熱や圧力を加えることによって変形する高分子物質を総称して樹脂といいます。松ヤニやうるしなどの天然樹脂および人工的に製造された多様な合成樹脂があります。樹脂は、物性面から熱可塑性樹脂と熱硬化性樹脂に分類されます。
熱可塑性樹脂は、ガラス転移点( Tg )あるいは融点( Tm )まで加熱すると軟化します。軟化した熱可塑性樹脂を再び冷却すると固化します。そのため、熱可塑性樹脂は、与える熱を制御することによって、任意に状態変化を起こすことが可能であり、リサイクルが容易な材料といえます。熱可塑性樹脂は、一般に高分子鎖の配向度により結晶性と非結晶性に大別され、液状、ゴム状、ガラス状、結晶状の状態があります。結晶性樹脂は、融点以下の温度では、高分子鎖が規則的に配列します。非結晶性樹脂は、ガラス転移温度以下の固化した状態においても、高分子鎖が規則的に配列しません。また、熱可塑性樹脂は、耐熱性に応じて汎用プラスチックやエンジニアリングプラスチック等に分類されることもあります。汎用プラスチックは、ポリエチレン(PE)、ポリプロピレン(PP)、ABS樹脂、アクリル樹脂等があります。エンジニアリングプラスチックは、ナイロン等のポリアミド(PA)、ポリエチレンテレフタレート(PET)、ポリカーボネート(PC)、ポリエーテルエーテルケトン(PEEK)、ポリフェニレンスルフィド(PPS)、ポリテトラフロロエチレン(PTFE)等があります。また、熱を加えると軟化し、冷却するとゴム状に戻る性質を持つ熱可塑性エラストマー(TPE)も、熱可塑性樹脂に分類されます。
熱硬化性樹脂は、加熱時に一度軟化するものの、一定温度を超えると高分子鎖間の反応が三次元的な構造に進むことによって硬化します。いったん硬化した樹脂は、再加熱しても軟化しないという特徴があります。分子間の架橋結合が強固であるため、温度変化による熱影響を受けにくい反面、リサイクルが難しい材料といえます。代表的な材料としては、フェノール樹脂(PF)、エポキシ樹脂(EP)、メラミン樹脂(MF)、尿素樹脂(UF)、熱硬化性ポリイミド(PI)、熱硬化性エラストマー(飽和/不飽和)等があります。
特色のある機能を付加したプラスチックもあります。環境に配慮した生分解性プラスチックやバイオプラスチック、形状記憶樹脂、光硬化性樹脂およびガラス繊維強化プラスチック(GFRP)や炭素繊維強化プラスチック(CFRP)、木材・プラスチック再生複合材(WPRC)等の複合材料等が様々な産業界で利用されています。
合成樹脂の粉体化技術
合成樹脂の物性は多様なため、粉体化には適切な製造プロセスを選定することが重要です。粉砕処理で得られるフレークや粉末樹脂は、物理的な衝撃によって微粒化するため、摩擦による熱変性が生じます。また、粉砕時に糸引きやヒゲ状等の異形粒子が発生するため、形状はいびつになり、粒度や均一性に劣る傾向があります。当社の技術であるスプレードライ法(噴霧乾燥法)、スプレーコンジーリング法(噴霧冷却凝固法)、フリーズグラニュレーション法(凍結造粒法)は、精密な粒子制御により、球形で流動性に優れ、粒度分布がシャープな粉体を得ることが可能です。
スプレードライ法(噴霧乾燥法)
スプレードライ法で得られる乾燥粉体は、球形で流動性に優れるため、他の乾燥プロセスと比べてシャープで安定した粒度分布になります。スプレードライヤーによる樹脂原料の乾燥造粒プロセスは、緻密な熱収支計算に基づいたプロセス条件設定が必要となります。例えば、ガラス転移点( Tg )あるいは融点( Tm )が低い熱可塑性樹脂の分散液は、乾燥時の熱影響によって粉体が軟化しないプロセス温度を設定し、また噴霧液滴の滞空時間を適切に制御することが重要です。原料の熱影響を低減する目的として、除湿した低露点ガスを使用してプロセス温度を低く設定し、乾燥温度を低く保つことがあります。スプレードライヤーは、精密な粒子制御が可能な連続式の粉体製造プロセスであるため、粉砕+分級のような多段プロセスではなく、単一のプロセスで目的の造粒体を連続的に製造することが可能です。
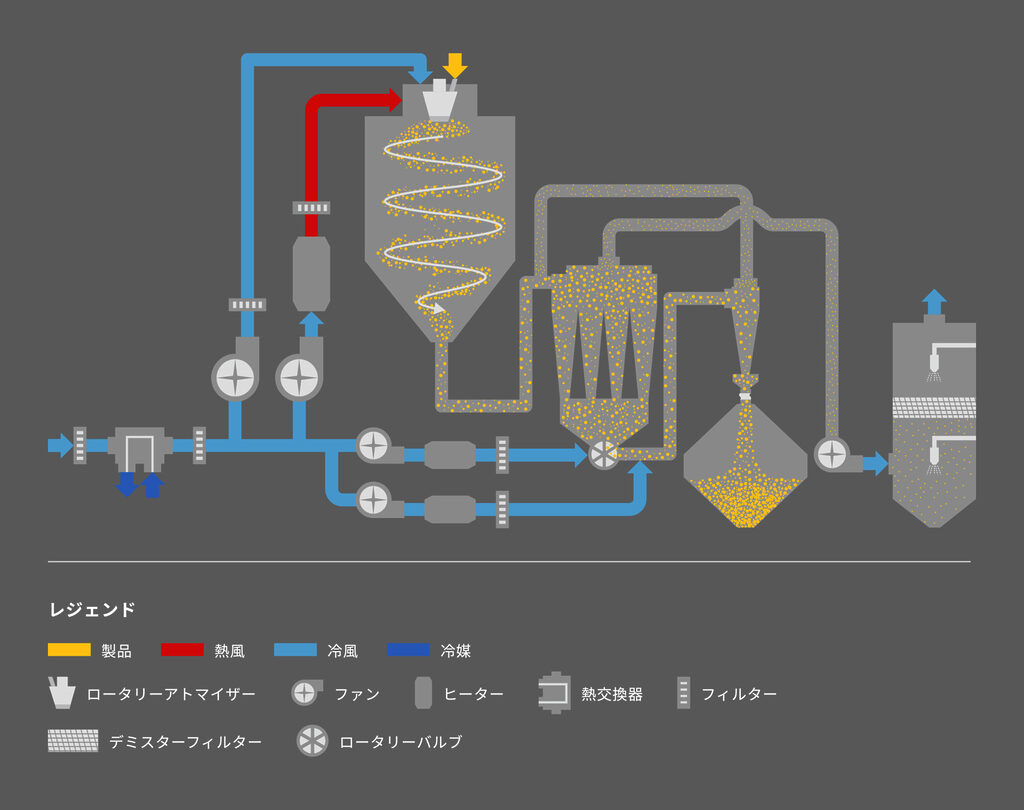
プロセスの生産効率や造粒体品質を向上させるためには、プロセス条件の最適化に加えて、原料を適切に調整することが重要です。ラテックス等の重合体の乳化分散液を噴霧乾燥する場合は、界面活性剤や電解質等の組成や添加量が引張強度と熱安定性に影響を与えます。分散液の固形分濃度は、高いほど生産効率が高まりますが、送液時の液粘性や乾燥粉体の流動性、凝集性、含水率を考慮した上で、適切に調整する必要があります。溶媒に有機溶剤を使用する、あるいは酸化を防止する必要がある場合は、プロセスガスに窒素を使用する循環式のクローズドサイクルシステムを採用します。フェノールやエポキシ等の熱硬化性樹脂の場合は、硬化温度や比熱を考慮してプロセス条件を設定します。例えば、メラミン樹脂や尿素樹脂の初期縮合品は、ホルマリンとの縮合反応で得た樹脂液をスプレードライすることによって乾燥粉体を生産します。乾燥粉体に与える熱影響を最小限におさえる必要があります。樹脂液は、200℃程度に設定された入口温度により、噴霧直後に乾燥チャンバー上部で水分蒸発します。その後、乾燥した粉体樹脂は、乾燥チャンバー下部以降で供給される冷風によって急速に冷却された後にサイクロンで回収されます。当社は、樹脂原料の物性や粒度、形状等における品質目標に応じて、最適な噴霧乾燥プロセス条件を提案することが可能です。
スプレーコンジーリング法(噴霧冷却凝固法)
スプレークーラーを用いた噴霧冷却凝固プロセスは、熱可塑性樹脂の造粒およびビーズ、プリル化が可能です。溶融樹脂液を冷却気流中に噴霧し、瞬間的に冷却凝固させ、球状の造粒体を連続的に生産します。熱可塑性樹脂の場合は、加熱した溶融液を冷却チャンバーに噴霧し、融点( Tm )より低い冷却気流を連続的に接触させることによって、冷却凝固した造粒体を生産します。固化した造粒体は、球状で流動性に優れ、シャープで安定した粒度分布が得られます。噴霧乾燥法とは異なり、原液に溶媒が殆ど存在しないことから、造粒体の粒度は大きくなります。一般には、数十μm~数mm程度の造粒体を製造することが可能です。
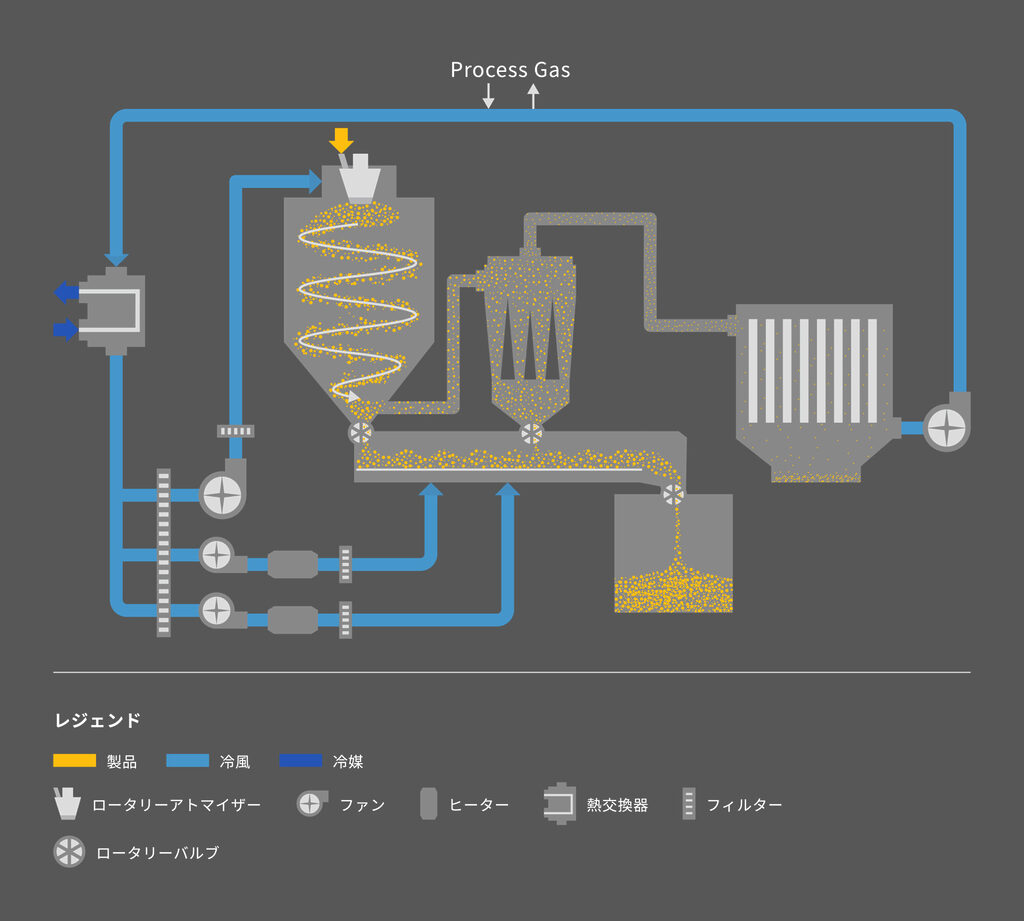
スプレーコンジーリングは、単一工程で連続的に造粒体の大量生産が可能なため、粉砕、分級、顆粒化等の下流工程を必要としない連続式の製造プロセスです。スプレークーラーは、原料液の調整やプロセス条件、運転条件を適切に設定する必要があります。プロセス設計を適切に行うことにより、目的に応じた造粒体を製造することが可能になります。当社は、樹脂原料の物性や粒度、形状等の品質目標に応じて、最適なスプレークーラープロセス条件を提案することが可能です。
フリーズグラニュレーション法(凍結造粒法)
フリーズグラニュレーション(凍結造粒)は、液体を低温環境下に噴霧することによって瞬間的に凍結させ、凍結した造粒体を凍結乾燥工程で昇華させることにより、球形で流動性に優れた造粒体を製造することが可能な粉体製造プロセスです。2019年に、当社が世界初の量産型フリーズグラニュレーター(特許)を開発しました。液体噴霧方式は、スプレードライヤーと同様にロータリーアトマイザー、二流体ノズル、超音波ノズル等が選定可能です。
フリーズグラニュレーションは、液体を低温環境下に噴霧し、急速に冷却させて凍結体を得る凍結工程と、回収した凍結体をフリーズドライヤーで凍結乾燥し、乾燥粉体を得る乾燥工程の二段の組み合わせによる粉体製造法です。凍結工程は連続式プロセスである一方、凍結乾燥工程はバッチ式となります。後段であるバッチ式の凍結乾燥工程の欠点を解消するために、回転式フリーズドライヤーを複数台配置し、前段のフリーズグラニュレーターと順番に接続することにより、連続式に近づけた製造を行うことが可能です(準連続式プロセス)。

フリーズグラニュレーションで得られる造粒体は、球形で流動性に優れ、低密度で高い均質性を保持することが可能です。造粒体は10~500µm程度の粒度範囲で制御が可能で、スプレードライ法と同等以上のタップ密度が得られます。また、高温の熱風乾燥プロセスとは異なり、樹脂への熱影響が無く、酸化を最低限にとどめることが可能です。
フリーズグラニュレーターは、スプレードライヤーと同様に、精密な粒子制御が可能なプロセスであるため、凍結粉砕プロセスと比較した場合、造粒体は球形で流動性に優れ、シャープな粒度分布を得ることが可能です。また、当社の最新型フリーズグラニュレーターであるCS220は、冷却源として液体窒素を使用しないため、凍結粉砕プロセスと比べて、オペレーションコストを大幅に低減することが可能です。
スプレードライは、通常は乾燥時に溶媒が液滴表面から蒸発すると同時に、内部の水分が表面に移動することで液滴全体が収縮します。水分の移動と同時に、液滴内の固形分が外側に移動しながら粒子構造を形成します。そのため、粒子は外殻の密度が高くなり、内部は低密度あるいは中空状になる傾向があります。フリーズグラニュレーションは、液滴を瞬間的に凍結させることで、溶媒を含む液滴内部構造を固定化します。後工程の凍結乾燥は、時間をかけて溶媒を昇華させるため、物質の移動と収縮が極めて少なく、造粒体は多孔質で低密度かつ内外の密度差がない中実球となります。

凍結造粒法は、新しい製造プロセスであることからアプリケーション事例は多くありませんが、現在スプレードライヤーで生産している製品は、フリーズグラニュレーターを採用することによって、品質の向上が見込める可能性があります。噴霧乾燥法と比べて熱影響が無く、また低密度で均質な中実顆粒が製造できることから、今後は幅広い産業分野において、製品の品質改善や新素材開発に貢献することが期待されます。
当社のスプレードライヤーおよびスプレークーラーは、樹脂の造粒工程における多数の実績があります。積み重ねた経験と実績から、要求品質を満たした最適なプロセス設計および運転条件設定を行います。スプレードライヤープロセスの諸条件を最適化し、造粒体品質をコントロールする事が可能です。液体噴霧方式は、ロータリーアトマイザー、二流体ノズル、一流体加圧ノズル、超音波ノズルから選定可能です。噴霧方式を選定する際には、噴霧液滴径だけではなく、物理的な接触および摩擦による影響も考慮にいれます。また、当社が開発したフリーズグラニュレーターは、スプレードライ製品とフリーズドライ品の粉砕製品の弱点を解決することが可能なプロセスです。凍結造粒技術については、フリーズグラニュレーション(凍結造粒)とは、ナノファイバーの分散性向上 – CNFとCNTのフリーズグラニュレーション(凍結造粒)等で紹介しています。
当社は、スプレードライヤー、スプレークーラー、フリーズグラニュレーターの粉体製造だけではなく、前後工程を含めたテスト・分析・測定サービスを提供しています。国内二拠点のパウダーテクニカルセンターおよびASEANパウダーテクニカルセンターの計三拠点において、顧客の課題を解決するために日々運営しています。2023年に新設した第二パウダーテクニカルセンター(PTC2)では、国内最大規模の分析・測定装置を取り揃えています。粉体加工だけではなく、原料調製から分析・評価までワンストップで対応する事が可能です(粉体テスト・分析・測定サービス詳細/粉体委託加工サービス詳細)。
当サービスをご紹介する特設サイトプリス粉ラボを新たにリリースしました。サービスや施設の詳細、また技術資料もご案内していますので、ぜひアクセスしてください。
※掲載している写真は、実際のプロジェクトとは異なり、イメージとして使用している場合があります。