FREEZE GRANULATOR – CS220
CS220 is our latest generation “liquid nitrogen-free” dry cooling freeze granulator that uses patented technology with our original high-efficiency cooling system. As the process does not use liquid nitrogen, it has advantages in safety and environment, and can reduce the installation and operating cost. Our latest generation CS220 is the world’s first closed-cycle system that can be scaled up for mass production. Since liquid nitrogen is not used in the process, operating costs can be significantly reduced. The atomized droplets come into contact with the ultra-low temperature gas flow that is continuously supplied into the process, and instantaneously get frozen. Frozen granules are collected at the bottom of the freezing chamber and the cyclone. The collected frozen granules are freeze-dried using a freeze dryer RHEOFREED. By connecting multiple freeze dryers to CS220 and automatically switching connections, it is possible to process as semi-continuous production.
Process flow
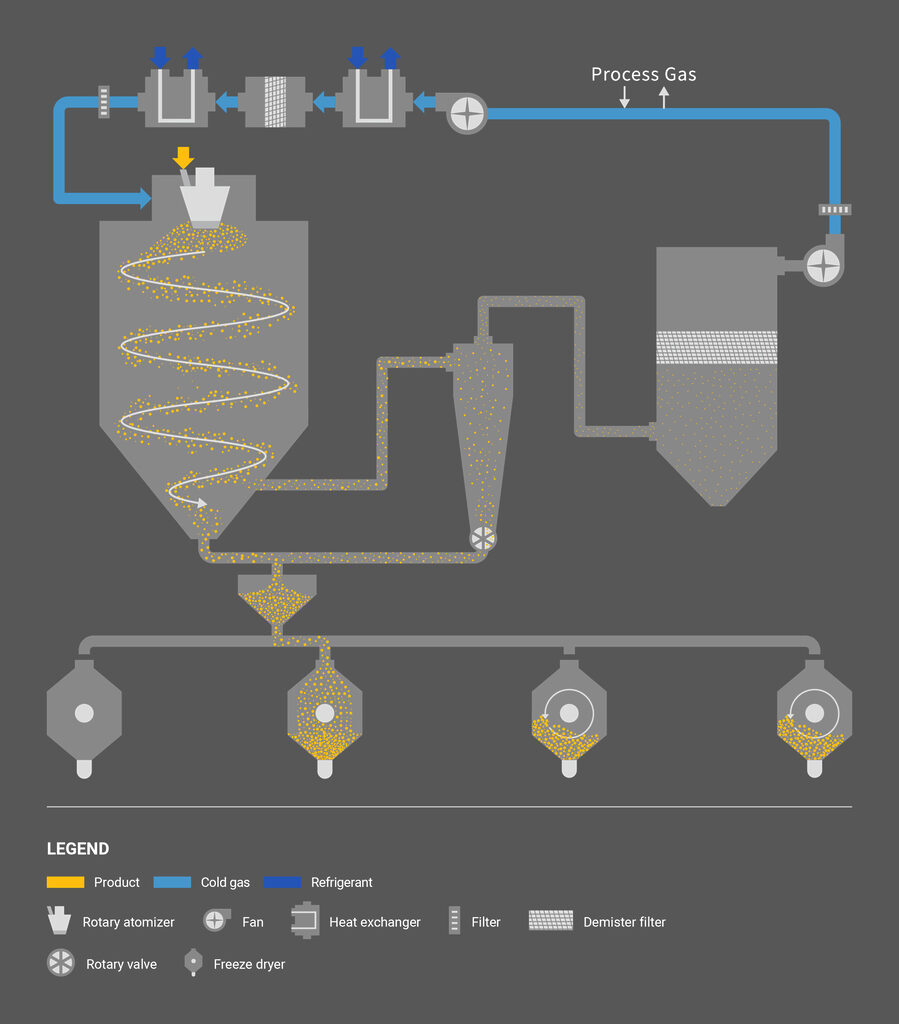
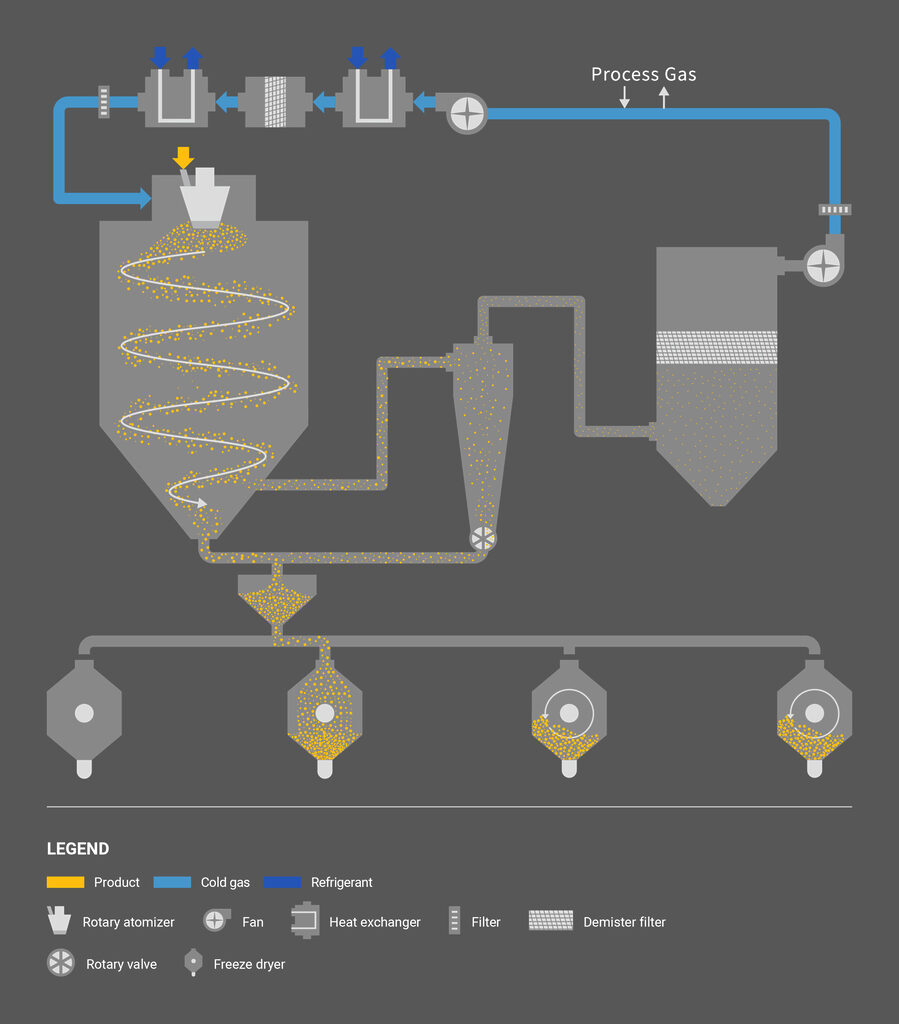
Specifications
Model | CS220 |
Chamber diameter | φ2200mm |
Atomization system | Rotary atomizers, Two-fluid nozzles, S-type two-fluid nozzles, Pressure nozzles, and Ultrasonic nozzles are available. |
Material feed capacity | Up to 320kg/h |
Cooling temperature | −10 ~ −50℃ |
Cooling system | Original high-efficiency dry cooling system |
Related Information
FREEZE GRANULATOR – CS30
CS30 is the world’s first production scale freeze granulator that uses patented technology to enable continuous production. Liquid nitrogen is supplied to the outer layer of the jacketed chamber to control the process. The evaporated nitrogen gas in the outer layer is supplied to the inner layer of the chamber. A liquid mateial is atomized into the inner layer by two-fluid nozzle and droplets are frozen by contacting with the nitrogen gas. Process temperature can be controlled by adjusting the supply amount of liquid nitrogen. Frozen granules are collected in the container installed at the bottom of the chamber. The collected frozen granules are freeze-dried using freeze dryer TFD-10 or RHEOFREED. By connecting multiple freeze dryers to CS30 and automatically switching connections, it is possible to process as semi-continuous production.
Process flow
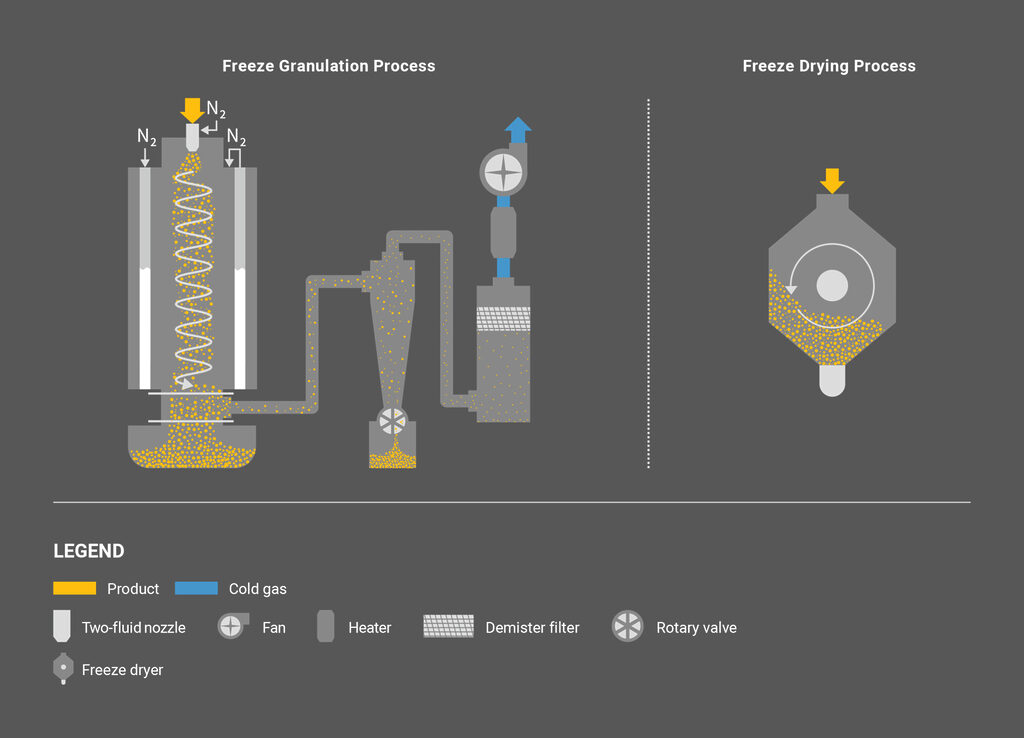
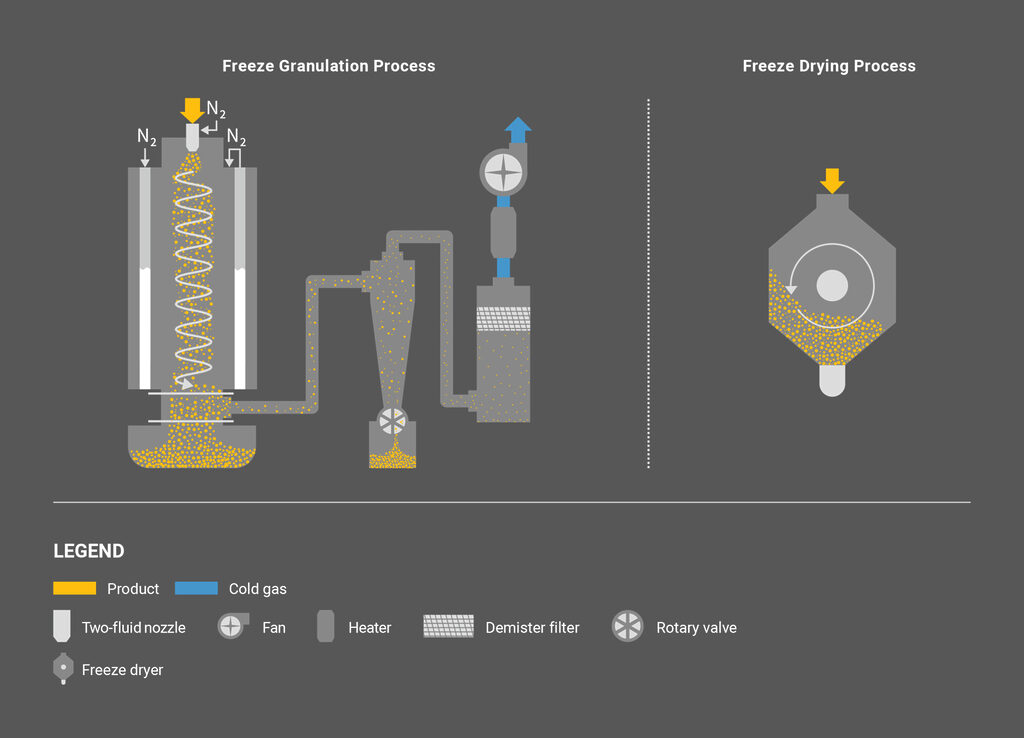
Specifications
Model | CS30 |
Chamber diameter | φ300mm |
Atomization system | Two-fluid nozzles, S-type two-fluid nozzles |
Material feed capacity | Up to 15kg/h |
Cooling temperature | −10 ~ −120℃ |
Cooling system | Dry cooling system by evaporated nitrogen gas |
Related Information
LAB FREEZE GRANULATOR – LS-6
LS-6 is a lab-scale freeze granulator unit manufactured by PowderPro. A liquid mateial is atomized by two-fluid nozzle into a container filled with liquid nitrogen. The frozen granules are deposited in the container and collected using a scoop, and manually placed to trays for freeze-drying. Freeze-drying is processed by storing trays in a multi-stage freeze dryer.
Specifications
Model | LS-6 |
Container diameter | φ120mm |
Atomization system | Two-fluid nozzles |
Material feed capacity | Up to 6kg/h |
Cooling temperature | −196℃ |
Cooling system | Wet cooling system by liquid nitrogen |