ファインセラミックスの製造プロセスにおいて、スプレードライヤーは造粒体の製造工程で使用されています。スプレードライヤーの前段である湿式粉砕・混合工程では、数百nmから1μm程度の原料粉末が均質に分散したスラリーを製造します。その後、スプレードライヤーによってスラリーを噴霧乾燥し、数十から100μm程度の造粒体を製造します。造粒体は、スプレードライを用いることで、球形で流動性に優れ、シャープな粒度分布となります。そのため、成形時に造粒体を均質に充填することが可能となり、密度や厚みにばらつきの少ない、安定した成形体が得られます。また、成形体が均質で高密度になるため、焼成時においても高い精度で緻密化が進み、空隙率の低い高密度な焼結体が得られます。
ファインセラミックス産業において広く利用されているスプレードライ(噴霧乾燥)とは別に、フリーズグラニュレーション(凍結造粒)という新しい造粒プロセスがあります。フリーズグラニュレーション(凍結造粒)は、液体を低温環境下に噴霧することによって瞬間的に凍結させ、その凍結体を凍結乾燥工程で昇華させることで、球形で流動性に優れた造粒体を製造することが可能なプロセスです。2019年に、当社が世界初の量産型フリーズグラニュレーターを開発しました(特許)。2020年には、経済産業省による戦略的基盤技術高度化支援事業に、産業技術総合研究所、横浜国立大学、よこはまTLOと共同で採択され(研究開発計画名:高機能ファインセラミックス用噴霧凍結造粒乾燥装置の研究開発)、さらなるフリーズグラニュレーターの研究開発を進めました。2023年には、液体窒素フリーの高効率冷却ユニットによる乾式冷却方式を採用した大型フリーズグラニュレーター CS220を開発しました(特許)。液体噴霧方式は、スプレードライヤーと同様に、ロータリーアトマイザー、二流体ノズル、超音波ノズル等を使用することが可能です。
フリーズグラニュレーションは、液体を噴霧し、急速に冷却させて凍結体を得る凍結工程と、回収した凍結体をフリーズドライヤーで凍結乾燥し、乾燥粉体を得る乾燥工程の二段の組み合わせによる粉体製造法です。凍結工程は連続式のプロセスである一方、凍結乾燥工程はバッチ式となります。後段である凍結乾燥工程において、バッチ式の欠点を解消するために、回転式フリーズドライヤーを複数台配置し、前段のフリーズグラニュレーター(凍結工程)と順番に接続することにより、連続式に近づけた製造を行うことが可能です(準連続式プロセス)。
以下は、当社が過去に行った、スプレードライ法とフリーズグラニュレーション法を用いたアルミナ(Al2O3)とシリカ(SiO2)の特性比較です。
1. アルミナ(Al2O3)成形体と焼結体の密度比較
スプレードライ法とフリーズグラニュレーション法によって製造したアルミナ造粒体を乾式プレスで成形し、その後、焼結体を作製して密度を評価しました。

結果は、成形体としてはスプレードライ造粒体の密度が高くなりましたが、焼成後には、フリーズグラニュレーション造粒体が逆転して高密度になりました。フリーズグラニュレーション造粒体は、内部構造が均質で低密度になるため、金型への充填密度が低くなります。そのため、成形体密度としては、スプレードライ造粒体よりも低くなります。一方、フリーズグラニュレーション造粒体は、造粒体内部が均質であるため、焼成時において欠陥が生じにくいことから、焼結体としての密度が向上しています。
以下は、当社が、2022年に量産型フリーズグラニュレーターの初号機を納入した、産業技術総合研究所 マルチマテリアル研究部門の近藤 直樹氏を第一著者として、産業技術総合研究所、横浜国立大学および当社による研究結果になります。
Journal of the Ceramic Society of Japan(2024年、フルペーパー)
本論文では、噴霧凍結造粒乾燥(SFGD)と噴霧乾燥(SD)によって調製されたアルミナ顆粒の圧縮性と焼結性を比較しました。SFGDおよびSDにより作製した造粒体の強度、成形体と焼結体の密度、成形体の気孔径分布、SFGDおよびSD造粒体から作製した焼結体の内部構造と強度を評価しました。SFGD顆粒の強度はSD顆粒に比べて低くなりました。SFGD顆粒の顆粒強度が低いことは、グリーンボディに粒子間細孔のない均質な構造を形成するのに有利であり、その結果、焼結体の密度と強度が高まりました。
※当ページ上では、論文内の記載である「噴霧凍結造粒乾燥(SFGD)」を「フリーズグラニュレーション」、「噴霧乾燥(SD)」を「スプレードライ」と表記しています。
引用
KONDO, Naoki, et al. Compactability and sinterability of alumina granules made by spray freeze granulation drying and spray drying. Journal of the Ceramic Society of Japan, 2024, 132.4: 145-151.
Journal of the Ceramic Society of Japan(2020年、テクニカルレポート)
本テクニカルレポートでは、噴霧凍結造粒乾燥(SFGD)および噴霧乾燥(SD)プロセスを使用してアルミナ顆粒を作製し、顆粒サイズ分布、充填密度、安息角、圧縮強度などの顆粒特性を分析しました。さらに、SFGDおよびSD顆粒から粉末圧縮成形体を作成し、対応する密度と欠陥を評価しました。さらに、この成形体を焼結し、密度と強度を評価しました。SFGD造粒体の製造には、スラリー液滴を水で凍結させたため、SFGD造粒体の特性はスラリーの固形分に影響されることがわかりました。SFGD造粒体から作製した焼結体は、SFGDを用いて弱く均質な造粒体を作製したため、SD 造粒体から作製した焼結体に比べて高い強度を示しました。
※当ページ上では、論文内における記載である「噴霧凍結造粒乾燥(SFGD)」を「フリーズグラニュレーション」、「噴霧乾燥(SD)」を「スプレードライ」と表記しています。
引用
KONDO, Naoki, et al. Comparison of alumina granules prepared by spray freeze granulation drying and spray drying. Journal of the Ceramic Society of Japan, 2020, 128.11: 922-926.
2. シリカ(SiO2)成形体と焼結体の透光性比較
スプレードライ法とフリーズグラニュレーション法により製造したシリカ造粒体を乾式プレスで成形し、その後、焼結体を作製して直線透過率を評価しました。
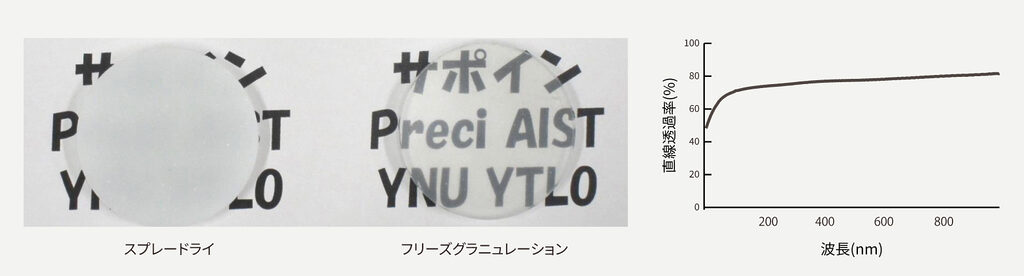
フリーズグラニュレーション造粒体は、造粒体内部が均質になります。そのため、焼結体は、光の散乱により透過率の低下を招く空孔の欠陥が少なくなることで、透光性に差が出ました。
まとめ
2019年に、当社が量産型のフリーズグラニュレーターを開発して以降、ファインセラミックスにおけるフリーズグラニュレーション造粒体の優位性が解明されてきました。フリーズグラニュレーションを用いたファインセラミックスの製造プロセスは、スプレードライでは達成できなかった水準の特性が得られる可能性があります。一方、ファインセラミックスにおける原料調合とスプレードライ(噴霧乾燥)で紹介していますが、スプレードライにおいても、造粒体の形状やサイズ、密度、内部構造を的確に把握し、原料調合とスプレードライ条件の適切な制御を行うことによって、空隙率の低い高密度の焼結体を得ることが可能です。当社は、スプレードライ法およびフリーズグラニュレーション法において、さらなる技術の進展を目指して研究開発を行い、ファインセラミックス産業の発展に貢献していきます。
当社のスプレードライヤーは、ファインセラミックスの噴霧乾燥工程における多数の実績があります。積み重ねた経験と実績から、要求品質を満たした最適なプロセス設計および運転条件設定を行います。スプレードライヤープロセスの諸条件を最適化し、造粒体品質をコントロールする事が可能です。液体噴霧方式は、ロータリーアトマイザー、二流体ノズル、一流体加圧ノズル、超音波ノズルから選定可能です。噴霧方式を選定する際には、噴霧液滴径だけではなく、物理的な接触および摩擦による影響も考慮にいれます。また、当社が開発したフリーズグラニュレーターは、スプレードライ製品とフリーズドライ品の粉砕製品の弱点を解決することが可能なプロセスです。凍結造粒技術については、フリーズグラニュレーション(凍結造粒)とは、ナノファイバーの分散性向上 – CNFとCNTのフリーズグラニュレーション(凍結造粒)等で紹介しています。
当社は、スプレードライヤー、スプレークーラー、フリーズグラニュレーターの粉体製造だけではなく、前後工程を含めたテスト・分析・測定サービスを提供しています。国内二拠点のパウダーテクニカルセンターおよびASEANパウダーテクニカルセンターの計三拠点において、顧客の課題を解決するために日々運営しています。2023年に新設した第二パウダーテクニカルセンター(PTC2)では、国内最大規模の分析・測定装置を取り揃えています。粉体加工だけではなく、原料調製から分析・評価までワンストップで対応する事が可能です(粉体テスト・分析・測定サービス詳細/粉体委託加工サービス詳細)。
当サービスをご紹介する特設サイトプリス粉ラボを新たにリリースしました。サービスや施設の詳細、また技術資料もご案内していますので、ぜひアクセスしてください。
※掲載している写真は、実際のプロジェクトとは異なり、イメージとして使用している場合があります。