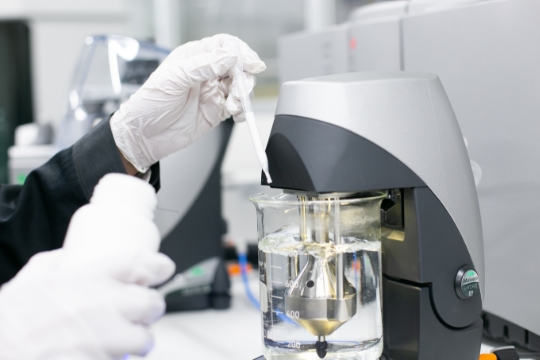
スプレードライ処理前の
原液調製からお引き受けします。
スプレードライ、フリーズグラニュレーションの前工程の原液調製から実施します。原液調製後すぐに粉体加工するため、時間経過による原液の物性変化リスクを低減できます。粉体加工を実施せずに原液調製のみのサービスもお引き受けしています。
このような課題はありませんか?
- 自社でスラリー調製し、スプレードライ受託会社に送付しているが、時間の経過により沈降・固着が発生する。スプレードライ受託会社にて再分散させているが、物性が変化している懸念がある。原液調製とスプレードライを一括で受託して欲しい。
- 自社でスラリー調製し、スプレードライ受託会社に送付しているが、時間の経過より分散剤、結合剤、可塑剤等の添加剤の物性変化、窒化系セラミックスと水との反応による物性変化が懸念される。原液調製とスプレードライを一括で受託して欲しい。
- 開発用途で原液を試作したいが、使用できる原液調製設備が小さく、一定の量で複数検体の製造が困難。
- 開発用途で原液を試作したいが、自社の原液調製設備は、既存製品製造に使用しているため、コンタミ(異物混入)リスクの懸念で使用できない。
液体を外部委託加工する際の課題
液体の経時変化による品質の不安定化

スプレードライ用途の液体は、時間の経過によって、濃縮、沈降、反応等、物性が変化することがあります。
スプレードライは、瞬間的に溶媒を蒸発させて除去し、固形物を粉体として回収するので、極端な話、液体中の溶媒分は無駄なものであり、少ない程熱効率が良くなります。したがって、溶媒の量を限界まで減らした設計で液体調製することも多々あり、物性変化にも遊びがなくなる傾向があります。
液体調製とスプレードライの受託会社が別である、または自社で原液調製しスプレードライ受託会社に送付すると、少なくとも液体調製から1~2日後のスプレードライ処理となり、物性変化のリスクが高まります。したがって、物性変化の有無をあらかじめ検討した液体設計が必要となります。
液体の委託加工のサービス内容
液体調製
50Lボールミル2台、100Lボールミル2台、ビーズミル1台、各種機械攪拌機にて液体調製します。
複数台の機器を同時に使用し、多検体の同時処理が可能です。
使用するメディアボールは、高靭性のジルコニアを選定し、コンタミリスクを極力低下させています。
品質管理
粘度計、レオメーター、レーザー回折粒度分布計での品質管理が可能です。
液体調製後、即日のスプレードライ、フリーズグラニュレーションが可能
液体調製直後にスプレードライ、フリーズグラニュレーションによる粉体化が可能です。
液体の物性変化を極力抑えるため、同日に処理することは、品質の安定化に有効です。