、内部で蒸発した水が表面層から外部に抜け出せず、水蒸気圧によって表面皮膜が膨張する、造粒体が破裂する、あるいは中空球状となる場合があります。その場合、乾燥した造粒体の外殻密度は高くなり、内部は低密度になる傾向があります。懸濁液の場合は、液滴に含まれる粒子成分が複数あり、それぞれの粒径が異なる場合は、乾燥時の粒子移動によって造粒体の内部で偏析が生じることがあります。
乾燥粉体の品質は、粒子の内部構造に影響を受けます。造粒体の粒度や形状、密度および内部構造を把握し、液体物性および乾燥条件の適切な調整を行うことが重要です。
乾燥粉体の分離回収
粉体は、乾燥チャンバー内で旋回気流に乗った状態で落下します。液滴は、チャンバーの内壁に接触する前に水分が蒸発して乾燥します。適切に設計されたスプレードライヤーは、製品が乾燥に要する落下距離に応じた有効容積が確保されているため、未乾燥の製品が内壁に付着するのは最小限に収まります。乾燥粉体の分離回収は、粉体を製品として捕集する製品回収機構および製品回収後にプロセスガスに残存する微粒子が系外に排出することを防止する最終除塵システムがあります。
製品回収機構は、乾燥チャンバーの下部に落下した粉体を直接回収する方法や、サイクロンによる回収があります。食品や医薬品などの比較的に軽めの粉体や、分級する必要のない製品については、一般にサイクロンで一括捕集します。サイクロンで捕集する場合は、スプレードライヤーの生産規模や運転条件に応じて、シングルサイクロンやマルチサイクロン等を採用します。ファインセラミックスや無機材料などの分野では、スプレードライヤープロセス内で直接分級を行う目的として、乾燥チャンバー下部およびサイクロンの二点で回収する方式があります。乾燥チャンバー下部では、球形に造粒された流動性の良い造粒粉が得られ、サイクロンにより微粒子を捕集します。サイクロン方式で良好な回収効率が得られない場合は、バグフィルターで一括捕集します。バグフィルターによる一括捕集は、造粒体がシングルミクロンレベルの微粒子である場合や、サイクロンの遠心力により造粒体が破損してしまう場合に採用されます。製品の吸湿性や温度管理、酸化対策などを考慮し、除湿システムや温度制御を組み合わせた粉体輸送(空気輸送や各種フィーダ等)を行った後に製品を回収するプロセスもあります。また、粉体輸送時に流動層を組み込むことにより、追加の造粒を行うこともあります。その他、篩や金属探知等のインライン検査を組み込む場合もあります。
最終除塵システムは、バグフィルターや湿式スクラバーがあります。除塵システムで回収される粉体は、品質上において製品と見なされない、あるいは廃棄物となるために損失として扱われる場合があります。バグフィルターによる除塵は、単一品種を扱う場合は捕集した粉体を再利用する場合があります。多品種を扱う場合は、クロスコンタミネーションを防止するための洗浄工程が必要になります。バグフィルターの洗浄にかかる設備とオペレーション費用は高額になるため、一部の高付加価値品を除き一般には採用されません。食品などにおいてサニタリー性が要求される場合は、湿式スクラバーや湿式電気集塵機(WESP)を採用します。これらは湿式プロセスであるため、排水処理設備が必要になります。回収した液体は、濃縮して再利用する、あるいは再び噴霧乾燥を行う場合があります。これらのケースは、付帯設備が高額になる、また複数回の乾燥処理により品質が劣化することから、実際の採用は一部の特殊な用途に限られます。環境面において厳しい排出制限ある製品や、排ガス中にバグフィルターでは捕集しきれない微粒子が残存する場合は、電気集塵機(ESP)を採用することもあります。
スプレードライヤーの生産性を高めるためには、適切な分離回収システムを選定し、捕集効率を最大化することが重要です。また、最終除塵システムについては、環境面や衛生面だけではなく、投資費用および運用コストも考慮して選定する必要があります。
プロセスフロー
以下は、オープン型およびクローズド型スプレードライヤーの汎用プロセスフロー例です。
オープンサイクルシステム
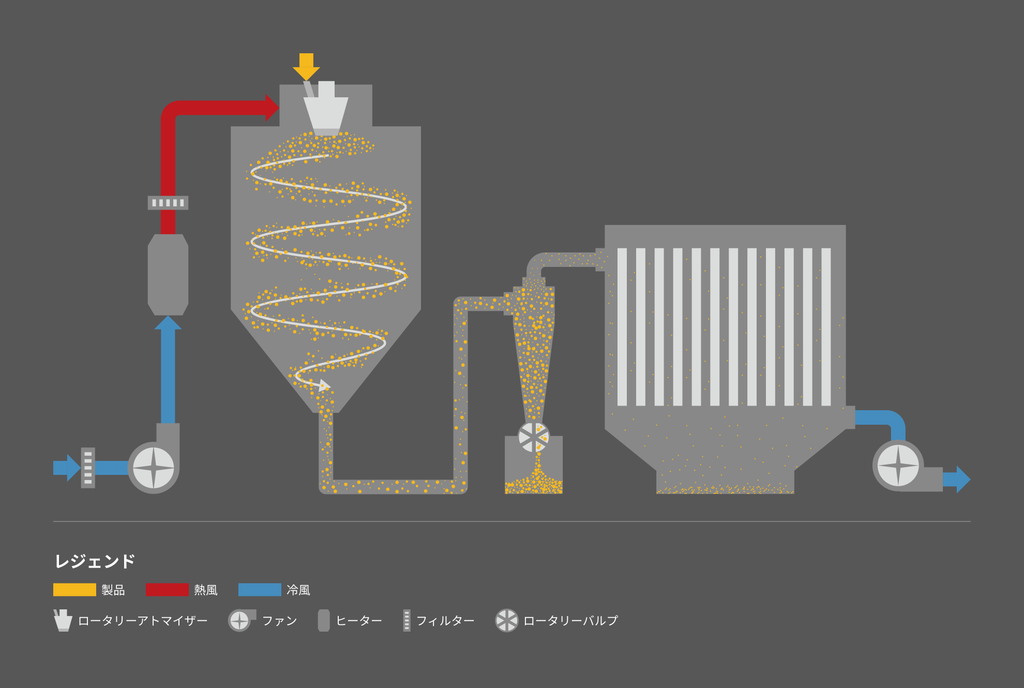
クローズドサイクルシステム
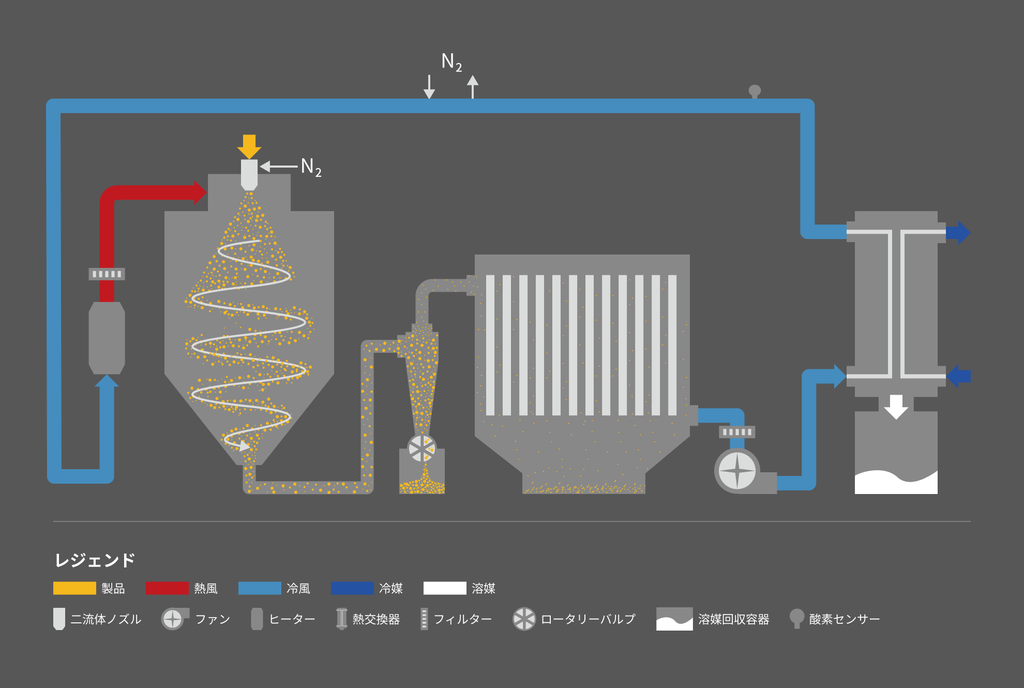
水系溶媒の場合は、一般に大気を使用するオープンサイクルシステムを選定します。液体材料に可燃性の有機溶媒が含まれる場合や、酸化あるいはCO2との反応を避けたい、また粉じん爆発や発火リスクがある場合は、窒素等の不活性ガスを循環使用するクローズドサイクルシステムを採用します。当社は、オープンサイクルシステムとクローズドサイクルシステムの両用型であるデュアルサイクルシステムも設計することが可能です。また、可燃性有機溶媒に対応したオープンサイクルシステムもあります。安全対策として、運転時の溶媒ガス濃度を爆発下限界の25%以下にコントロールし、蒸発した溶媒は触媒あるいは加熱分解プロセスを経て系外に排出されます。
噴霧乾燥プロセスは、一般に以下の要素で構成されています。
液体供給システム
水などの溶媒供給ラインと液体材料の供給ラインを組み合わせたシステムです。溶媒タンクおよび原料タンクから、ポンプによって液体を乾燥チャンバーに設置された噴霧システムに送液します。通常は、原料液の供給(実際の製造工程)前後で溶媒供給を行います。前段で行う溶媒運転は、プロセスの運転条件(プロセス温度や内圧等)を事前に安定させる目的で行われます。後段では、原料液をすべて供給し、供給ライン内に残らないようにする目的があります。原料液は、乾燥効率を上げるために予熱して供給する場合もあります。液体供給システムは、通常はすべて自動化された制御のもとで行われます。
乾燥ガス供給システム
乾燥ガスは、プロセスの入口側と出口側に組み込んだ2つのメインファンを使用して供給します。プレフィルター、高性能フィルター、HEPAフィルター等のフィルタリングシステムを組み込み、コンタミネーションを排除した清浄なガスを、後述の熱源供給システムで加熱して供給します。入口側と出口側ファンの風量を調節することによって、造粒体の物性に適したプロセス内圧制御を行います。供給するプロセスガス量は、物質収支および熱収支に基づき最適に計算されています。計算式には、プロセスの設置場所の温度や湿度(季節変動要因を含む)等の周囲条件も考慮され、必要に応じて除湿や予熱システムが付加されます。乾燥ガスは、一般には大気を使用しますが、液体材料に可燃性の有機溶媒が含まれる場合や、酸化あるいはCO2との反応を避けたい、また粉じん爆発や発火リスクがある場合は、窒素ガス等の不活性ガスを使用する場合があります。
熱源供給システム
ヒーターとしての役割を担う熱源供給は、製造現場が保有するユーティリティの中から、製造コストや安定性、効率性を考慮した上で、最適なシステムを採用します。通常は、電気、蒸気、LNG、LPG、灯油、重油および工場内の排熱等を組み合わせて選定します。例えば、蒸気による間接加熱を主として使用し、制御の反応性を高める目的で電気ヒーターを次段に設置することがあります。熱源の供給方式については、許容される清浄度に応じて直接加熱方式あるいは間接加熱方式を選定します。間接加熱の場合は、熱交換器の放熱出口ガスの一部を循環させることにより、高効率の省エネシステムを構築することが可能です。また、プロセス出口側の排熱を入口側に循環させて熱交換することにより、エネルギー効率を高めることも可能です。省エネルギーのシステムを採用することにより、オペレーションコストの削減に加えてCO2の削減および環境対策としても効果があります。
液体噴霧システム
液体供給システムから供給された液体を、噴霧システムにより乾燥チャンバー内に噴霧します。液体の噴霧方式は、遠心噴霧方式(ロータリーアトマイザー方式)、一流体ノズル方式(加圧ノズル方式/プレッシャーノズル方式)、二流体ノズル方式、超音波ノズル方式があり、要求される粉体特性に応じて選定します(液体噴霧方式の選定はこちら)。当社の特許技術としては、プロセス内の粒度分布をリアルタイムで測定し、得た値をもとにフィードバック制御を行う粒度分布自動追従型 アトマイザーシステムがあります。この制御では、一般に行われるロータリーアトマイザーの回転数固定制御ではなく、粒度分布Dv 50(μm)が設定値となります。プロセス内の粒度分布を監視しながら、回転数が自動で調節されるため、プロセス内外の温度や湿度、圧力等の環境に変化があった場合においても、粉体の粒度を一定に保つことが可能になります。その他、コアンダ効果(流体が近くの壁面に引き寄せられる効果)を応用したコアンダディスク(特許)があります。通常のディスクと比べて噴霧液滴が下方向に向かうため、液滴の滞空時間が長く、生産効率を高める効果があります。また、当社の最新式二流体ノズルは、四流体ノズルなどの多流体ノズルと同水準の微粒化性能があり、圧縮気体の消費量を大幅に低減した上で、シングルミクロンの微粒化が可能です。
乾燥チャンバー
乾燥チャンバー内に噴霧した液滴の水分は、プロセス内に供給される熱風と接触し、気流中に浮遊した状態で蒸発します。熱風は、乾燥ガス供給システムから乾燥チャンバー上部のエアディスパーサーに供給されます。熱風は、エアディスパーサーにより整流され、液滴を効率良く乾燥するために適正な旋回気流を作り出します。乾燥チャンバーのサイズ、形状および有効容積は、造粒体の品質および要求される諸条件に基づき決定します。具体的には、物質収支および熱収支の計算に加えて、噴霧システムの特性と液滴の物性値から導かれる粒子の滞空時間と距離を算出して決定します。液滴の乾燥速度は、一般に数秒から数十秒程度となります。適切に設計されたスプレードライヤーは、液滴が乾燥するまでに必要な滞空時間と距離に応じた空間が確保されているため、未乾燥の製品が内壁に付着するのは最小限に収まります。粉体の滞留時間が短すぎる場合は、未乾燥原料がプロセス内に付着する原因となります。反対に、滞留時間が長すぎる場合も、高温のプロセス内に製品を必要以上に滞留させることによって品質の劣化を招く要因になることがあります。製品の熱変性が懸念される、あるいは原料に吸湿性または潮解性が高い成分が多く含まれる場合は、乾燥チャンバーにエアスイーパーや多段の除湿エア供給ラインを設置することもあります。
製品分離・回収システム
乾燥チャンバーの下部とサイクロンの二点で製品を回収する場合は、チャンバー下部では球形に造粒された流動性の良い造粒体が得られ、サイクロンでは微粒子が得られます。チャンバー下部の製品回収における当社の独自技術として、旋回流分級ユニット Helix(特許)があります。乾燥チャンバー内に回転羽根機構を組み込み、旋回流を起こすことによって、チャンバー下部の製品回収効率を向上させることが可能なユニットです。当ユニットは、プロセスガスを動力として使用するため、追加の工事が必要なく、簡易な設置のみで稼働することが可能です。サイクロンで一括捕集する場合は、スプレードライヤーの生産規模や運転条件に応じて最適なサイクロンシステムを設計します。当社では、ポルトガルのACS社とのパートナーシップにより、PACyc(サイクロンにおける粒子凝集)モデルを設計最適化シミュレーションに組み込んだ高効率サイクロンを採用することも可能です。ACSの高効率サイクロンは、製品の歩留まり向上に加えて、多くのケースにおいてバグフィルター等の最終除塵システムの設置を省略することが可能です。高効率サイクロンを採用することにより、製品回収率の向上(原料損失の低減)だけではなく、バグフィルターを省略することによる設備投資費用の低減につながります。その他、バグフィルターで製品を一括捕集する方式もあります。また、製品回収ラインに除湿や冷却、異物検査、シフター、流動層造粒等を備えた粉体輸送を組み込むこともあります。最終除塵システムは、バグフィルターユニットや湿式スクラバーなどから、環境適合性や衛生面および設備投資とオペレーション費用を考慮して選定します。
洗浄システム
食品や医薬品などの製造プロセスまたは単一のプロセスで多品種の製造を行う場合は、スプレードライヤーを定期的に洗浄する必要があります。研究用の小型装置は、洗浄性を考慮し、分解が容易でサニタリー性に優れた構造にする必要があります。小規模プロセスでは、予算上の制約によって自動洗浄システムが採用されない場合があります。一方、小ロットで多品種かつ多条件の試験を継続して行う研究機関などは、省力化の観点も考慮して自動洗浄システムを採用する場合もあります。中規模のパイロット設備や量産プラントについては、洗浄システムの導入費用やオペレーションコスト、また要求される品質水準を考慮して、適切な洗浄システムを採用する必要があります。定置洗浄(CIP)システムを導入する場合は、生産プロセスにあらかじめ洗浄設備を組み込んだ形で設計を行います。生産プロセスの仕様と原料特性を考慮し、最適な洗浄システムおよび運転プログラムを決定します。一般的なCIPシステムは、水、酸、アルカリの貯蔵タンク、バッファータンク、送液ポンプ、配管ライン、洗浄ノズルおよび各種センサー類が含まれます。洗浄工程は、一般に温水による粗洗浄から、アルカリ洗浄、酸洗浄、温水すすぎ洗浄、仕上げリンス洗浄、乾燥工程と進行します。洗浄剤や洗浄時間など、運用費用の浪費を防ぐためには、適切に設計された洗浄システムが必要です。CIPを効果的に行うためには、原料汚れの特性に応じた化学的・物理化学的な洗浄方案の策定や、生産設備の構造に適した洗浄機器の選定といった総合的なエンジニアリングが要求されます。原料固有の特性や生産プロセスの構造によっては、部分的にCOPを採用し、全体の自動洗浄と区分けすることによって、全自動のCIPシステムよりも、衛生面および安定性に優れた洗浄工程を構築することが可能な場合もあります(セミCIPシステム)。
テスト・受託加工
当社は、積み重ねた技術をもとに、データに基づく最適なスプレードライヤー製造プロセスを提供しています。また、スプレードライヤーのテスト・受託加工および各種分析・測定業務も承っています。粉体加工のみならず、原料の粉砕や混合、成形、焼成、凍結乾燥など、前後工程も含めたサービスを提供しています。国内二拠点のパウダーテクニカルセンター(神奈川県川崎市)およびASEANパウダーテクニカルセンター(タイ)の計三拠点において、顧客の持つ技術的課題を解決するために日々運営しています。2023年に新設した第二パウダーテクニカルセンター(PTC2)では、国内最大規模の分析・測定装置を取り揃えています(粉体テスト・分析・測定サービス詳細/粉体委託加工サービス詳細)。当サービスをご紹介する特設サイトプリス粉ラボを新たにリリースしました。サービスや施設の詳細および技術資料もご案内していますので、ぜひアクセスしてください。