Index
Freeze granulation
Freeze granulation is a process that produces frozen granules by atomizing a liquid mateial into an ultra-low temperature environment. The atomized droplets instantaneously get frozen and dried granules are obtained after sublimation process (freeze drying). We have developed the world’s first production scale dry cooling freeze granulation process. The process is called freeze granulation or spray freeze drying, also known as spray freeze granulation drying. Freeze granulation process is a two-step powder manufacturing process consisting of a freezing process in which a liquid material is atomized and rapidly cooled down to obtain frozen granules, and a drying process in which the frozen granules are freeze-dried to obtain dried granules. There are three types of freeze granulation processes: a wet cooling in which the liquid material is directly atomized into liquid nitrogen, a dry cooling that uses evaporated gas from liquid nitrogen, and a dry cooling using our original high-efficiency cooling system. Our latest generation “liquid nitrogen-free” dry cooling freeze granulation process using our original high-efficiency cooling system is now in mainstream. As the process does not use liquid nitrogen, it has advantages in safety, environment, installation costs, and operating costs.
Liquid materials such as solutions, gels, suspensions, slurries, and emulsions are sprayed into a freeze granulation process by atomization systems such as rotary atomizers and spray nozzles to produce frozen granules. The freezing process is continuous, while the freeze-drying process is batch-based. In order to eliminate the drawback of the batch-type freeze-drying process which is the latter stage, it is possible to process as semi-continuous production by connecting multiple freeze dryers to the freeze granulator and automatically switching connections between them.
The dried granules obtained by freeze granulation are spherical in shape, have excellent fluidity, and can maintain low density and high homogeneity. The particle size range of the granules is relatively wide, ranging from 10 to 500 µm, and the tap density equivalent to or higher than spray dried powder can be obtained. Additionally, unlike high-temperature hot gas drying processes, there is no heat effect on materials, and oxidation can be minimized.
Characteristics of freeze granulation
・Granules are spherical in shape and have excellent fluidity.
・Particle size is ranging from 10 to 500 µm with a sharp distribution.
・Precise particle control is possible with a variety of atomization systems.
・No thermal effect and oxidation can be minimized.
・Granules can maintain low density and high homogeneity.
・Excellent dispersibility for nano fibers.
History of freeze granulation
Freeze granulation was firstly published in 1975 by W. W. Rhodes and S. Prochazka on freeze granulation of ceramic powders. In the late 1980s, the Swedish Ceramic Institute (SCI) developed an experimental-scale wet cooling method in which ceramic slurry is sprayed into liquid nitrogen for freeze granulation. In 2000, the Swedish company PowderPro developed a small experimental wet-cooling freeze granulator unit. PowderPro used a general-purpose, compact freeze-drying unit for the sublimation process. Since then, freeze granulators have been considered in various research projects, but since the process uses large amounts of liquid nitrogen, there were issues in terms of safety and operating costs. Furthermore, since scale-up for mass production has not been established, no progress has been made in considering the process as an alternative process to spray dryers.
In 2016, we started testing services and product sales for wet cooling compact bench-top freeze granulator units through a joint venture with Sweden’s PowderPro. At the same time, we began our in-house R&D for scaling up a freeze granulation process. In 2019, we developed the world’s first freeze granulator CS30 (patented) for mass production using a dry cooling method. In 2020, we were awarded jointly with the National Institute of Advanced Industrial Science and Technology (AIST), Yokohama National University, and Yokohama TLO for the FY2020 Strategic Fundamental Technology Advancement Support Project by the Ministry of Economy, Trade and Industry (Project name: Research and Development of Spray Freeze Granulation Drying Process for Advanced Fine Ceramics), and further development of freeze granulators was progressed. In 2023, we developed our latest generation “liquid nitrogen-free” dry cooling freeze granulator CS220 using patented technology with our original high-efficiency cooling system. CS220 is the world’s first closed-cycle system that can be scaled up for mass production. Since liquid nitrogen is not used in the process, operating costs can be significantly reduced.
Freeze granulation vs spray drying
Freeze granulation has advantages over spray drying in terms of density and homogeneity of the granules, as well as the degree of thermal effect and oxidation.
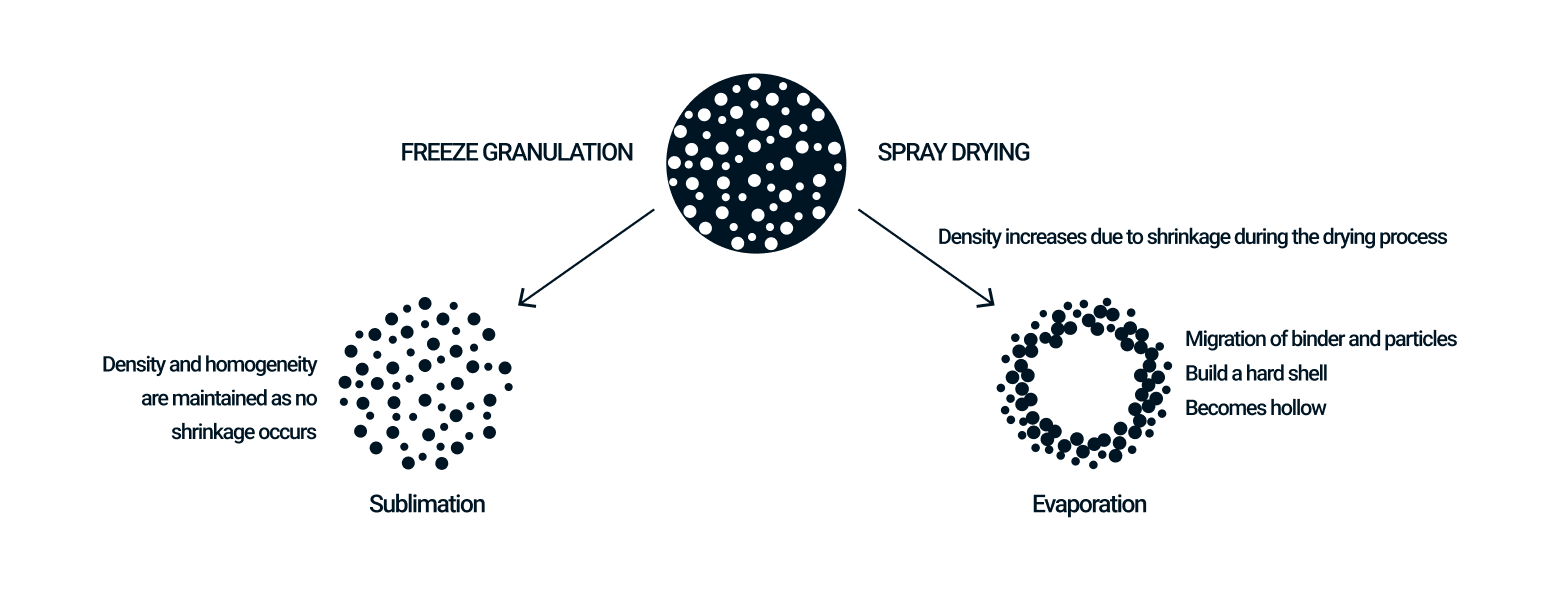
Structured granules with low density
In spray drying, moisture evaporates from the surface of a droplet, and at the same time, internal moisture moves to the surface, causing the droplet to shrink, and the solid content inside the droplet to move outward. Therefore, density of granules is higher on the outside surface than inside, so that the shape of the granules may become hollow. Freeze granulation immobilizes the internal structure of droplets containing the moisture by rapidly freezing the droplets. In freeze-drying as the post-process, the frozen moisture (ice) is dried by sublimation, resulting in extremely low material movement and shrinkage. Therefore, the granules are porous but structured, low density with no difference between inside and outside surface. Low-density structured granules contribute to improved solubility in food and pharmaceuticals, as well as properties in fine ceramics and powder metallurgy.
Case 1. Alumina
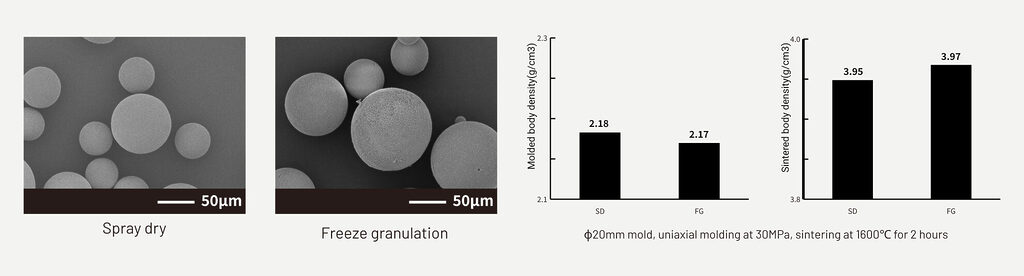
Case 2. Silica
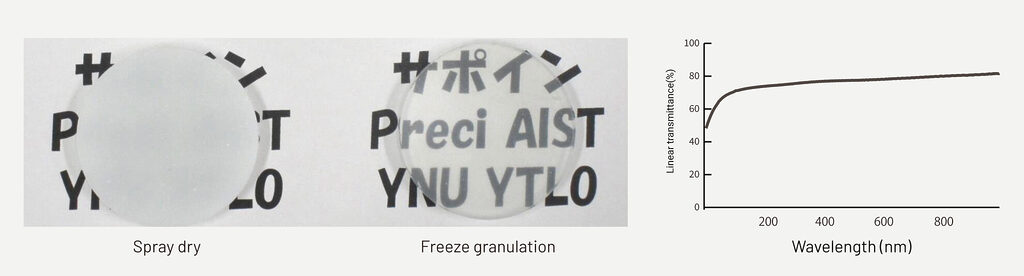
Low temperature drying
Spray drying is a drying process that produces a dry powder from a liquid material by rapidly evaporating moisture with a hot gas stream. The heat of the hot gas supplied to the process is immediately consumed as latent heat of vaporization as moisture evaporates on the surface of the droplets. Hence, spray drying is a preferred process for heat-sensitive materials such as food and pharmaceuticals. However, since hot gas is used as the drying medium, exposure to heat above room temperature is unavoidable, making it unsuitable for materials that are extremely sensitive to heat. Freeze granulation makes it possible to obtain dry powder without applying heat above room temperature.
Case 3. Lactic acid bacteria

Freeze granulation vs grinded freeze-dried products
A process similar to freeze granulation is a grinding process of freeze-dried products. A frozen material is freeze-dried and grinded after the drying process. In general, raw materials are pre-frozen in a freezer for a certain period of time. One of the examples is instant coffee production process. Freeze granulation has advantages in terms of homogeneity and fluidity of dried granules when compared to the grinding process of freeze-dried products.
Homogeneous with no segregation
The major difference between freeze granulation and the grinding process of freeze-dried products is the freezing speed. When pre-freezing in a freezer, the freezing process takes several hours, so segregation of ingredients occurs during the freezing process. In addition, if the material is a suspension, segregation due to sedimentation may be a problem. On the other hand, in freeze granulation, specific surface area of atomized droplets increases, resulting in instant freezing and the granular structure is immobilized without segregation. Even in the subsequent freeze-drying process, the moisture sublimes with almost zero material movement and shrinkage so that the dried powder can maintain a homogeneous and structured state.
Spherical with excellent flowability
Freeze granulation produces spherical frozen granules because surface tension acts on the droplets during the atomization process. Frozen granules maintain their shape even during the subsequent freeze-drying process and become dry powders with excellent flowability. On the other hand, the grinding process of freeze-dried products involves physical mechanical grinding, resulting in powders that are irregularly shaped, non-uniform, and have poor flowability.
Applications
- Fine ceramics, metals, alloys, and material composites (MMC)
- Filler powder for MIM and extrusion molding
- Thermal spray materials such as ceramics, metals, cermets, etc.
- Ceramic fluorescent plate materials for white LED
- Precursor preparation in material synthesis
- Graphene sheets and graphene oxide
- Re-dispersion treatment of nano-powders and carbon nanotubes (CNT)
- Fine nanofibers such as cellulose nanofibers (CNF)
- Carriers in catalysts
- Pharmaceutical and biopharmaceutical products
- Viable bacteria in food and pharmaceuticals
- Porous proteins
- Freeze-fixation of organic compounds in droplet state
Yeast
Lactose
Ascorbic acid
Dextrin
Cellulose nanofibers (CNF)
SUS316
Alumina
Silica
Freeze granulation is a new manufacturing process that we successfully developed in mass production for the first time in the world. Therefore, there are not many actual application cases yet. The quality of products currently manufactured using spray dryers may be improved by using freeze granulators. Compared to spray drying, freeze granulation process is not affected by heat and can produces low-density, homogeneous, and solid granules, so it is expected to contribute to product quality improvement and material development in a wide range of industrial fields in the future.
Process overview
Freeze granulation process consists of four steps: liquid atomization, freezing of droplets, separation and recovery of frozen granules, and freeze drying of frozen granules. A freeze granulator is a continuous process performing the process from liquid atomization to separation and recovery of frozen granules. Recovered frozen granules are freeze-dried by sublimating the mooisture in a batch-type freeze-drying process. In the freeze-drying process, by connecting multiple freeze dryers to a freeze granulator and automatically switching connections, it is possible to process as semi-continuous production.
Liquid atomization
A liquid such as a solution, gel, suspension, slurry, and emulsion is sprayed by an atomization system into a freeze granulation process where a continuous ultra-low temperature gas stream flows. The droplets sprayed by an atomization system have an increased specific surface area, and the moisture in the droplets gets frozen in seconds. The particle size and the shape of frozen granules are strongly influenced by the shape of droplets during atomization. Therefore, the first step for designing a freeze granulation process is to determine the right atomization system and operating conditions that can produce the desired granule quality (Click here to learn more about Liquid Atomization).
A liquid supplied to an atomization system is destabilized by the impact of internal and external energy given, causing it to flow, deform, and breakup. A supplied liquid becomes more unstable due to turbulence in the liquid as the flow rate increases. Furthermore, the addition of external forces such as air causes fragmentation, forming ligaments and droplets. External forces mainly include shear forces and forces acting on the interface between the liquid and the outside air (surface tension and negative pressure due to airflow). A state in which most of the liquid flow becomes droplets is called an atomization flow. Droplets repeat re-splitting during liquid disintegration process, becoming finer and forming an atomization flow. In theory, re-splitting is repeated until the droplet’s surface tension balances out the force caused by the irregular turbulence of the external air.
The main factors in liquid atomization are the physical properties of a liquid and a gas and the energy added externally.
Physical properties of a liquid and a gas
Density ( ρ ), Viscosity ( μ ), Surface tension ( σ ), Specific heat ( c ), Thermal conductivity ( λ ), Temperature diffusivity ( α ), etc.
Energy added externally
Liquid flow rate ( ν ), Atomization pressure ( p ), Atomization speed ( ν ), Rotational speed ( N ), Temperature ( T ), etc.
Energy added externally works to make a liquid unstable, while the liquid works to resist deformation and return to its original stable state. The stability of a liquid in an atomization flow is derived from the dimensionless numbers of the liquid’s inertial, viscous, and surface tension forces. Typical dimensionless numbers include the Reynolds number ( Re ), Weber number ( We ), jet number ( Je ), stability number ( St ) derived from Reynolds number and Weber number, and Ohnesorge number ( Oh ).
Atomization properties are influenced not only by an atomization system but also by physical properties of a liquid material and process conditions of a freeze granulator. In terms of physical properties of a liquid, density, viscosity, pH, dispersion, and properties of primary particles in the case of a slurry or a suspension are affected. In the process conditions, the design of a freeze granulator, process gas temperature, process gas flow, internal pressure, etc. are the properties to be affected. Therefore, it is important to consider the characteristics of the liquid material and manufacturing process and determine the atomization system and atomization conditions that will yield the desired granule quality.
Freezing of droplets and separation & recovery of frozen granules
There are three types of freezing processes: a dry cooling process using a liquid nitrogen-free high-efficiency cooling system, a dry cooling process using evaporated gas from liquid nitrogen, and a wet cooling process in which a liquid material is directly atomized into liquid nitrogen. Our latest generation “liquid nitrogen-free” dry cooling freeze granulation process is now in mainstream. As the process does not use liquid nitrogen, it has advantages in safety, environment, installation costs, and operating costs.
Dry cooling process using our original high-efficiency cooling system (liquid nitrogen free)
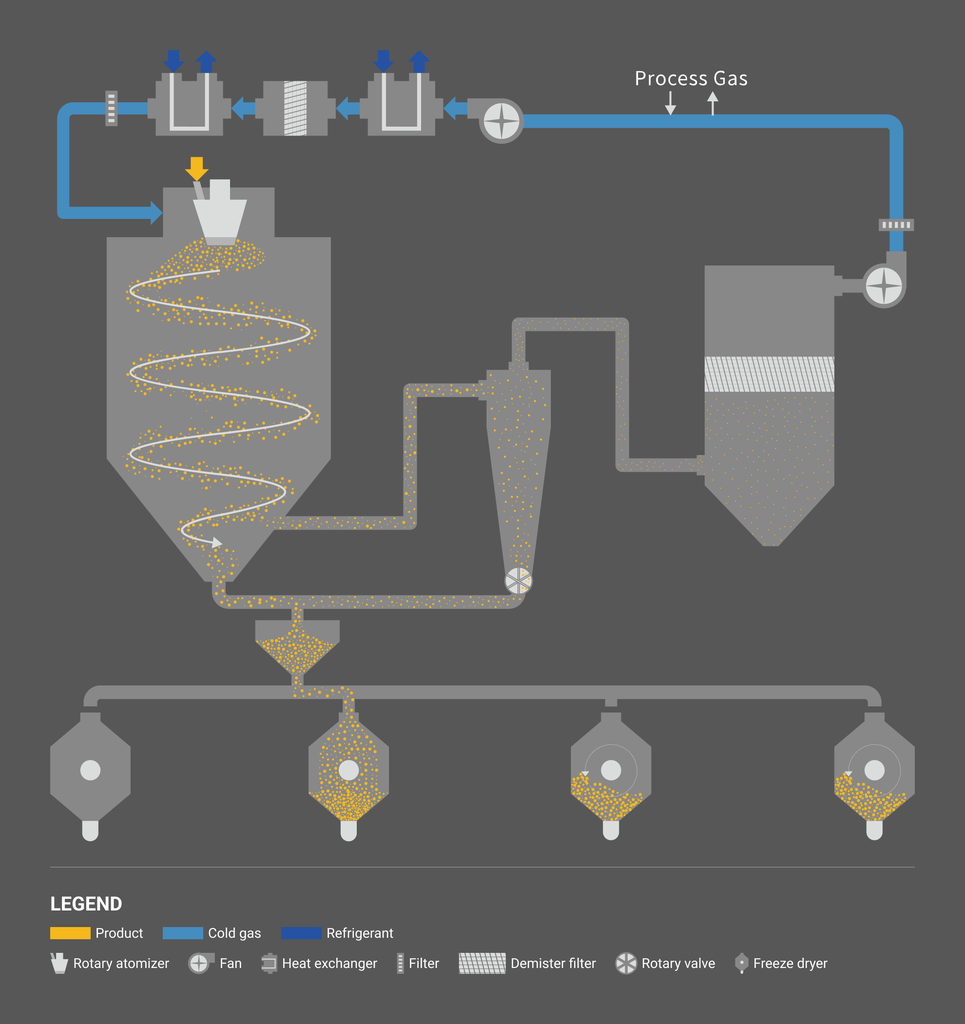
Our latest generation “liquid nitrogen-free” dry cooling freeze granulator uses patented technology with our original high-efficiency cooling system. As the process does not use liquid nitrogen, it has advantages in safety and environment, and can reduce the installation and operating cost. The process uses cold gas, similar to spray cooling. The process temperature of the cold gas used in spray cooling is generally in between 0°C and several tens of degrees Celsius, whereas the temperature applicable to the freeze granulation is in between -10°C and -50°C.
Dry cooling process using evaporated gas from liquid nitrogen
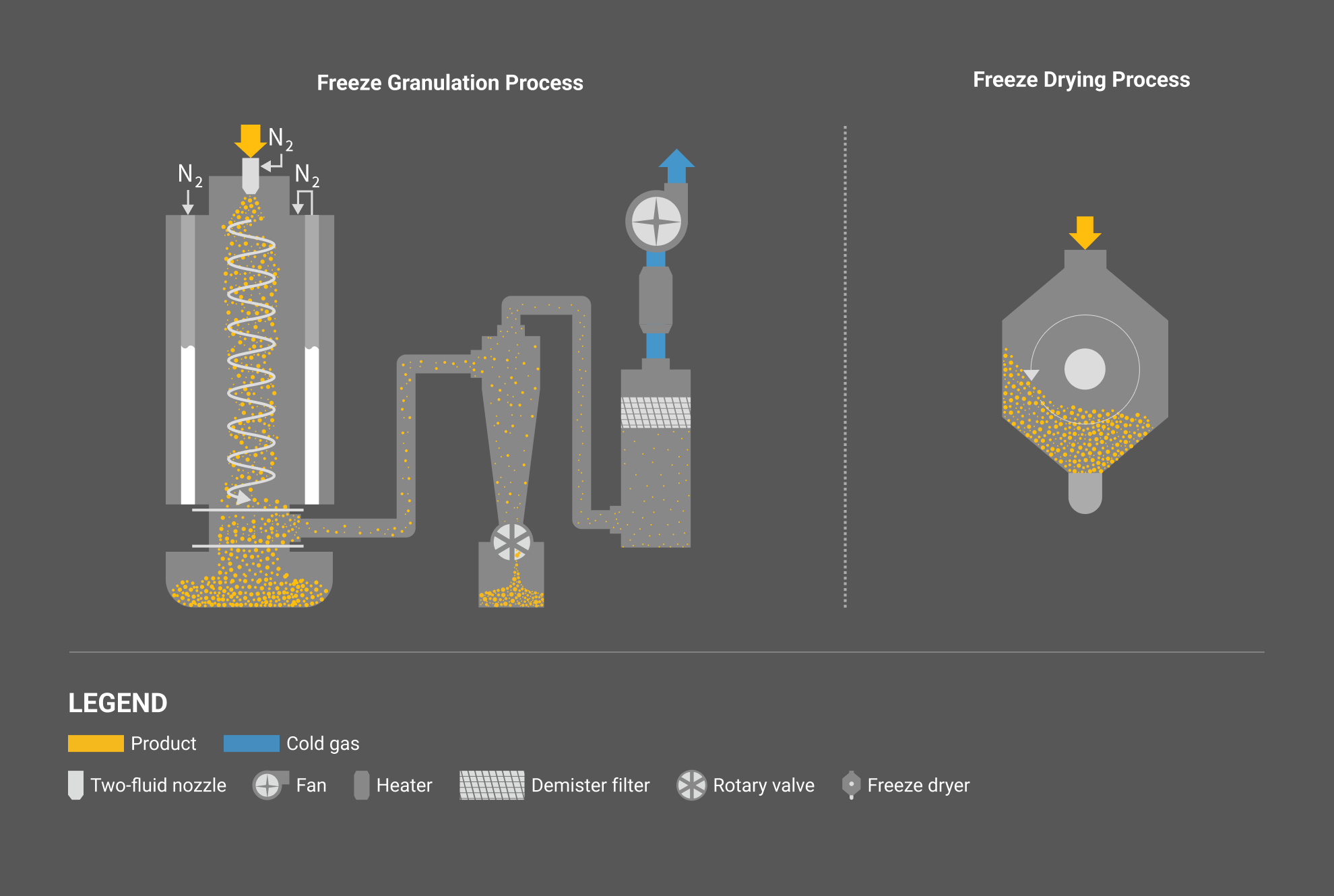
Liquid nitrogen is supplied to the outer layer of the jacketed chamber to control the process temperature. The evaporated nitrogen gas in the outer layer is supplied to the inner layer of the chamber. A liquid mateial is atomized into the inner layer by a two-fluid nozzle and the atomized droplets get frozen by contacting with the nitrogen gas. Process temperature can be controlled by adjusting the supply amount of liquid nitrogen. Frozen granules are collected in the container installed at the bottom of the chamber. The collected frozen granules are freeze-dried using freeze dryer TFD-10 or RHEOFREED. By connecting multiple freeze dryers to CS30 and automatically switching connections, it is possible to process as semi-continuous production.
Wet cooling process
A liquid mateial is atomized by a two-fluid nozzle into a container filled with liquid nitrogen. The frozen granules are deposited in the container and collected using a scoop, and manually placed to trays for freeze-drying. Freeze-drying is processed by storing trays in a multi-stage freeze dryer.
Freezing of droplets
Atomized droplets come into contact with a process cold air that is continuously supplied into a freeze granulator process, and get frozen while droplets float in the process gas flow. Freezing speed of droplets generally ranges from several seconds to several tens of seconds. The heat transfer coefficient of droplets is much larger during the acceleration phase immediately after atomization compared to the free fall phase after reaching the terminal velocity. The heat transfer coefficient in the free-fall phase can be estimated by Ranz and Marshall correlations derived from Nusselt number ( Nu ), Prandtl number ( Pr ) and Reynolds number ( Re ) as the concentration of droplets per unit space becomes diluted. However, actual behavior varies due to agglomeration and interference of droplets during fall-down time, physical properties of a liquid material, and process conditions.
Freezing speed and properties also depend on the physical properties of the liquid material and process conditions. The atomized droplets dissipate heat through continuous contact with a low-temperature air stream, and the temperature of the droplets decreases during the material pre-cooling period, passes through supercooling due to freezing point depression, and then transitions to the solidification period. During the solidification period, the solidification of droplets releases the latent heat of solidification. The solidified granules enter a solid cooling period where the temperature of the granules decreases.
In freeze granulation, the amount of heat and time required to cool and solidify (freezing) a liquid material are calculated from the physical properties of the material and the process conditions such as process gas temperature and gas flow volume. The material pre-cooling period is calculated from the droplet temperature during atomization, the heat transfer coefficient of the droplet surface, the constant pressure specific heat of the liquid material, and the density of the liquid phase. The solidification speed during the solidification period is derived from the droplet diameter, the freezing point of the liquid material, the latent heat of solidification, the heat transfer coefficient of the droplet surface, the density of the solid phase, the thermal conductivity of the solid phase, etc. The solid cooling period is calculated from the temperature of the solid granules, the heat transfer coefficient of the solid surface, the constant pressure specific heat of the solid, and the density of the solid phase.
Separation & recovery of frozen granules
Frozen granules fall in a swirling gas flow inside a freezing chamber. Atomized droplets get frozen before contacting the inner walls of the freezing chamber. A properly designed freeze granulator has an effective volume proportional to the distance the product must fall to solidify, minimizing the amount of unsolidified product stuck to the inner walls. Frozen granules are separated and collected at the bottom of the freezing chamber or by a cyclone. In fields such as fine ceramics and inorganic materials, there is a method of collecting frozen granules at two points: at the bottom of the freezing chamber and at a cyclone, for the purpose of direct classification within the freeze granulator process. At the bottom of the freezing chamber, spherical frozen granules with good fluidity can be obtained, and a cyclone collects the fines. For products that do not need to be classified according to the particle size, a bulk collection can also be performed using a cyclone. After separating and recovering the frozen granules, fine dust is removed using a demister scrubber and HEPA filter.
Collected frozen granules are freeze-dried using a freeze dryer. The freezing process is continuous, while the freeze-drying process is batch-based. In order to eliminate the drawback of the batch-type freeze-drying process which is in the latter stage, it is possible to process as semi-continuous production by connecting multiple freeze dryers to the freeze granulator and automatically switching connections between them.
Our freeze granulator can incorporate a freeze dryer RHEOFREED. RHEOFREED is a rotary freeze dryer manufactured by Kobelco Eco-Solutions. The rotating drying chamber dries frozen granules uniformly with high efficiency. Drying time can be reduced by over 50% when compared to standard freeze dryers. Powder collection and cleaning are easy thanks to the simple structure. Capacity can be scaled up from 160 to 1,000L.
Freeze-drying of frozen granules
The collected frozen granules are freeze-dried using a freeze dryer. In the freeze-drying process, the frozen moisture is removed by sublimation and the frozen granules are dried. During freeze-drying, by bringing the temperature and pressure in the process below the triple point, the moisture in the solid state sublimates into a gas without undergoing a phase transition to liquid. Since the phases of substances change in response to heat and pressure, reducing the pressure in the process lowers the boiling point of the moisture, allowing evaporation at lower temperatures. The sublimation process in freeze-drying is called primary drying.
In freeze drying, the process pressure is reduced inside the system using a vacuum pump. The moisture contained in the frozen granules undergoes a phase transition from solid to gas under reduced pressure. The vaporized steam is condensed in a cold trap (condenser) and discharged outside the process. The moisture contained in the frozen granules absorbs heat due to phase transition during sublimation. Therefore, by heating the inside of the process, the amount of heat required for the latent heat of sublimation of the frozen granules is supplemented. Sublimation proceeds from the surface of the frozen granules. The sublimation surface, which is the boundary between the dried layer and the undried frozen layer, gradually moves inward as sublimation progresses. The sublimation rate increases as the vapor pressure difference between the frozen granules and the cold trap increases, but the drying conditions must also be determined by considering the characteristics of the frozen products. The vapor generated at the sublimation surface that has migrated inside passes through the voids in the dry layer and moves to the outside. If heat is supplied to a level where the rate of vapor generation at the sublimation surface exceeds the rate of vapor movement to the outside, the degree of vacuum locally decreases inside the frozen granules, and the frozen layer may melt. Therefore, the heating temperature in the process must be kept below the eutectic point of the frozen granules.
The amount of heat absorbed for sublimation gradually decreases as sublimation progresses, and the temperature of the product, the granules, gradually increases. Frozen granules contain bound water, which is bound to constituent molecules through hydrogen bonds, and unfreeze water, which remains unfrozen even at temperatures below the freezing temperature of free water. During the sublimation process, remaining bound water and unfreeze water are removed by increasing the temperature of the process. The drying process by increasing temperature after sublimation is called secondary drying.
If the heating temperature and degree of vacuum are not set appropriately during each stage of primary and secondary drying, the granules may melt or not dry, or structural defects such as collapse, shrinkage, or cracks may occur. Therefore, in the freeze-drying process, it is important to consider the freezing characteristics and set appropriate temperature and pressure conditions.
Trials, contract processing & analytical measurements
We not only provide powder processing trials for spray drying, spray cooling, and freeze granulation, but also services that include pre- and post-powder processing, such as wet pulverizing, mixing, molding, sintering and freeze-drying. We operate a total of three locations: two Powder Technical Centers in Japan and ASEAN Powder Technical Center in Thailand under the partnership with T.S.K. Engineering. Our brand new Powder Technical Center 2 (PTC2), which was newly established in 2023, has one of the largest collections of analytical measurement equipment in Japan. We provide one-stop support for powder processing and analytical measurements (Powder Trials & Analytical Measurements / Contract Powder Processing).