Index
Spray drying
Spray drying is a continuous drying process that produces a dry powder from a liquid material by rapidly evaporating moisture with a hot gas stream. A liquid material such as a solution, gel, suspension, slurry, and emulsion is sprayed by an atomization system into a drying process where a continuous high-temperature gas stream flows. The droplets sprayed by an atomization system have an increased specific surface area, and the moisture in the liquid evaporates in seconds. The heat of the hot gas stream supplied to the process is immediately consumed as latent heat of vaporization as moisture evaporates on the surface of the droplets. Hence, spray drying is a preferred process for heat-sensitive materials such as food and pharmaceuticals. In addition, since powder can be obtained directly and continuously from liquid, spray drying is a process that can potentially eliminate multiple steps such as concentration, filtration, pulverization, mixing, classification and granulation, and integrate those processes into one step.
Spray dried granules are spherical in shape, have excellent fluidity and a sharp and stable particle size distribution. Atmospheric air is generally used as the process gas. A closed-cycle system with the use of inert gas (e.g. nitrogen) as a process gas is selected if a liquid material contains flammable organic solvents or is sensitive to oxidation. An open-cycle system for a flammable organic solvent such as ethanol can be selected for some special cases. As a safety measure, the spray drying process is precisely controlled at below 25% of the lower explosion limit (LEL) of the organic solvent gas concentration in the process. The evaporated organic solvent gas is exhausted after passing through a catalyst and the heat decomposition process.
Characteristics of spray drying
- Production process may be simplified because powder can be obtained directly from liquid.
- Heat sensitive applications are available as droplets are dried in seconds.
- Spray dried granules are spherical in shape, have excellent fluidity and a sharp PSD.
- Precise particle control is possible with a variety of atomization systems.
- Continuous process: easy to scale up and suitable for mass production.
History of spray drying
Spray drying was invented in the late 1800s. In 1865, Charles LaMont patented a method in which eggs were broken into thin droplets by a powerful jet air and dried by falling into a stream of hot air. In 1872, chemist and physician Samuel R. Percy patented a spray drying process for producing milk powder. From the 1920s until World War II, spray drying was put into practical use primarily in the production of milk powder, and its use gradually expanded to other applications. In Japan, the use of spray drying began before the World War II for manufacturing soy sauce and milk powders. Since the 1950s, researches for spray drying theory and manufacturing processes have been actively progressed, and applications have expanded to include industrial materials such as metals, ceramics, synthetic resins, and chemicals, mainly in industrialized countries including Japan. Today, spray drying is used in a wide range of industrial applications including fine ceramics, metals, and advanced material composites. In these advanced fields, process improvements in spray drying have been required differently from those in food and pharmaceutical applications. As a result, spray drying has made further technological advances as a process that allows precise controls of particle shape, particle size, structure, density, etc. In addition to traditional industries such as food and pharmaceuticals, spray drying is a foundation that supports various technologies including electronics, semiconductors, optical materials, magnetic materials, and catalysts, and has become an essential powder manufacturing process for a wide variety of industries.
Applications
Foods
Milk, Infant formula, Creamer, Whey, Lactobacillus, Lactobacillus bifidus, Lactoferrin, Coffee, Tea, Green tea catechin, Alginic acid, Collagen peptides, Keratin, Chitosan, Glucosamine, Chondroitin, Agaricus, Propolis, Yeast, Ascorbic acid, Vitamins, Citric acid, Flavonoids, Isoflavonoids, Fumaric acid, Malic acid, Succinic acid, Tartaric acid, Phytic acid, Stevia, Inulin, Tongkat ali, Moringa, Maca, Arnica, Turmeric, Coptis rhizome, Gentian, Salacia, Microcapsules such as EPA/DHA, etc., Oil emulsion microcapsules, Hydrophilic powdered oils, Coconut oil, Starch, Dextrin, Trehalose, D-mannitol, Fructose, Glucose, Oligosaccharides, Food flavorings, Spices, Seasonings (Marine products, Livestock products, Agricultural products, etc.), Powdered alcohol, Natural pigments, Synthetic colorants, Viscous agent, Bio-gum, Locust bean gum, Xanthan gum, Antioxidant, Preservatives, Quality improvers, Plant extracts, Minerals, Algae, Green juice, Fruit juice, Egg white, Processed seafood products, Plant proteins, Animal proteins, Enzyme, Animal feeds
Pharmaceuticals
Medicines, Biopharmaceuticals, Active pharmaceutical ingredients (APIs), Poorly-soluble pharmaceutical microcapsules, Colloid carriers (Liposomes, Polymeric microspheres, Polymeric nanoparticles, Microemulsions), Antibiotics, Solid dispersion formulations, Amorphous formulations, Excipients, Polyethylene glycol (PEG), Polylactic acid (PLA), Polycaprolactone (PCL), Lactic acid-glycolic acid copolymer (PLGA), Pectin, Water-soluble polymer, Carboxyvinyl polymer, Quaternary ammonium compound, Enzyme, Yeast, Herbal medicines, Brown algae extracts, Supplements
Foods
Milk, Infant formula, Creamer, Whey, Lactobacillus, Lactobacillus bifidus, Lactoferrin, Coffee, Tea, Green tea catechin, Alginic acid, Collagen peptides, Keratin, Chitosan, Glucosamine, Chondroitin, Agaricus, Propolis, Yeast, Ascorbic acid, Vitamins, Citric acid, Flavonoids, Isoflavonoids, Fumaric acid, Malic acid, Succinic acid, Tartaric acid, Phytic acid, Stevia, Inulin, Tongkat ali, Moringa, Maca, Arnica, Turmeric, Coptis rhizome, Gentian, Salacia, Microcapsules such as EPA/DHA, etc., Oil emulsion microcapsules, Hydrophilic powdered oils, Coconut oil, Starch, Dextrin, Trehalose, D-mannitol, Fructose, Glucose, Oligosaccharides, Food flavorings, Spices, Seasonings (Marine products, Livestock products, Agricultural products, etc.), Powdered alcohol, Natural pigments, Synthetic colorants, Viscous agent, Bio-gum, Locust bean gum, Xanthan gum, Antioxidant, Preservatives, Quality improvers, Plant extracts, Minerals, Algae, Green juice, Fruit juice, Egg white, Processed seafood products, Plant proteins, Animal proteins, Enzyme, Animal feeds
Chemicals
Silica, Sodium silicate, Calcium carbonate, Catalyst, Polymer, Polyvinyl alcohol (PVA), Polyethyleneimine (PEI), Polyvinylpyrrolidone (PVP), Pigment, Dye, Soap, Detergent, Surfactant, Zeolite, Cosmetics, Lignin, Ammonium sulfate, Phosphorous solution, Urea, Fertilizer, Herbicides, Pesticides, Insecticides, Ammonium carbonate, Paints, Melamine resins, Acrylic resins, Phenolic resins, Epoxy resins, Urea resins, Amino plastics, Resin emulsions, Functional plastics, Bioplastics, Biodegradable plastics, Elastomers, Latex, Vinyl chloride, Vinyl acetate, Battery materials, Titanium oxide, Phosphoric acid compounds, Calcium phosphate, Natural apatite, Methylcellulose (MC), Hydroxypropyl methylcellulose (HPMC)
Ceramics, Alloys & Powder metallurgy
Alumina (Al2O3), Zirconia (ZrO2), Silica (SiO2), Silicon nitride (Si3N4), Sialon (SiAlON), Silicon carbide (SiC), Aluminum nitride (AlN), Boron nitride (BN), Titanium oxide (TiO2), Magnesium oxide (MgO), Barium titanate (BaTiO3), Steatite (MgO・SiO2), Mullite (3Al2O3・2SiO2), Ferrite (Fe2O3), Zircon (ZrSiO4), Yttria (Y2O3), Ceria (CeO2), Cermet (TiC, TiN), Tungsten carbide (WC), Nickel alloy, Aluminum alloy, Magnesium alloy, Titanium alloy, Cobalt alloy, Rare metal, Rare earth, Bioceramics
Materials & Parts
Electronic materials, Multilayer ceramic capacitors (MLCC), Semiconductors, Insulators, Magnetic materials, Dielectrics, Glass materials, Sensors, Catalysts, Refractory materials, Pulp materials, Dental materials, Hydroxyapatite, Cellulose, Cellulose nanofibers (CNF), Synthesis rubbers, Synthetic fibers, Carbon, Graphene, Carbon nanotubes (CNT), Superconducting materials, Toners, Abrasives, Carbide tools, Optical fibers, Battery materials, Lithium ion secondary battery cathode materials, Sodium ion battery materials, All solid state battery materials
Lactose
Yeast
Citric acid
Zeolite
Alumina
Silica
Zirconia
WC-(Fe-Ni) alloy
Cobalt
Molybdenum
Yttrium oxide
Indium oxide
Process overview
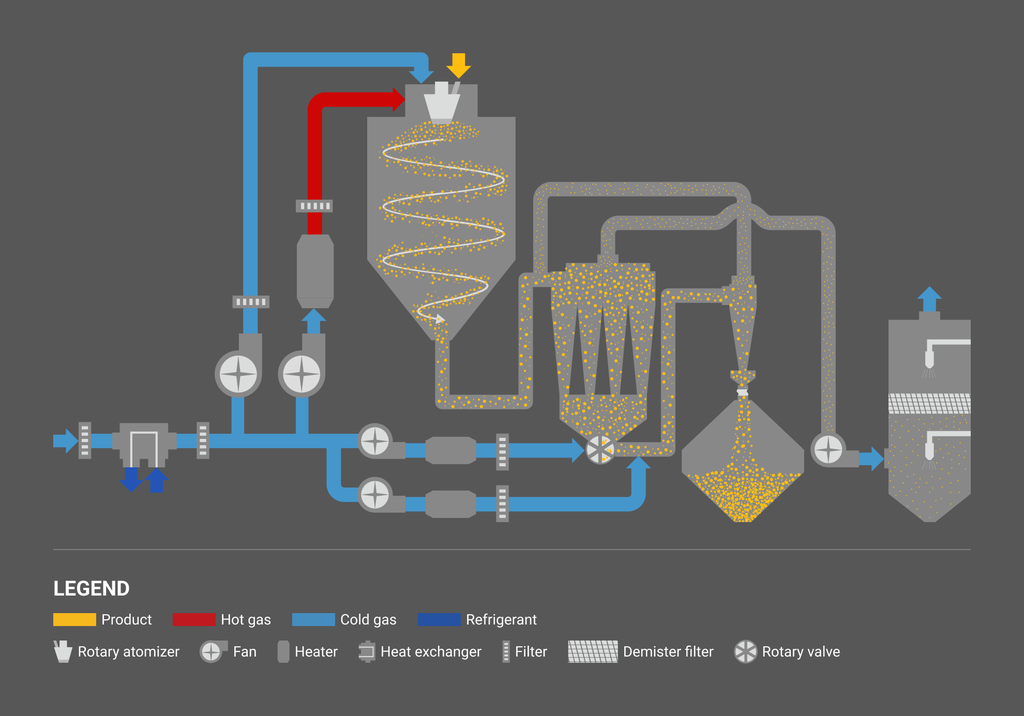
Spray drying process consists of three steps: liquid atomization, moisture evaporation of droplets, and separation and recovery of dried powder.
Liquid atomization
A liquid such as a solution, gel, suspension, slurry, and emulsion is sprayed by an atomization system into a drying process where a continuous high-temperature gas stream flows. The droplets sprayed by an atomization system have an increased specific surface area, and the moisture in the droplets evaporates in seconds. The particle size and the shape of dried powders are strongly influenced by the shape of droplets during atomization. Therefore, the first step for designing a spray drying process is to determine the right atomization system and operating conditions that can produce the desired granule quality (Click here to learn more about Liquid Atomization).
A liquid supplied to an atomization system is destabilized by the impact of internal and external energy given, causing it to flow, deform, and breakup. A supplied liquid becomes more unstable due to turbulence in the liquid as the flow rate increases. Furthermore, the addition of external forces such as air causes fragmentation, forming ligaments and droplets. External forces mainly include shear forces and forces acting on the interface between the liquid and the outside air (surface tension and negative pressure due to airflow). A state in which most of the liquid flow becomes droplets is called an atomization flow. Droplets repeat re-splitting during liquid disintegration process, becoming finer and forming an atomization flow. In theory, re-splitting is repeated until the droplet’s surface tension balances out the force caused by the irregular turbulence of the external air.
The main factors in liquid atomization are the physical properties of a liquid and a gas and the energy added externally.
Physical properties of a liquid and a gas
Density ( ρ ), Viscosity ( μ ), Surface tension ( σ ), Specific heat ( c ), Thermal conductivity ( λ ), Temperature diffusivity ( α ), etc.
Energy added externally
Liquid flow rate ( ν ), Atomization pressure ( p ), Atomization speed ( ν ), Rotational speed ( N ), Temperature ( T ), etc.
Energy added externally works to make a liquid unstable, while the liquid works to resist deformation and return to its original stable state. The stability of a liquid in an atomization flow is derived from the dimensionless numbers of the liquid’s inertial, viscous, and surface tension forces. Typical dimensionless numbers include the Reynolds number ( Re ), Weber number ( We ), jet number ( Je ), stability number ( St ) derived from Reynolds number and Weber number, and Ohnesorge number ( Oh ).
Atomization properties are influenced not only by an atomization system but also by physical properties of a liquid material and process conditions of a spray dryer. In terms of physical properties of a liquid, density, viscosity, pH, dispersion, and properties of primary particles in the case of a slurry or a suspension are affected. In the process conditions, the design of a spray dryer, process gas temperature, process gas flow, internal pressure, etc. are the properties to be affected. Therefore, it is important to consider the characteristics of the liquid material and manufacturing process and determine the atomization system and atomization conditions that will yield the desired granule quality.
Moisture evaporation of droplets
Moisture in atomized droplets comes into contact with a process hot air that is continuously supplied into a spray dryer process, and evaporates while droplets float in the process gas flow. Drying speed of droplets generally ranges from several seconds to several tens of seconds. The heat transfer coefficient of droplets is much larger during the acceleration phase immediately after atomization compared to the free fall phase after reaching the terminal velocity. The heat transfer coefficient in the free-fall phase can be estimated by Ranz and Marshall correlations derived from Nusselt number ( Nu ), Prandtl number ( Pr ) and Reynolds number ( Re ) as the concentration of droplets per unit space becomes diluted. However, actual behavior varies due to agglomeration and interference of droplets during fall-down time, physical properties of a liquid material, and process conditions.
Drying speed and properties also depend on the physical properties of a liquid material and process conditions. If a liquid material is a non-adsorptive porous material, atomized droplets receive heat through continuous contact with process hot air, and the temperature of the droplets increase during the material preheating period, before transitioning to the surface evaporation period. During the surface evaporation period, the latent heat of vaporization is consumed by moisture evaporation on the droplet surface. As a result, the droplet temperature asymptotes to the wet bulb temperature ( Tw ), which is the dynamic equilibrium temperature. During this period, all of the heat input to the droplet is used to evaporate free water on the droplet surface, so the droplet surface temperature and drying rate remain almost constant. The drying rate during the surface evaporation period is the pressure difference ( ΔP ) of water vapor partial pressure between the droplet surface and the hot air multiplied by the mass transfer coefficient on the gas side. In the case of non-adsorptive porous materials, the water vapor partial pressure on the droplet surface is equal to the saturated water vapor pressure, and even if the free water on the surface decreases, the mass transfer coefficient on the gas side does not decrease significantly. Therefore, if the temperature of the material surface does not rise, the drying rate remains almost constant, which corresponds to a constant-rate drying period. Thereafter, the droplet diameter decreases with the progress of water evaporation, and the droplet enters a falling-rate drying period as the movement of free water from the interior of the droplet to the surface is subordinated to the evaporation rate. During the a falling-rate drying period, the temperature of solid content begins to rise gradually from the surface. Since some portion of the heat received is used to raise the temperature of the material, the amount of heat used for water evaporation is reduced by a corresponding amount so that the drying rate becomes slow. The moisture content at the transition point between the constant rate drying period and the falling-rate drying period is called the critical moisture content ( Wc ).
The actual drying processes for specific liquid materials depend on the heat and mass transfer resistance occurring inside a liquid material. The mass transfer resistance of a liquid material is low due to the abundance of free water before reaching the critical moisture content. Then, as drying progresses and the moisture content decreases, the mass transfer resistance of a wet material increases.
In the case of suspensions and slurries, which are heterogeneous materials, there is generally a constant rate drying period until the moisture content reaches around 30 to 50%, and the drying rate tends to be constant. For homogeneous materials such as solutions and gels, the constant rate drying period may be short or may not exist. For example, in the case of polymer materials, a constant rate drying period may not be observed due to the diffusion movement of the moisture within the droplets. In this case, there is no constant rate drying period, so the drying rate is slow. On the other hand, in the case of salt materials, crystals precipitate on the surface of the droplet to form an outer shell, so there is a tendency for the droplet to transition from the point of shell formation to the falling-rate drying period. In the case of materials that forms an outer shell, an outer shell may rupture as the vapor pressure inside the droplets becomes higher than the outside gas pressure when the process gas temperature is above the boiling point of the liquid material. Examples of shell rupture include slurries with added binders and spray drying processes where excipients or coating materials are added to create microencapsulation. In the case of gels that have a high affinity for water, such as gelatin, or bound water, a film may form on the surface of the droplets in the early stage of drying, and the falling-rate drying period may begin from that point. Polymeric materials such as bound water that form films can also increase droplet diameter due to droplet expansion.
Moisture evaporation can also transition from a surface evaporation period to an internal evaporation period in which moisture evaporates internally and moves to the surface in vapor form. The internal evaporation period occurs during the falling-rate drying period. There are still many aspects that are not understood in the actual behavior of heat and materials in internal evaporation. The receding evaporation plane model assumes that evaporation occurs at a certain point in the interior depth. It is assumed that the droplet is divided into a dry region and a wet region, and that evaporation occurs at the interface, and the interface retreats inward as drying progresses. There is also the internal evaporation zone model, which assumes that evaporation occurs in a region rather than at an interface. The actual behavior of spray drying is that if the drying progresses to the internal evaporation period with an outer shell or film formed, the moisture that has evaporated inside cannot escape from the surface layer to the outside and the surface film may swell due to vapor pressure, the granules may burst, or they may become hollow spheres. In that case, the dried granules tend to have a high outer shell density and a low density interior. In the case of a suspension, if there are multiple primary particles contained in the droplets, and each particle size is different, segregation may occur inside the granule due to particle movement during the evaporation process.
The quality of dried powder is influenced by the internal structure of the granules. It is important to understand the particle size, shape, density, and internal structure of the granules and to appropriately adjust the liquid material properties and drying conditions.
Separation & recovery of dried powder
Dried powder falls in a swirling gas flow inside a drying chamber. Atomized droplets are dried before contacting the inner walls of the drying chamber. A properly designed spray dryer has an effective volume proportional to the distance the product must fall to dry, minimizing the amount of undried product stuck to the inner walls. Separation and recovery of dry powder includes a product recovery mechanism that collects the powder as a product and a final dust removal system that prevents fine particles remaining in the process gas from being discharged outside the process after product recovery.
Product recovery mechanisms include methods that directly collect the powder that has fallen to the bottom of the drying chamber, and methods that use a cyclone to collect the powder. Relatively light powders such as food and pharmaceuticals, and products that do not need to be classified, are generally collected in bulk using a cyclone. When collecting a powder with a cyclone, a single cyclone or multi-cyclone is used depending on the production scale and operating conditions of the spray dryer. In fields such as fine ceramics and inorganic materials, there is a method of collecting powders at two points: at the bottom of the drying chamber and at a cyclone, for the purpose of direct classification within the spray dryer process. At the bottom of the drying chamber, spherical granulated powder with good fluidity is obtained, and fine particles are collected using a cyclone. If required recovery efficiency cannot be achived using a cyclone, bulk collection can also be performed using a bag filter unit. Bulk collection using a bag filter unit is used when the particle size of the granules are fine such as single micron level or when the granules are damaged by the centrifugal force of the cyclone. There is also a process in which the product is recovered after a powder conveying system (pneumatic transportation, various feeders, etc.). The system may be equipped with a dehumidification system and temperature controls, taking into consideration the hygroscopicity of the product or oxidation countermeasures. Secondary granulation may also be achieved by incorporating a fluidized bed during the powder conveying process. In addition, in-line inspections such as sieving and metal detection may also be incorporated.
Final dust removal systems include bag filter units and wet scrubbers. Powder collected by a dust removal system may not be considered a final product in terms of quality, or it may be treated as waste and therefore a loss. When removing dust using a bag filter unit, the collected powder may be reused when handling a single variety. When handling multiple varieties of products, cleaning process is required to prevent cross-contamination. The equipment and operation costs for cleaning bag filter unit are relatively high, so the system is not generally applied except for productions of high value-added products. For food and pharmaceutical applications, wet scrubbers or wet electrostatic precipitators (WESP) are generally selected. Since these are wet processes and therefore require the installation of wastewater treatment equipment. The collected liquid materials may be concentrated and reused, or may be spray-dried again. In these cases, ancillary equipment is expensive and the quality may deteriorate due to multiple drying processes, so their actual use is limited to some special applications. An electrostatic precipitator (ESP) may be used for products that have strict environmental emission restrictions or when there are residual particles in the exhaust gas that cannot be captured by bag filters.
In order to increase the productivity of spray dryers, it is important to select an appropriate powder recovery system and maximize collection efficiency. In addition, when selecting a final dust removal system, it is necessary to consider not only environmental and sanitary aspects, but also investment costs and operating costs.
Process flows
Open-cycle system
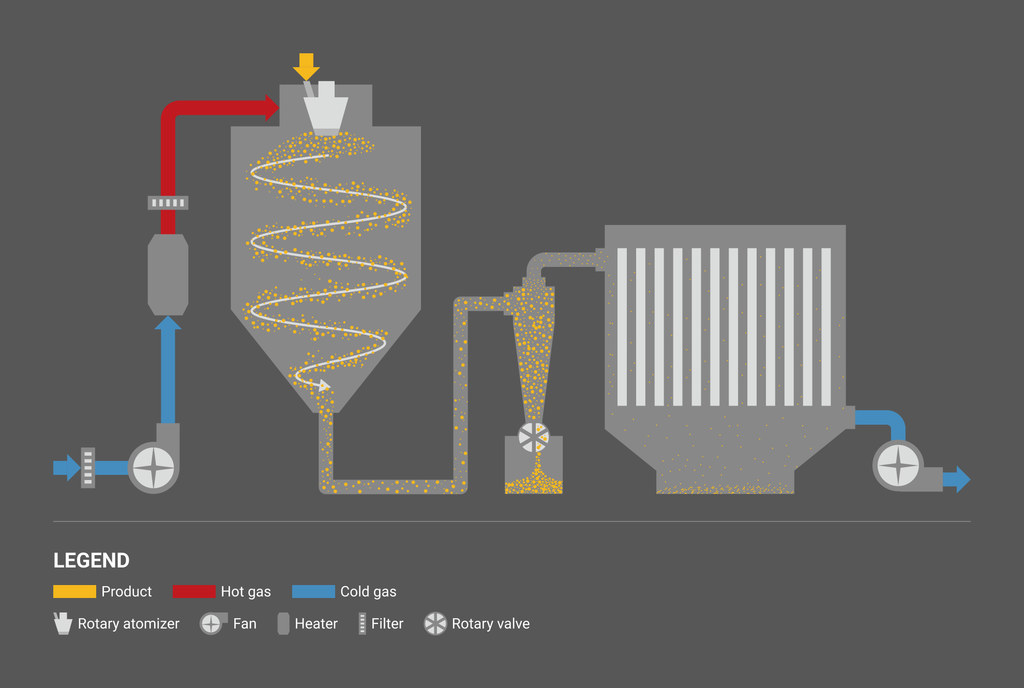
Closed-cycle system
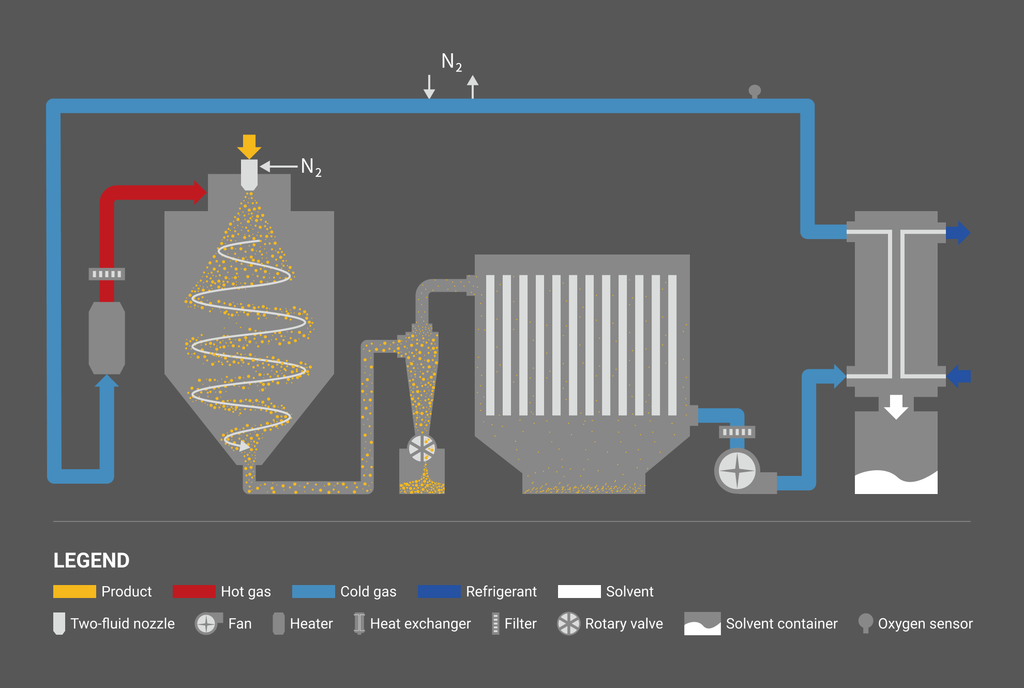
For water solvents, open-cycle systems using atmospheric air are generally selected. Closed-cycle systems where an inert gas, e.g. nitrogen, is used in the process are selected for flammable solvents as well as oxygen-sensitive or CO2-reaction-sensitive materials. We are also capable of designing dual-cycle systems, which are both open-cycle and closed-cycle systems. There are also open-cycle systems for flammable organic solvents. As a safety measure, the concentration of solvent gas in the process is controlled below 25% of the lower explosion limit (LEL), and the evaporated solvent is discharged from the system through a catalyst and/or a thermal decomposition process.
Spray drying processes generally consist of the following functions:
Liquid supply system
Liquid supply system is an integrated process line equipped with a solvent supply line such as water and a liquid material supply line. A liquid is supplied by a pump from solvent and material tanks to an atomization system installed in a drying chamber. A solvent such as water is supplied before and after supplying a liquid material. The solvent operation before supplying a liquid material is performed to stabilize the process operating conditions (process temperature, internal pressure, etc.) in advance. The purpose of the solvent operation after the liquid material operation is to completely supply all the liquid material so that nothing remains in the supply line. A liquid material may be preheated and supplied to increase the drying efficiency. Liquid supply systems are fully automated.
Process gas supply system
Process gas is supplied using two main fans integrated at the inlet and outlet of the spray drying process. The system incorporates filtering systems such as pre-filters, high-performance filters, and HEPA filters to eliminate contamination and supplies clean gas that is heated by a heat source supply system. By adjusting the process gas volume of the inlet and outlet fans, the process internal pressure is controlled to stabilize the physical properties of the spray dried granules. The amount of process gas supplied is optimally calculated based on mass and heat balances. The calculation formula also takes into account ambient conditions such as temperature and humidity including seasonal fluctuation factors at the location where the process is installed, and dehumidification and preheating systems may be added as necessary. Atmospheric air is generally used as the process gas. An inert gas, e.g., nitrogen, is used for flammable solvents as well as oxygen-sensitive or CO2-reaction-sensitive materials.
Heat source supply system
A heat source supply system plays the role of heating a spray dryer process gas. An optimal heat source supply system is selected from the utilities available at the installation site, taking into consideration operating costs, stability, and efficiency. Utilities include electricity, steam, LNG, LPG, kerosene, heavy oil, and waste heat from the factory. It is also possible to use a combination of multiple heat sources. For example, indirect heating with steam may be used primarily, with an electric heater installed at the next stage to increase control responsiveness. Direct and indirect heating systems are available depending on the acceptable cleanliness. In the case of indirect heating, it is possible to build a highly efficient energy-saving system by circulating the outlet gas of the equipped heat exchanger. It is also possible to increase energy efficiency by exchanging the waste heat from the spray dryer outlet gas. By adopting an energy-saving system, in addition to reducing operation costs, it is also effective in reducing CO2 from environmental point.
Liquid atomization system
A liquid supplied from a liquid supply system is atomized into a drying chamber by an atomization system. A variety of liquid atomization systems are available such as rotary atomizers, single-fluid nozzles (pressure nozzles), two-fluid nozzles, and ultrasonic nozzles, depending on the required powder properties (Click here to learn more about Liquid Atomization). Our patented technology, Auto PSD Control Atomizer System, measures the particle size of the powder flowing through the process in real time, and the rotational speed of the rotary atomizer is automatically adjusted by our original patented algorithm. Since the particle size is automatically controlled as a set value without fixing the rotational speed, the system can precisely keep the set PSD during the operation. In addition, our patented Coanda Disc can increase the droplet fall distance and it allows for the efficient use of chamber space. By applying the Coanda effect which is the effect that fluid is attracted to a nearby wall, the atomized droplets are directed downward and the droplets fall distance becomes longer so that it is effective to increase production efficiency. Our state-of-the-art two-fluid nozzle has the same level of performance as multi-fluid nozzles such as four-fluid nozzles, and can atomize to single microns while significantly reducing compressed gas consumption.
Drying chamber
Moisture in droplets atomized into a drying chamber comes into contact with a hot gas stream that is continuously supplied into the spray drying process and evaporates in seconds. A process gas is supplied to an air disperser installed at the top of the drying chamber. The process gas is rectified by the air disperser, creating an appropriate swirling airflow to efficiently dry the atomized droplets. The size, shape and effective volume of the drying chamber are determined based on the target properties of the powder and the required operating conditions. Specifically, in addition to the calculation of the mass balance and heat balance, the residence time and distance of the granules are calculated and determined based on the characteristics of the selected atomization system and the physical properties of the atomized droplets. Drying speed of droplets generally ranges from several seconds to several tens of seconds. A properly designed spray dryer minimizes the adhesion of undried product on internal walls by securing enough residence time and distance to be dried for atomized droplets. If the powder residence time is too short, it will cause undried material to stick in the process. On the other hand, if the residence time is too long, the powder will remain in the high-temperature process for longer than necessary, which can lead to quality deterioration. If there is a concern about thermal denaturation, or if a liquid material contains components that are highly hygroscopic or deliquescent, an air sweeper system or a multi-stage dehumidifying air supply system may be installed in the drying chamber.
Product separation & recovery system
In the case that products are collected at two points: the bottom of the drying chamber and a cyclone, spherical granules with good fluidity can be collected at the bottom of the drying chamber, and fine particles are recovered at a cyclone. Our unique technology for product recovery at the bottom of the chamber is the patented Swirl Flow Classifier HELIX. The unit incorporates a rotating vane mechanism inside the drying chamber to create a swirling flow, which can improve product recovery efficiency at the bottom of the drying chamber. HELIX uses process gas as power, so no additional modification is required and it can be operated with simple installation. When product collection is performed at a cyclone, an optimal cyclone system is designed according to the production scale and operating conditions of the spray dryer. Through our partnership with Portugal’s ACS, we may also offer high-efficiency cyclones that incorporate the PACyc (particle aggregation in cyclones) model into the design optimization simulations. In addition to improving product yield, ACS’s high-efficiency cyclones can eliminate the need for final dust removal systems such as bag filters in many cases. Adopting a high-efficiency cyclone not only improves product recovery rate (reduces raw material loss), but also reduces equipment investment costs by omitting a bag filter unit. Another method is to collect products all at once using a bag filter unit. In addition, powder transportation with dehumidification, cooling, contamination inspection, sifters, fluidized bed granulation, etc. can be incorporated into the product recovery line. Final dust removal systems are selected from bag filter units, wet scrubbers, etc., taking into consideration environmental compatibility, hygiene, capital investment, and operating costs.
Cleaning system
Spray dryers need to be cleaned regularly in food and pharmaceutical industries or when manufacturing multiple products in a single process. A small spray dryer for R&D needs to be designed to easily disassemble and have excellent sanitary properties. In small-scale spray dryers, budget constraints may preclude automated cleaning systems. On the other hand, research institutes that continuously conduct high-mix, low-volume productions, and multi-condition trials may adopt automatic cleaning systems for their efficient operations. For medium-sized pilot spray dryers and mass production plants, it is necessary to adopt an appropriate cleaning system, taking into consideration the installation cost and operation cost of the cleaning system, as well as the required quality level. When introducing a cleaning-in-place (CIP) system, the design process should include the cleaning systems and controls in advance in the overall process. We take into account the required process specifications and raw material characteristics to design the optimal cleaning systems and controls. A typical CIP system includes water, acid, and alkali storage tanks, buffer tanks, liquid pumps, cleaning nozzles, and various sensors. A general sequence control of cleaning processes is rough cleaning with hot water, alkaline cleaning, acid cleaning, hot water rinsing, final rinse, and drying. A properly designed cleaning system is required to avoid wasting operational costs such as cleaning chemicals and operation time. In order to carry out CIP effectively, comprehensive engineering is required, such as formulating chemicals and physicochemical cleaning processes according to the characteristics of raw material contamination, and selecting cleaning equipment suitable for the structure of the spray drying process. Depending on the unique characteristics of the raw materials and the structure of the production process, it may also be possible to construct a cleaning process that is more hygienic and stable than a fully automatic CIP system by partially adopting COP and separating the part from automatic cleaning of the entire process (Semi-CIP system).
Trials, contract processing & analytical measurements
We not only provide powder processing trials for spray drying, spray cooling, and freeze granulation, but also services that include pre- and post-powder processing, such as wet pulverizing, mixing, molding, sintering and freeze-drying. We operate a total of three locations: two Powder Technical Centers in Japan and ASEAN Powder Technical Center in Thailand under the partnership with T.S.K. Engineering. Our brand new Powder Technical Center 2 (PTC2), which was newly established in 2023, has one of the largest collections of analytical measurement equipment in Japan. We provide one-stop support for powder processing and analytical measurements (Powder Trials & Analytical Measurements / Contract Powder Processing).