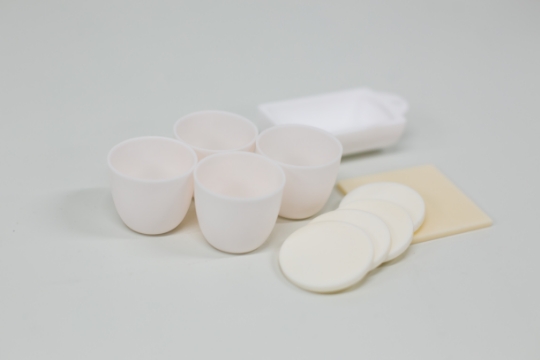
豊富な実績とスプレードライヤー
だけでなく多様な機器により、
セラミックス製品の性能向上を
支援します。
メーカーとしての装置納入や受託加工・試作テストでも数多くの実績があります。スプレードライヤーはもちろん、前工程のスラリー調製設備や後工程の一軸成形機、CIP、脱脂炉、焼成炉の保有から、各種粉体測定、成形体・焼成体密度測定、強度測定の機器も揃えています。セラミックス製造をトータルサポートします。
セラミックスのスプレードライについてこのようなお悩みはありませんか?
- 製品の性能向上のためスプレードライ造粒を検討したい。自社に設備がないのでノウハウがなく、どのように始めたらよいのかわからない。
- 自社で製造しているスプレードライ顆粒が中空状で硬く、成形体・焼成体密度が上がらないので、空孔のない中実球を製造し、性能を向上させたい。
- 自社で製造しているスプレードライ顆粒の性能を上げたいが、保有スプレードライヤーが大きく、改善のための少量試作テストを実施することが困難。
- スプレードライヤーを使用した新製品を開発したいが、自社のスプレードライヤーは、既存製品製造に使用しているため、コンタミ(異物混入)リスクの懸念から使用できない。
- 定期的に数十kg~数百kg程度の粉体が必要となるが、自社のスプレードライヤーが大きく、取り回しが悪い。
- 今までは少量試作のため、エバポレーターとふるいで簡易造粒していたが、性能が安定せず、まとまった量も生産できないので、スプレードライ造粒したい。
スプレードライが可能なセラミックスの種類
一次粒子がサブミクロン~シングルミクロン前半のセラミックススラリーであれば、基本的にスプレードライによる造粒は可能と考えられます。ノーバインダーでの造粒は粉体原料の凝集力が必要なため、サブミクロン以下が好ましいです。セラミックス粒子をコア材として樹脂や微粒子でコーティングする加工であれば、シングル~200μm程度での加工実績があります。セラミックス粒子が大きく鋭利な形状である場合、噴霧ディスクが摩耗・損傷することがあるので、注意が必要です。
下記は今まで当社で受託加工・試作テストを実施した実績の一例です。
アルミナ(Al2O3)、ジルコニア(ZrO2)、シリカ(SiO2)、窒化ケイ素(Si3N4)、サイアロン(SiAlON)、炭化ケイ素(SiC)、窒化アルミ(AlN)、酸化チタン(TiO2)、酸化マグネシウム(MgO)、チタン酸バリウム(BaTiO3)、ステアタイト(MgO・SiO2)、ムライト(3Al2O3・2SiO2)、フェライト(Fe2O3)、ジルコン(ZrSiO4)、イットリア(Y2O3)、セリア(CeO2)
セラミックスのスプレードライに求められるもの
一般的なセラミックス製品の評価を焼結体の密度・強度を主している企業が多いと思われます。
スプレードライで造粒したセラミックス顆粒に求められる特性は、焼結体の密度・強度を向上させるために、下記のような特性が求められます。
流動性の良い顆粒
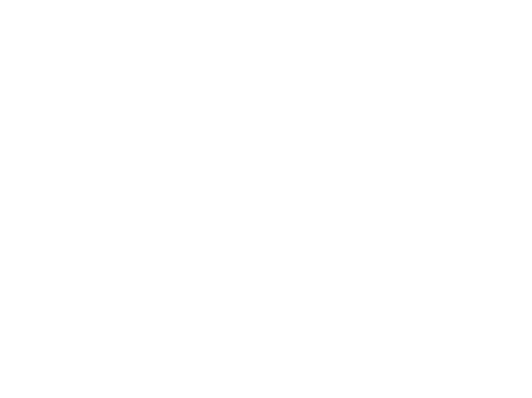
スプレードライ工程は、セラミックス製造の中間原料としての顆粒製造に使用されています。
原料粉末は焼結性の良いサブミクロン~シングルミクロン前半の微細粒子であるため、ハンドリング性に難があり流動性に乏しく、そのままでは金型に均一に充填することができません。そこで原料粉末に溶媒、結合剤、分散剤、焼結助剤、可塑剤、離型剤等、必要な助剤を添加したスラリーを調製し、スプレードライヤーで球形顆粒を造粒します。球形な数十~100μm程度の顆粒は良好な流動性を持ち、液体のようにサラサラと流れる粉となることで、後工程の成形金型に均一に充填され、プレス後の成形体が安定した高品質となり、焼成後の焼結体も高品質となります。
当社では流動性、金型への充填性の評価に、粉体特性評価装置「パウダテスタ」、パウダーレオメーター「FT4」を使用しています。
粒度分布がシャープな、微粉、粗大粒子の少ない顆粒
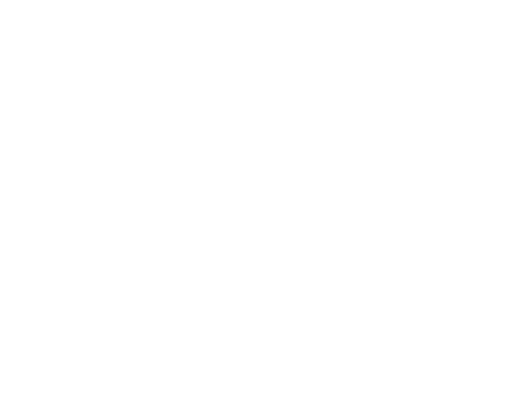
粉体を金型へ均一に充填するためには、粒度分布も重要となります。
粒子の集合体である粉体は必ず分布を持ち、微粒子は粉体の流動性を低下させるので金型への均一充填を阻害させ、粗大粒子は顆粒の強度にバラつきがあり成形体・焼結体の密度ムラの原因となります。したがって、微粒子と粗大粒子を極力少なくする、すなわち粒度分布をシャープにすることが重要です。
当社では粒度分布の評価にレーザー回折粒子径測定装置「マスターサイザー3000」、粒子画像分析装置「モフォロギG3、モフォロギ4」を使用しています。
適度な強度の顆粒
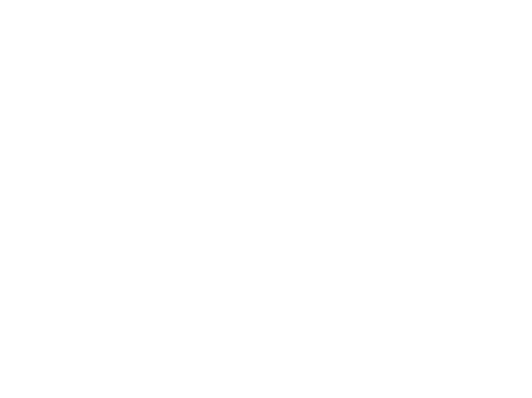
スプレードライ顆粒は、①金型へ投入するための外力によって崩壊しない強さを保ちながら均一に充填され、②充填後、プレスにて加圧された際に顆粒の態を保つこと無く、緻密に焼結されるように密に圧縮される弱さであることが求められます。①②を兼ね備えた、弱すぎず、強すぎない適度の顆粒強度が必要となります。
当社では顆粒強度の評価に、ミクロでは微小粒子圧壊力測定装置「NS-A200」、マクロではパウダーレオメーター「FT4」を使用しています。
上記の特性を備えた顆粒を製造するには、様々な試作検討が必要となります。
スプレードライ条件だけでなく、原料特性を含めたスラリー調製条件も重要となります。特にスラリーの分散性、添加剤量・種類、スラリー濃度が重要な指標となります。
当社では各種粉体測定装置、プレス機、炉、密度計、万能試験機を保有しているため、焼結体の密度・強度評価まで対応可能です。
セラミックスに関するサービス内容
- スプレードライヤーによる
受託加工・試作テスト造粒 - フリーズグラニュレーターによる
受託加工・試作テスト造粒 - 粉体の特性評価
(粒度分布、粒子形状、流動性、かさ密度、
粒子強度、比表面積、真密度、水分値) - 自動ふるい機による粉体の分級
- ビーズミル、ボールミルによる
スラリー調製 - レオメーター、レーザー回折粒度分布計、
粘度計によるスラリーの特性評価 - 一軸成形機・CIP成形機による
成形体作製(少量サンプル) - マッフル炉による成形体、粉体の仮焼き
(少量サンプル) - 管状炉による焼結体作製
(少量サンプル) - 密度計による焼結体密度評価、
万能試験機による
強度評価成形体作製(少量サンプル)
セラミックスのスプレードライ事例
スプレードライで製造した中実球と中空球の性能評価事例
結論から記載すると、乾式プレス成形から焼結体を作製する一般的なセラミックス製造工程において、スプレードライ顆粒は中空ではない、中実球(充実球)が望ましいです。顆粒中心部にポーラス(空孔)のある中空球は、顆粒外側に粒子密度が集中して高まっているので、外殻が硬くプレス成形時に密に圧縮されないため、焼成時も密度が上がらず、低密度な焼結体となってしまいます。低密度な焼結体=空孔の多い焼結体であり、強度低下、特性低下の主要因となるため、スプレードライ工程において、中空球の低減は問題提起される、よくある課題と言えます。
ここで紹介する事例では、φ0.5μmのアルミナを原料に複数の条件で調製したスラリーをスプレードライし、得られた顆粒、成形体、焼結体を評価しました。
スラリー条件
No.1 | No.2 | No.3 | |
---|---|---|---|
溶媒 | 水 | 水 | 水 |
固形分濃度 | 50w% | 50w% | 76.5w% |
バインダー濃度(PVA アルミナ比) | 0.5w% | 0.5w% | 0.5w% |
分散剤(ポリカルボン酸系 アルミナ比) | - | 0.3w% | 0.3w% |
粘度(20rpm) | 400mPa・s | 20mPa・s | 740mPa・s |
液比重 | 1.6g/mL | 1.57g/mL | 2.29g/mL |
条件No1と2の違いは分散剤の有無となります。条件No2と3の違いは固形分濃度となります。
条件No1は中濃度で分散剤を添加しない凝集系スラリー、条件No2は中濃度分散系スラリー、条件No3は高濃度分散系スラリーとして調製しました。
スプレードライ条件
使用装置 | ターニング式スプレードライヤー TR160(φ1600mm) |
---|---|
噴霧条件 | ロータリーアトマイザー 8000rpm |
温度条件 | 入口温度150℃ / 出口温度成行(条件No1.2は80~84℃、3は90~95℃) |
粉体回収 | 乾燥チャンバー下、サイクロン下の2点 |
数十μm程度の一般的なセラミックス用途のスプレードライ顆粒を得るためにアトマイザー回転数を8000rpmに設定しました。乾燥チャンバーφ1600mmのスプレードライヤーは、数十μm程度の比較的大きめの流動性の良い顆粒を得ることができて、かつ洗浄性も良いため実験機として推奨です。
入口温度はセラミックス用途としては低めの150℃に設定しました。理由としては、高濃度スラリー検体が含まれているので、乾燥が早いことが想定され、噴霧ディスク内での固着・閉塞を防止するためとなります。
出口温度は成行となりますが、条件条件No3はスラリー固形分濃度が高く、装置内に投入される溶媒が少ないため噴霧液滴が瞬間乾燥して奪われる熱量も少なくなることから、他条件と比較して高温となっていました。
SEM画像
条件No1の顆粒は、真球状であることが確認できます。
条件No2、3の顆粒は、中心部に穴が空いており、中空であることが確認できます。これらは顆粒外側が高密度となっているため、硬い顆粒となっていることが想定されます。
条件No3は一部紐状のような異形粉も確認できます。高濃度スラリーのため乾燥が早すぎたため、ディスクで適切に噴霧ができなかったことが要因と考えられます。
No毎で顆粒形状が大きく異なる理由は、スラリーの分散状態にあります。
条件No1は50w%の中濃度ですが400mPa・sの粘性があります。分散剤を添加していないため、スラリー中の一次粒子が緩く凝集してネットワークを構築しているためと考えられます(凝集系スラリー)。
条件No2、3は分散剤を添加しており、粘性もそれぞれ20、720mPa・sと低粘度となっており、一次粒子が単体、もしくは単体に近い状態で分散していると想定されます(分散系スラリー)。
下記のイラストは、噴霧した微細液滴が乾燥顆粒となるまでの過程のモデル図です。
送液されたスラリーは、ディスクにより微細に噴霧され、表面張力によって真球状の液滴となります。
分散系スラリーは、一次粒子が単体分散しており、軽く小さく外力によって動きやすい状態です。一次粒子は、液滴内の溶媒が蒸発する際に内側から外側へ移動する力、液滴表面から内部に向かって乾燥する収縮の力に応じて移動し、液滴表面に集まり密度が高くなることで硬い外殻を形成します。外殻の形成後も蒸発は続き、液面は殻内部に入って減圧されるため、最終的に外殻の最弱部が内側にへこんだ大きい陥没形状の顆粒となります。
凝集系スラリーは、一次粒子が一定の強度のネットワークを形成しているため、溶媒乾燥時の外力に負けずに構造を保持したまま、最終的に乾燥体となるため、噴霧初期の真球状に近い形状で、中空では無い中実顆粒となります。
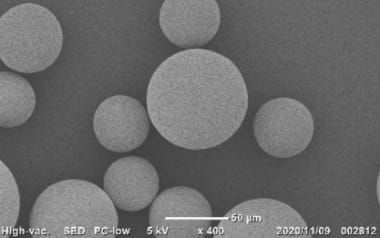
No.1 スプレードライ顆粒(中実)
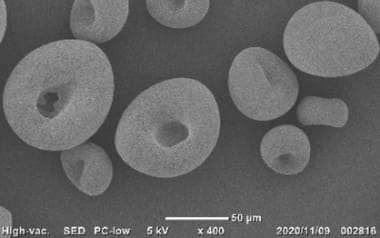
NO.2 スプレードライ顆粒(中空)
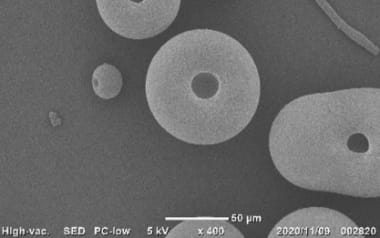
NO.3 スプレードライ顆粒(中空)
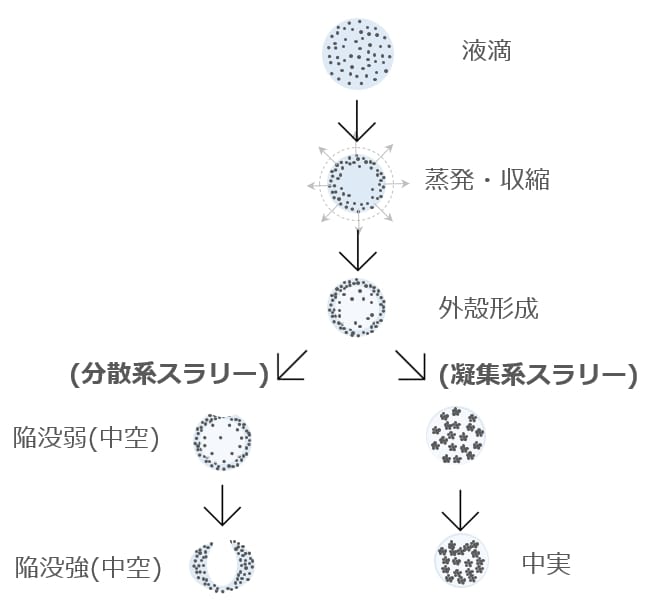
静かさ密度、安息角
真球状の条件1は、安息角が低く流動性が高いことが示されています。
条件3は、球状粒子の他に紐状の異形粒子が確認されていることから流動性が低いと想定されます。
条件3は高濃度スラリーから調製された顆粒のため、粒子単体の比重が高いので、静かさ密度が高くなっています。
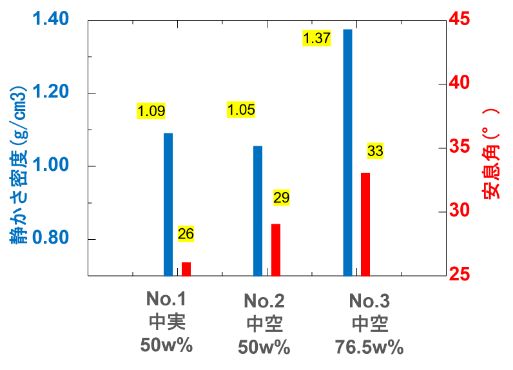
成形体・焼結体密度
プレス成形条件 | φ20mm 圧力30MPa |
---|---|
焼成条件 | 脱脂後1600℃ 2時間 |
成形体密度は、条件No3が最も高くなっていますが、こちらも静かさ密度と同様に高濃度スラリーゆえの顆粒単体比重が高いことが要因と考えられます。焼結体の密度は、条件No3が著しく低くなり、次点で条件No2、最も密度が高い=性能が高い検体は、条件No1となりました。要因としてはSEM画像でも確認された、プレス成型時に顆粒が緻密に崩壊しやすい柔らかい中実球であったことだと考えられます。条件No2は中空球で外殻が硬く潰れ性に劣っています。条件No3は高濃度スラリーであることで、さらに顆粒強度が上がったことや、紐状異形粒子の存在により低密度化したと考えることができます。
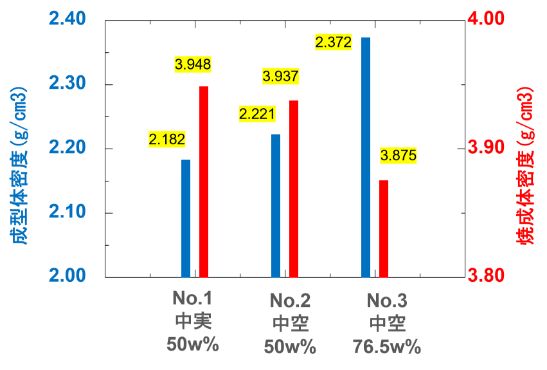
【参考文献:噴霧乾燥顆粒の構造形成過程に及ぼすスラリー特性の影響 椿純一郎 他】