SPRAY COOLER – SC
Extensive Track Record
Maximize your profit with high yield & energy savings
Accumulated experience
With our extensive track record and experience in installing large-scale plants with a maximum capacity of 12t/h, we are capable of realizing processes with high yields and low material loss.
Energy saving & Small footprint
Energy can be saved by optimizing utilities. A variety of our original technologies are available to save your footprint without compromising the capacity.
Atomization system
Rotary atomizers, Two-fluid nozzles, S-type two-fluid nozzles, Pressure nozzles, and Ultrasonic nozzles are available.
System selection
Open-cycle systems, Closed-cycle systems and Dual systems are available.
Flexible design
A wide variety of options are available including powder collection, cooling sources, cleaning systems, and controls.
Global network
We carry out projects globally by collaborating with our official engineering partners in each region under our quality management system.
Process flows
Open-cycle system
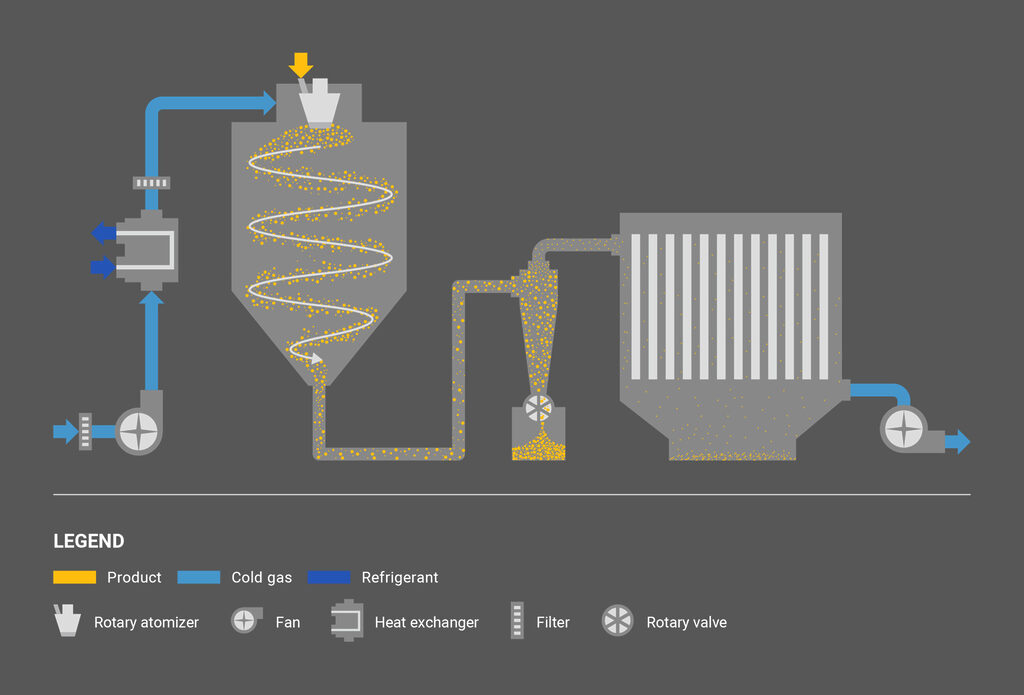
Closed-cycle system
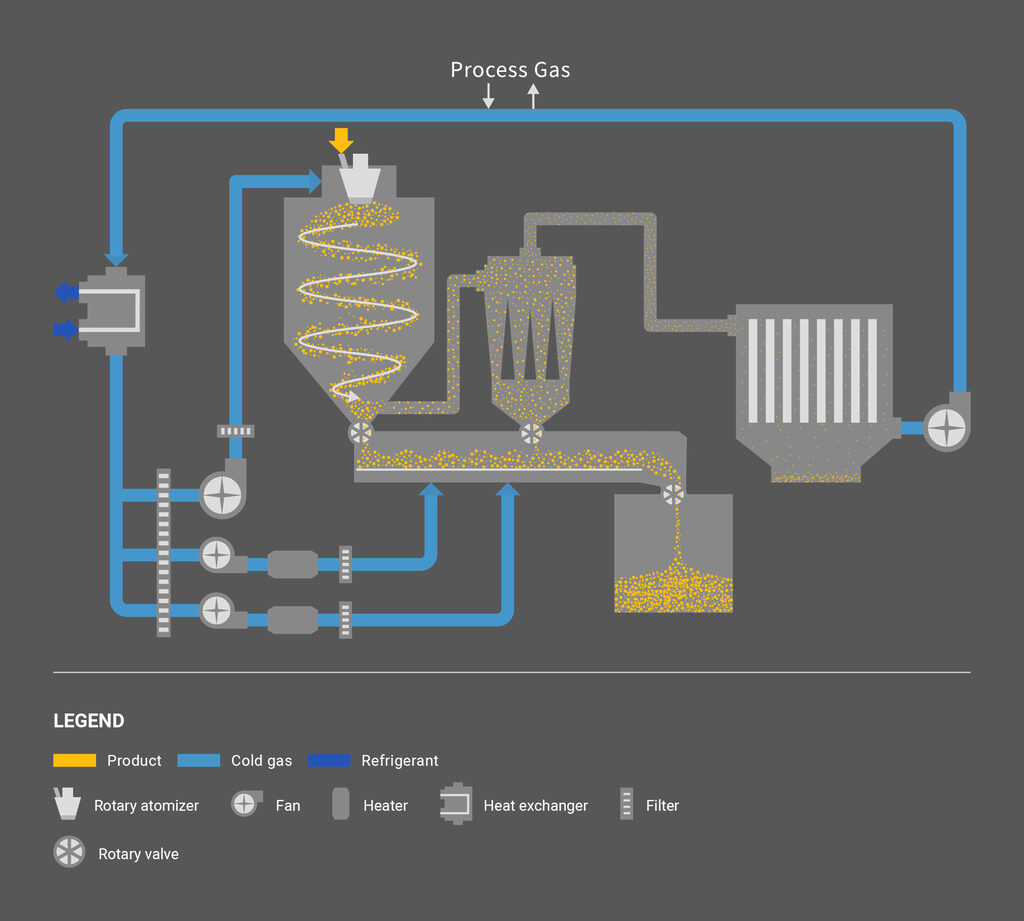
References