目次
スプレークーリング(噴霧冷却凝固)
スプレークーリングとは、溶融物質を低温気流中に噴霧し、急速に冷却凝固させることによって造粒体を製造する連続式プロセスです。プロセスの名称は、一般にはスプレークーリングと呼ばれていますが、加熱溶融した液体を冷却固化して造粒を行うことから、噴霧冷却造粒、噴霧冷却固化、スプレーコンジーリング(噴霧凝固)ともいわれます。
スプレークーラーは、スプレードライヤーを応用したプロセスです。ロータリーアトマイザーやスプレーノズル等の噴霧システムによって、低温気流が連続で流れる冷却プロセス内に液体材料を噴霧します。噴霧によって微粒化した液滴は、比表面積が増大し、秒単位で冷却凝固します。冷却凝固した造粒粉体は、球形で流動性に優れ、シャープで安定した粒度分布になります。噴霧乾燥と異なり、蒸発に伴う液滴収縮が生じないため、造粒体は大きくなります。造粒体は、顆粒、造粒体、ビーズ、プリル等とも呼ばれ、一般には数十μm~数mm程度の範囲において造粒を行うことが可能です。溶融物質を膜物質として、原液内に芯物質を混合することにより、容易にマイクロカプセル化を行うことが可能です。噴霧乾燥を含む、他のマイクロカプセル化プロセスと比較した場合、カプセル化効率は高くなります(90〜100%)。プロセスに使用する冷却空気は、主に大気を使用します。液体材料に可燃性の成分が含まれる場合や、酸化あるいはCO2との反応を避けたい、また粉じん爆発や発火の可能性が高い場合は、窒素等の不活性ガスを循環して使用します。噴霧冷却凝固プロセスは、安価かつ単純なプロセスで、流動性が高く球状の造粒体を製造することが可能です。単一工程で連続生産が可能であり、粉砕、分級、顆粒化等の下流工程を必要としない利点があります。また、消費エネルギーもスプレードライヤーと比べて少なくなります。
スプレークーリング法の特徴
- 液体から直接粉体が得られるため、製造工程を簡略化できる
- 造粒体は球形で流動性に優れ、シャープな粒度分布が得られる
- 噴霧システムの選定により、精密な粒子制御を行うことが可能
- 連続式プロセスであり、スケールアップが容易で大量生産に適する
- 高水準のマイクロカプセル化を行うことが可能
アプリケーション例
ろう、ワックス、飽和脂肪酸、ステアリン酸、パルチミン酸、ラウリン酸、ミリスチン酸、脂肪酸アマイド、セバシン酸、リン脂質、パーム油乳化ワックス、ステアロイル乳酸ナトリウム、エッセンシャルオイル、パラフィン、テルペン、ステロイド、カロテノイド、魚油、オメガ 3脂肪酸、オメガ6脂肪酸、グリセリン、モノグリセリド、ジグリセリド、トリグリセリド、ポリオキシルグリセリド、ポロキサマー、ポリエチレングリコール(PEG)、高級アルコール、無水フタル酸、無水マレイン酸、テレフタル酸ジメチル、マイクロカプセル、ポリマー、石油樹脂、フェノール樹脂、塩ビ安定剤、ラテックス、エラストマー、合成ゴム、尿素、無機融液、有機融液
プロセス概要
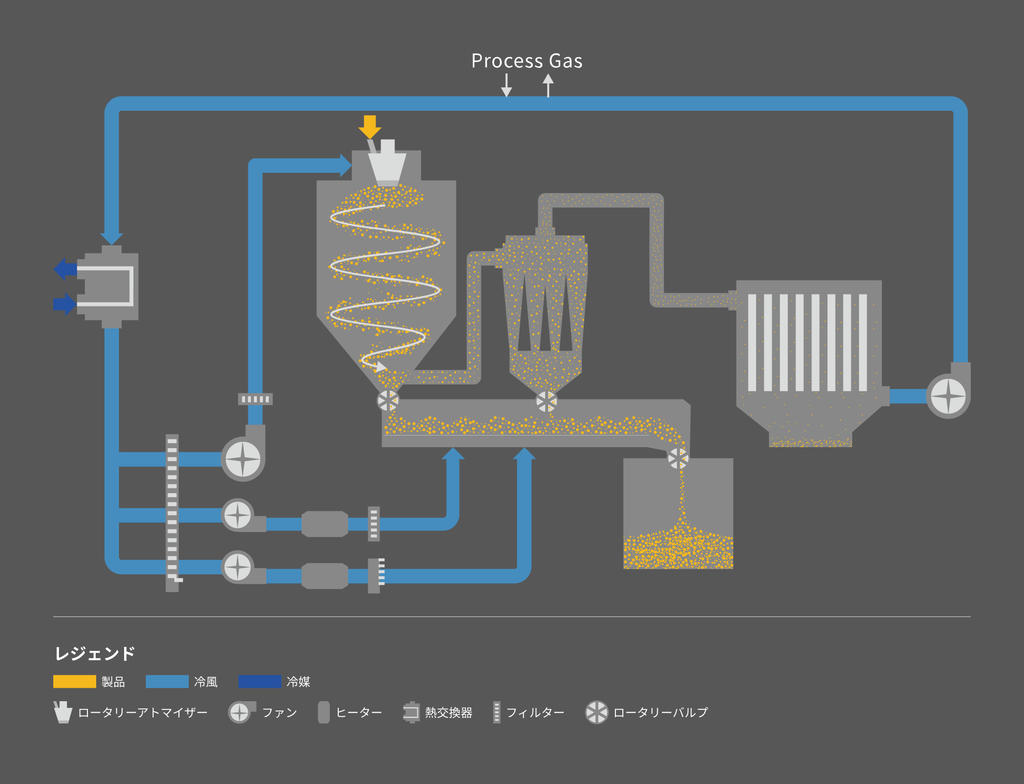
噴霧冷却凝固プロセスは、液体の微粒化、液滴の凝固、造粒体の分離回収という3つの工程からなります。
液体の微粒化
溶融した液体原料を、ロータリーアトマイザーやスプレーノズル等の噴霧システムによって、低温気流が連続で流れる冷却プロセス内に噴霧します。溶融液は、噴霧システムによって微粒化し、微細な液滴となります。液滴は、微細化することによって急激に比表面積が増大するため、数秒から数十秒程度の短時間で冷却凝固します。固化した造粒体の粒度や形状は噴霧時の液滴に強く影響を受けるため、液体の微粒化はスプレークーリング法における最も重要な要素技術になります。そのため、目的とする造粒体品質を得ることが可能な噴霧システムおよび微粒化条件を決定することが、スプレークーラーの導入検討における最初のステップとなります(液体噴霧方式の選定はこちら)。
噴霧システムに供給された液体は、エネルギーが内外から付加されることによって不安定化し、流動と変形が生じて分裂します。液体は、流速の増加に伴う液中の乱れによって不安定性が増します。さらに、外気等の外部作用も加わることにより分裂を引き起こし、液糸や液滴が形成されます。外部作用は、主としてせん断力や、液体と外気の境界面に働く力(表面張力および気流による負圧)があります。液流の大部分が微粒化した状態を噴霧流といいます。液滴は、飛散時に再分裂を繰り返すことで微細化し、噴霧流を形成します。理論上は、外気の不規則な乱れによる力と液滴の表面張力が平衡して安定化するまで再分裂を繰り返します。
液体の微粒化は、液体と気体の物性および外部から付加するエネルギーが主要な因子となります。
液体と気体の物性
密度( ρ )、粘性( μ )、表面張力( σ )、比熱( c )、熱伝導率( λ )、温度拡散率( α )等
外部から付加するエネルギー
液流速( ν )、噴射圧力( p )、噴射速度( ν )、回転数( N )、温度( T )等
外部から付加するエネルギーは、液体を不安定にする働きである一方、液体は変形に抵抗して元の安定状態に戻ろうと働きます。噴霧流における液体の安定性は、液体の慣性力、粘性力および表面張力の無次元数から導かれます。代表的な無次元数としては、レイノルズ数( Re )、ウェーバー数( We )、ジェット数( Je )、レイノルズ数とウェーバー数から導かれるスタビリティ数( St )、オーネゾルゲ数( Oh )等があります。
噴霧特性は、噴霧システムだけではなく、液体材料の物性やスプレークーラーのプロセス条件からも影響を受けます。液体の物性面では、密度や粘性、pH、分散状態、また懸濁液の場合は一次粒子の物性が影響します。プロセス条件面では、スプレークーラープロセスの形状や温度、風量、内圧等が影響します。そのため、液体材料および製造プロセスの特性を考慮し、目的とする造粒体品質が得られる噴霧システムおよび微粒化条件を決定することが重要です。
液滴の凝固
噴霧により微粒化した液滴は、スプレークーラープロセス内に連続して供給される低温気流と接触することにより、気流中に浮遊した状態で冷却凝固します。液滴の固化速度は、一般に数秒から数十秒程度となります。冷風との接触による液滴群の伝熱係数は、噴霧直後の加速時には、終端速度に達した後の自由落下区間と比べて非常に大きくなります。自由落下区間における伝熱係数は、単位空間あたりの液滴群の濃度が薄まることによって、ヌセルト数( Nu )、プラントル数( Pr )およびレイノルズ数( Re )から導かれるランツ・マーシャルの式等により推算することが可能です。しかし、落下時における液滴群の凝集や干渉、液体材料の物性およびプロセス運転条件により、実際の挙動にはばらつきが生じます。
固化速度と凝固特性は、液体材料の物性および冷却条件によっても異なります。ステアリン酸などの脂肪酸の場合は、液滴は低温気流が連続で接触することによって放熱し、材料予冷期間と呼ばれる液滴の温度低下から、凝固点降下に伴う過冷却を経て、凝固期間に移行します。凝固期間では、液滴の凝固によって凝固潜熱を放出します。凝固した造粒体は、固体冷却期間に移行して、温度が低下します。噴霧冷却凝固プロセスにおいて、液体材料の冷却凝固に要する熱量と時間は、材料の物性およびプロセスの冷風温度と風量条件から算出します。材料予冷期間は、噴霧時の液滴温度、液滴表面の伝熱係数、液体材料の定圧比熱および液相の密度等から算出します。凝固期間における固化速度は、液滴径および液体材料の凝固点、凝固潜熱、液滴表面の伝熱係数、固相の密度、固相の熱伝導率等から導かれます。固体冷却期間は、固体である造粒体の温度、固体表面の伝熱係数、固体の定圧比熱および固相の密度等から算出します。
造粒体の分離回収
造粒体は、冷却チャンバー内で旋回気流に乗った状態で落下します。液滴は、チャンバーの内壁に接触する前に冷却凝固します。適切に設計されたスプレークーラーは、製品が凝固に要する落下距離に応じた有効容積が確保されているため、固化していない製品が内壁に付着するのは最小限に収まります。造粒体の分離回収は、粉体を製品として捕集する製品回収機構および製品回収後にプロセスガスに残存する微粒子が系外に排出することを防止する最終除塵システムがあります。
製品回収機構は、冷却チャンバーの下部で直接回収する方法や、サイクロンによる回収があります。冷却チャンバーから直接回収する場合は、造粒体の落下時における固体冷却期間に応じた有効チャンバー容積が必要となるため、冷却チャンバーが高くなります。そのため、冷却チャンバーの容積は、凝固に必要な滞空時間と距離に抑え、冷却チャンバー下部に、冷却機能を有する粉体輸送ラインを組み込む場合があります。粉体輸送ラインには、振動ふるい式や流動層式などがあり、供給する冷風量を調節することによって冷却時間を制御します。冷却チャンバーを通過した微粒子は、サイクロンによって回収し、粉体輸送ラインに送ります。また、すべての製品をサイクロンで一括回収する場合もあります。メインプロセス内の主サイクロンで一括捕集した製品を、空気輸送ラインに送り、輸送上で冷却後に最終サイクロンで回収します。最終除塵システムは、主にバグフィルターを使用します。除塵システムで回収される粉体は、品質面で劣る、あるいは廃棄物となるために損失として扱われる場合があります。バグフィルターによる除塵は、単一品種を扱う場合は捕集した粉体を再利用する場合があります。多品種を扱う場合は、クロスコンタミネーションを防止するための洗浄工程が必要になります。バグフィルターの洗浄にかかる設備とオペレーション費用は高額になるため、一部の高付加価値品を除いて一般には採用されません。
スプレークーラーの生産性を高めるためには、適切な分離回収システムを選定し、捕集効率を最大化することが重要です。また、最終除塵システムについては、環境面や衛生面だけではなく、投資費用および運用コストも考慮して選定する必要があります。
プロセスフロー
以下は、オープン型およびクローズド型スプレークーラーの汎用プロセスフロー例です。
オープンサイクルシステム
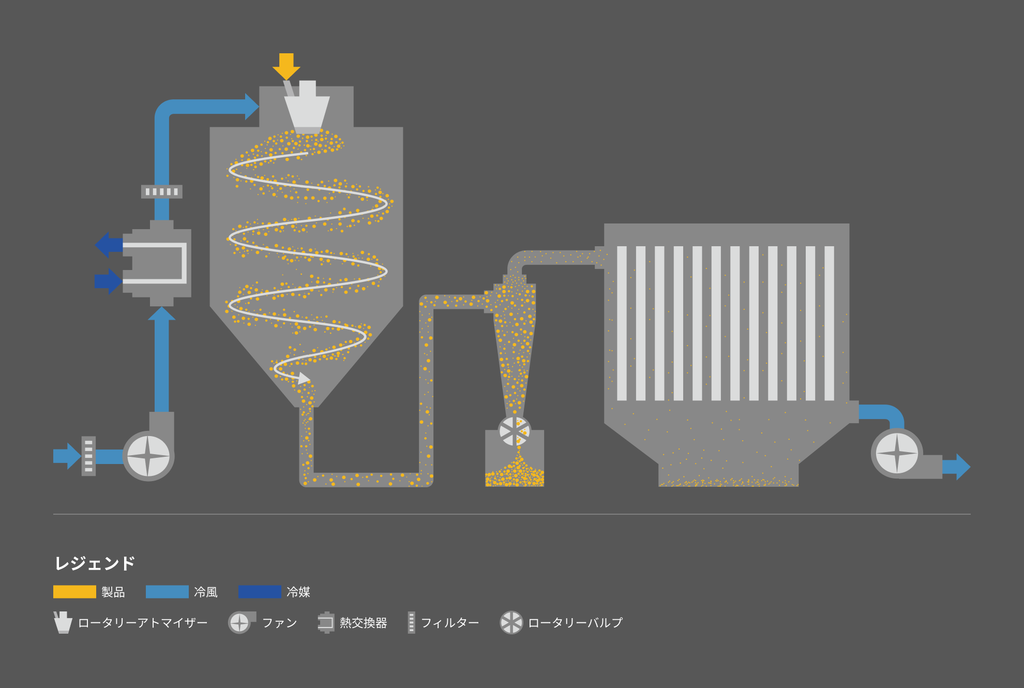
クローズドサイクルシステム
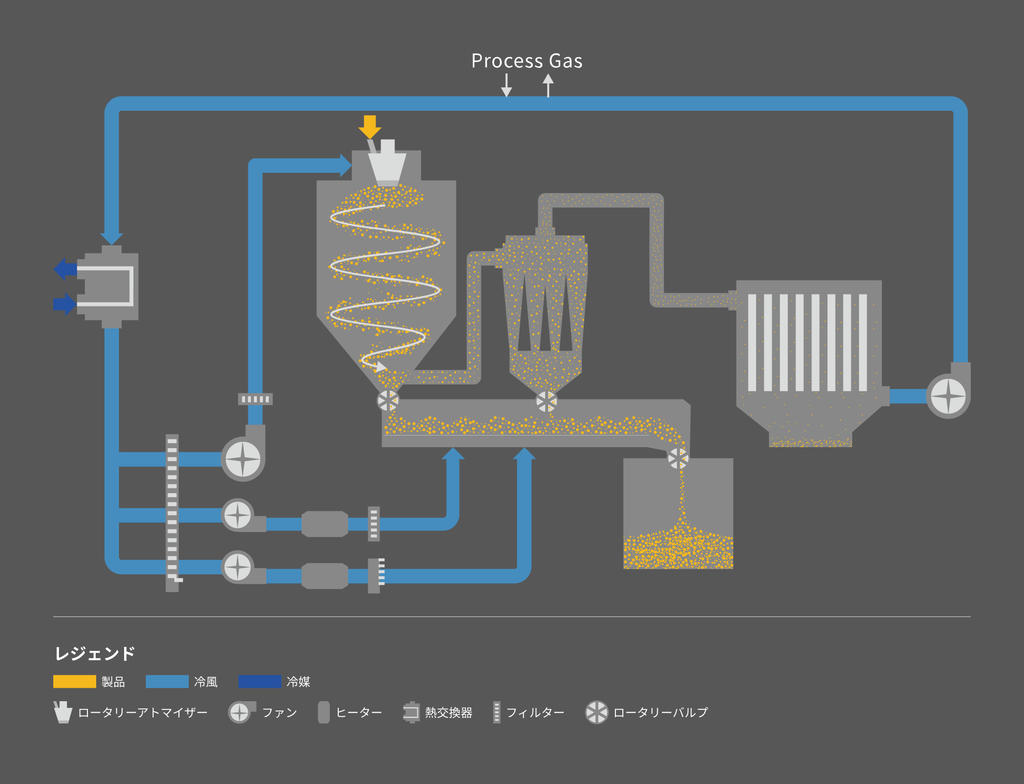
噴霧冷却凝固プロセスは、一般に以下の要素で構成されています。
液体供給システム
加熱溶融した原料液を、ポンプによって冷却チャンバーに設置された噴霧システムに送液します。供給配管上で液体温度が低下し、原料が固化して目詰まりすることを防止するため、配管温度を一定に保持します。通常は、加熱および保温したジャケット式の配管によって温度を維持します。熱媒は、一般に温水や蒸気、電気等を使用します。液体供給システムは、通常はすべて自動化された制御のもとで行われます。
冷却ガス供給システム
冷却ガスは、プロセスの入口側と出口側に組み込んだ2つのメインファンを使用して供給します。プレフィルター、高性能フィルター、HEPAフィルター等のフィルタリングシステムを組み込み、コンタミネーションを排除した清浄なガスを、後述の冷却源供給システムで冷却して供給します。供給するプロセスガス量は、物質収支および熱収支に基づき最適に計算されています。計算式には、プロセスの設置場所の温度や湿度(季節変動要因を含む)等の周囲条件も考慮され、必要に応じて除湿や予冷システムが付加されます。
冷却源供給システム
冷却源の供給は、設置場所である製造現場が保有するユーティリティの中から、製造コストや安定性、効率性を考慮した上で、最適なシステムを採用します。通常は、チラーユニットや冷水、冷媒等を組み合わせます。供給温度を精密に制御する必要がある場合は、後段にヒーターを組み込み、温度センサーのフィードバックによる自動制御を行います。
液体噴霧システム
液体供給システムから供給された溶融液を、噴霧システムにより冷却チャンバー内に噴霧します。液体の噴霧方式は、遠心噴霧方式(ロータリーアトマイザー方式)、一流体ノズル方式(加圧ノズル方式/プレッシャーノズル方式)、二流体ノズル方式、超音波ノズル方式があり、要求される粉体特性に応じて選定します(液体噴霧方式の選定はこちら)。当社の特許技術としては、プロセス内の粒度分布をリアルタイムで測定し、得た値をもとにフィードバック制御を行う粒度分布自動追従型 アトマイザーシステムがあります。この制御では、一般に行われるロータリーアトマイザーの回転数固定制御ではなく、粒度分布Dv 50(μm)が設定値となります。プロセス内の粒度分布を監視しながら、回転数が自動で調節されるため、プロセス内外の温度や湿度、圧力等の環境に変化があった場合においても、粉体の粒度を一定に保つことが可能になります。その他、コアンダ効果(流体が近くの壁面に引き寄せられる効果)を応用したコアンダディスク(特許)があります。通常のディスクと比べて噴霧液滴が下方向に向かうため、液滴の滞空時間が長く、生産効率を高める効果があります。また、当社の最新式二流体ノズルは、四流体ノズルなどの多流体ノズルと同水準の微粒化性能があり、圧縮気体の消費量を大幅に低減した上で、微粒子の製造が可能です。
冷却チャンバー
冷却チャンバー内に噴霧した液滴は、プロセス内に供給される冷風と接触し、気流中に浮遊した状態で固化します。冷風は、冷却ガス供給システムから冷却チャンバー上部のエアディスパーサーに供給されます。冷風は、エアディスパーサーにより整流され、液滴を効率良く凝固するために適正な旋回気流を作り出します。冷却チャンバーのサイズ、形状および有効容積は、造粒体の品質および要求される諸条件に基づき決定します。具体的には、物質収支および熱収支の計算結果に加えて、噴霧システムの特性と液滴の物性値から導かれる粒子の滞空時間と距離を算出して決定します。液滴の固化速度は、一般に数秒から数十秒程度となります。適切に設計されたスプレークーラーは、液滴が凝固するまでに必要な滞空時間と距離に応じた空間が確保されているため、未固化の製品が内壁に付着するのは最小限に収まります。粉体の滞留時間が短すぎる場合は、未固化の原料がプロセス内に付着する原因となります。
製品分離・回収システム
冷却チャンバーの下部で直接回収する場合は、チャンバー下部では球形に造粒された流動性の良い造粒体が得られ、サイクロンでは微粒子が得られます。サイクロンで一括捕集する場合は、スプレークーラーの生産規模や運転条件に応じて最適なサイクロンシステムを設計します。当社では、ポルトガルのACS社とのパートナーシップにより、PACyc(サイクロンにおける粒子凝集)モデルを設計最適化シミュレーションに組み込んだ高効率サイクロンを採用することも可能です。ACSの高効率サイクロンは、製品の歩留まり向上に加えて、多くのケースにおいてバグフィルター等の最終除塵システムの設置を省略することが可能です。高効率サイクロンを採用することにより、製品回収率の向上(原料損失の低減)だけではなく、バグフィルターを省略することによる設備投資費用の低減につながります。その他、製品の固体冷却期間を制御する目的として、冷却チャンバー下部に冷却機能を有する粉体輸送ラインを設置する場合もあります。粉体の冷却輸送ラインは、振動ふるい式や流動層式、空気輸送によるサイクロン回収方式があります。最終除塵システムは、バグフィルターユニットや高効率サイクロンユニットなどから、環境適合性や衛生面および設備投資とオペレーション費用を考慮して選定します。
洗浄システム
食品や医薬品などの製造プロセスまたは単一のプロセスで多品種の製造を行う場合は、スプレークーラーを定期的に洗浄する必要があります。研究用の小型装置は、洗浄性を考慮し、分解が容易でサニタリー性に優れた構造にする必要があります。小規模プロセスでは、予算上の制約によって自動洗浄システムが採用されない場合があります。一方、小ロットで多品種かつ多条件の試験を継続して行う研究機関などは、省力化の観点も考慮して自動洗浄システムを採用する場合もあります。中規模のパイロット設備や量産プラントについては、洗浄システムの導入費用やオペレーションコスト、また要求される品質水準を考慮して、適切な洗浄システムを採用する必要があります。定置洗浄(CIP)システムを導入する場合は、生産プロセスにあらかじめ洗浄設備を組み込んだ形で設計を行います。生産プロセスの仕様と原料特性を考慮し、最適な洗浄システムおよび運転プログラムを決定します。一般的なCIPシステムは、水、酸、アルカリの貯蔵タンク、バッファータンク、送液ポンプ、配管ライン、洗浄ノズルおよび各種センサー類が含まれます。洗浄工程は、一般に温水による粗洗浄から、アルカリ洗浄、酸洗浄、温水すすぎ洗浄、仕上げリンス洗浄、乾燥工程と進行します。洗浄剤や洗浄時間など、運用費用の浪費を防ぐためには、適切に設計された洗浄システムが必要です。CIPを効果的に行うためには、原料汚れの特性に応じた化学的・物理化学的な洗浄方案の策定や、生産設備の構造に適した洗浄機器の選定といった総合的なエンジニアリングが要求されます。原料固有の特性や生産プロセスの構造によっては、部分的にCOPを採用し、全体の自動洗浄と区分けすることによって、全自動のCIPシステムよりも、衛生面および安定性に優れた洗浄工程を構築することが可能な場合もあります(セミCIPシステム)。
テスト・受託加工
当社は、積み重ねた技術をもとに、データに基づく最適なスプレークーラー製造プロセスを提供しています。また、スプレークーラーのテスト・受託加工および各種分析・測定業務も承っています。粉体加工のみならず、前後工程も含めたサービスを提供しています。国内二拠点のパウダーテクニカルセンター(神奈川県川崎市)およびASEANパウダーテクニカルセンター(タイ)の計三拠点において、顧客の持つ技術的課題を解決するために日々運営しています。2023年に新設した第二パウダーテクニカルセンター(PTC2)では、国内最大規模の分析・測定装置を取り揃えています(粉体テスト・分析・測定サービス詳細/粉体委託加工サービス詳細)。当サービスをご紹介する特設サイトプリス粉ラボを新たにリリースしました。サービスや施設の詳細および技術資料もご案内していますので、ぜひアクセスしてください。